Hotline
+86-136 8495 9862
Email:cennia@szmizhi.com
Add::104,Building 27,Third Industrial Zone, Longxi Community,Longgang District,Shenzhen,China.
Coil Forming & Handling Equipment
Surface Treatment Equipment
Solutions
Application
About Us
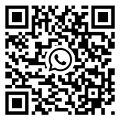
Welcome to MIZHI
For consultation/feedback, please call the service hotline: +86-136 8495 9862 Email:cennia@szmizhi.com
I. Introduction
Slitting line machine manufacturers are an integral part of the industrial manufacturing ecosystem. These manufacturers are responsible for the design, production, and distribution of slitting line machines that play a crucial role in the processing of various materials, especially metals. The quality and functionality of the slitting line machines they produce have a significant impact on the efficiency and precision of the slitting process, which in turn affects numerous downstream industries.
II. The Importance of Slitting Line Machines in Industrial Processes
1.
Material Transformation and Customization
Slitting line machines are used to convert wide coils of materials, primarily metals such as steel, aluminum, and copper, into narrower strips of specific widths. This transformation is essential for meeting the diverse requirements of different industries. For example, in the automotive industry, precisely slit metal strips are used for manufacturing components like seat frames, door panels, and engine parts. In the electronics industry, narrow metal strips are crucial for producing circuit boards and electrical connectors. By customizing the width of the material, slitting line machines enable manufacturers to optimize the use of raw materials and create products with specific dimensions.
2. Enhancing Production Efficiency
These machines significantly improve production efficiency. They can handle large coils of materials continuously, slitting them into multiple strips simultaneously. This continuous operation reduces downtime and increases the overall output of the manufacturing process. In addition, modern slitting line machines are often equipped with automated features that further streamline the process. For instance, automatic coil loading and unloading systems, as well as computer - controlled cutting parameters, minimize the need for manual intervention, saving time and reducing the risk of errors.
3. Quality Assurance in Material Processing
The slitting process performed by these machines is crucial for maintaining high - quality materials. The precision of the cutting operation ensures that the slit strips have straight edges, consistent widths, and minimal burrs or deformations. High - quality slitting line machines are designed with advanced control systems that monitor and adjust the cutting process in real - time. This results in materials that meet strict quality standards, reducing the likelihood of defects in the final products and minimizing the need for rework or scrap.
III. Types of Slitting Line Machines Manufactured
1. Metal Slitting Line Machines
Roll - slitting Machines: These are the most commonly used type for metal slitting. They utilize circular knives mounted on shafts to cut the metal coil. The coil is unwound, and the metal passes through a series of rollers that guide it to the slitting section. The circular knives can be adjusted to achieve different slit widths. Roll - slitting machines are suitable for a wide range of metals and are often used for high - volume production due to their relatively fast slitting speed.
Shear - slitting Machines: Shear - slitting machines use a shearing action to cut the metal coil. Instead of circular knives, they have a set of straight blades that move vertically or horizontally to cut the metal. Shear - slitting is preferred for thicker metals or when a more precise cut is required. The shearing process can provide cleaner cuts with less deformation compared to some roll - slitting methods.
Laser - slitting Machines: Laser - slitting machines are emerging as a high - tech option. They use high - power lasers to cut the metal coil. The laser beam is focused onto the metal surface, melting or vaporizing the material to create a slit. Laser - slitting offers extremely high precision and can handle complex cutting patterns. It is suitable for cutting thin and delicate metals as well as materials with special requirements.
2. Non - metal Slitting Line Machines
Plastic Film Slitting Machines: In the packaging industry, plastic film slitting machines are widely used. These machines are designed to slit large rolls of plastic films into narrower rolls of the desired width. The slitting process for plastic films may involve different techniques such as razor - blade slitting or hot - wire slitting. Razor - blade slitting is similar to the roll - slitting of metals but with specialized blades for plastic. Hot - wire slitting uses a heated wire to cut the plastic film by melting it.
Paper Slitting Machines: Paper slitting machines are used in the paper and printing industries. They can handle different types of paper, including newsprint, cardboard, and specialty papers. The slitting process for paper may involve cutting with circular knives or using score - and - tear methods. Score - and - tear slitting creates a weakened line in the paper, allowing it to be easily torn along the desired width.
IV. Key Considerations in the Manufacturing of Slitting Line Machines
1. Machine Design and Engineering
Mechanical Structure: The design of the slitting line machine starts with the mechanical structure. The frame of the machine must be sturdy enough to withstand the forces during the slitting operation. It is usually made of heavy - duty steel and is carefully engineered to ensure stability and durability. The rollers used for guiding and feeding the material need to be precisely machined to provide smooth and accurate movement. The shafts for holding the cutting tools, whether circular knives, shearing blades, or laser - generating components, must be designed with high precision to ensure proper alignment and rotation.
Cutting Mechanism Design: The design of the cutting mechanism depends on the type of slitting machine. For roll - slitting machines, the circular knives need to be carefully selected and mounted. The knives should have the right hardness, sharpness, and wear - resistance properties. In shear - slitting machines, the design of the straight blades and their actuation system is crucial. The blades must be able to apply sufficient force to cut through the material cleanly. For laser - slitting machines, the laser - generating and - focusing systems need to be designed to provide a stable and high - quality laser beam for accurate cutting.
2. Control Systems and Automation
Automated Operation: Modern slitting line machines are equipped with advanced control systems that enable automated operation. The control systems manage various aspects of the machine, such as the speed of the coil unwinding, the feeding of the material through the machine, and the cutting process. They can be programmed to adjust the slit width, cutting speed, and other parameters based on the input from the operator or pre - set production requirements.
Monitoring and Feedback: The control systems also incorporate monitoring and feedback mechanisms. Sensors are used to measure parameters such as the position of the material, the tension in the coil, and the performance of the cutting tools. Based on this information, the control system can make real - time adjustments to ensure optimal operation. For example, if the tension in the coil becomes too high or too low, the control system can adjust the tensioning rollers to correct the situation.
3. Safety Features and Compliance
Safety in Operation: Slitting line machines involve moving parts, sharp cutting tools, and in some cases, high - power lasers. Therefore, safety is a top priority in their design. Manufacturers incorporate various safety features, such as emergency stop buttons, safety guards around the cutting area, and interlocks that prevent the machine from operating when safety conditions are not met. These safety features protect the operators from potential hazards during the operation of the machine.
Industry Standards and Regulations: Slitting line machine manufacturers must comply with relevant industry standards and regulations. These include standards related to machine safety, electrical systems, and environmental protection. Compliance ensures that the machines are safe to use and do not cause any negative impact on the environment.
V. The Manufacturing Process of Slitting Line Machines
1. Component Fabrication
Mechanical Components: The manufacturing process begins with the fabrication of mechanical components. This includes the production of the machine frame, rollers, shafts, and other parts. The frame is usually fabricated by welding heavy - duty steel sections and then machining them to the required dimensions. The rollers are carefully manufactured with smooth surfaces and precise diameters. Shafts are machined to high tolerances to ensure proper fit and function. In the case of laser - slitting machines, the fabrication of the laser - related components requires specialized manufacturing techniques and high - quality materials.
Electrical and Control Components: The electrical and control components of the slitting line machine are also fabricated or sourced. This includes motors, sensors, control panels, and wiring harnesses. The motors are selected based on the power requirements of the machine, and the sensors are chosen for their accuracy and reliability. The control panels are designed with user - friendly interfaces to allow operators to easily control the machine.
2. Assembly and Integration
Mechanical Assembly: Once the components are fabricated, they are assembled in the factory. The assembly process involves fitting the rollers, shafts, and cutting mechanisms into the machine frame. The alignment of these components is crucial for the proper functioning of the slitting line machine. In roll - slitting machines, the circular knives are mounted on the shafts and adjusted for the correct slit width. In shear - slitting machines, the shearing blades are installed and calibrated. For laser - slitting machines, the laser system is integrated with the rest of the machine, and the optical path is adjusted to ensure accurate cutting.
Electrical and Control Integration: The electrical and control components are then integrated with the mechanical assembly. The motors are connected to the power supply and the control system. The sensors are installed in the appropriate positions to monitor the machine's operation. The control panels are wired to the control system, and the software for the control system is programmed and tested.
3. Testing and Quality Assurance
Mechanical Testing: After assembly, the slitting line machine undergoes mechanical testing. This includes checking the smooth running of the rollers, the proper rotation of the shafts, and the correct functioning of the cutting mechanisms. The machine is also tested for its ability to handle different types of materials and coil widths. The tension control system is evaluated to ensure that it can maintain the correct tension during the slitting process.
Electrical and Control Testing: The electrical and control systems are thoroughly tested. The motors are tested for their speed and torque output. The sensors are calibrated and checked for accuracy. The control system is tested for its ability to control the machine's operation according to the programmed parameters. The safety features are also tested to ensure that they work properly.
Quality Assurance and Certification: Quality assurance procedures are followed throughout the manufacturing process. The machine is inspected for any defects or non - conformities. Once the machine passes all the tests, it may be certified according to relevant industry standards. This certification provides assurance to the customers that the machine meets the required quality and safety standards.
VI. Challenges and Solutions in the Manufacturing of Slitting Line Machines
1. Meeting Customer Requirements
Customization: Customers often have specific requirements for slitting line machines, such as the ability to handle particular materials, specific slit width ranges, and different production speeds. Manufacturers need to be able to customize their machines to meet these diverse needs. This may involve modifying the machine design, using different cutting tools, or adjusting the control system. To address this, manufacturers often have modular designs that allow for easy customization.
Understanding Customer Needs: It is essential for manufacturers to have a good understanding of their customers' industries and applications. This helps them to design machines that are not only technically proficient but also meet the practical requirements of the end - use. Manufacturers may work closely with customers during the design phase, conduct site visits, or analyze customer feedback to gain this understanding.
2. Technological Advancements and Innovation
Keeping Up with Technology: The field of slitting line machines is constantly evolving with new cutting technologies, automation solutions, and materials. Manufacturers need to stay updated with these advancements to remain competitive. This may involve investing in research and development, attending industry conferences, and collaborating with technology partners. For example, the integration of artificial intelligence into control systems or the use of new materials for cutting tools are areas of ongoing research.
Innovating for Efficiency and Quality: Manufacturers are constantly looking for ways to improve the efficiency and quality of their machines. This may include developing more precise cutting mechanisms, improving the speed and accuracy of the control systems, or enhancing the durability of the machine components. Innovation in these areas can lead to better performance, reduced maintenance requirements, and increased customer satisfaction.
3. Cost Management and Competitiveness
Cost - effective Production: Manufacturing slitting line machines can be costly due to the use of high - quality materials, advanced manufacturing techniques, and sophisticated control systems. Manufacturers need to manage costs effectively to remain competitive. This may involve optimizing the supply chain for raw materials, improving production efficiency, and reducing waste. For example, using lean manufacturing principles can help to streamline the production process and reduce costs.
Pricing and Value Proposition: Determining the right pricing strategy is crucial. Manufacturers need to balance the cost of production with the value that the machine provides to the customer. This requires a clear understanding of the market and the competitive landscape. Offering additional services such as installation, training, and after - sales support can also enhance the value proposition of the machine.
4. After - sales Service and Support
Service Network: Providing excellent after - sales service is essential for customer satisfaction. Manufacturers need to have a well - developed service network to quickly respond to customer inquiries and issues. This may involve having local service centers, trained technicians, and a stock of spare parts. A reliable service network ensures that the machine can be quickly repaired in case of breakdowns, minimizing downtime for the customer.
Training and Support: Offering training to the customer's operators is also important. This helps the operators to understand the machine's operation, maintenance requirements, and safety procedures. Manufacturers may provide on - site training, online tutorials, or user manuals. Additionally, providing ongoing technical support and updates for the control system can help to keep the machine running smoothly over its lifespan.
VII. Conclusion
Slitting line machine manufacturers play a vital role in the industrial manufacturing sector. Their ability to design, produce, and support high - quality slitting line machines is crucial for the efficient processing of materials in various industries. Despite the challenges they face, through continuous innovation, cost management, and excellent after - sales service, these manufacturers can meet the evolving needs of their customers and contribute to the growth and development of the manufacturing industry.