Hotline
+86-136 8495 9862
Email:cennia@szmizhi.com
Add::104,Building 27,Third Industrial Zone, Longxi Community,Longgang District,Shenzhen,China.
Coil Forming & Handling Equipment
Surface Treatment Equipment
Solutions
Application
About Us
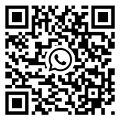
Welcome to MIZHI
For consultation/feedback, please call the service hotline: +86-136 8495 9862 Email:cennia@szmizhi.com
In the world of metal processing, the slitting line machine has emerged as a game-changer, offering efficient and precise cutting solutions for a wide range of materials. This advanced machinery has transformed the way metals are processed, providing manufacturers with increased productivity, improved quality, and greater flexibility. In this in-depth exploration, we will take a closer look at the slitting line machine, its features, working principles, applications, and future prospects.
I. Introduction
The slitting line machine is a specialized piece of equipment designed for cutting large coils of metal into narrower strips. It is widely used in the steel, aluminum, and other metal industries for a variety of applications, including the production of metal sheets, coils, and strips for construction, automotive, appliance, and other industries.
II. Features of Slitting Line Machine
1. High Precision
One of the key features of the slitting line machine is its high precision cutting capabilities. These machines are equipped with advanced cutting tools and control systems that ensure accurate and consistent cuts, resulting in high-quality finished products. The precision of the slitting process is crucial for applications where tight tolerances are required, such as in the production of automotive parts or electrical components.
2. High Production Capacity
Slitting line machines are designed for high-volume production, capable of processing large coils of metal quickly and efficiently. With their automated operation and high-speed cutting capabilities, these machines can significantly increase production output, reducing production time and costs.
3. Versatility
These machines are highly versatile, able to handle a wide range of metal materials and thicknesses. They can be configured to cut different widths and lengths of strips, providing manufacturers with the flexibility to meet the diverse needs of their customers. Additionally, slitting line machines can be integrated with other metal processing equipment, such as leveling machines and cut-to-length lines, to create a complete production line.
4. Advanced Control Systems
Slitting line machines are equipped with advanced control systems that allow for precise control of the cutting process. These systems can be programmed to adjust cutting parameters such as speed, blade position, and tension, ensuring optimal cutting performance for different materials and thicknesses. Some slitting line machines also feature automated inspection and quality control systems, ensuring that only high-quality strips are produced.
5. Safety Features
Safety is a top priority in any industrial setting, and slitting line machines are equipped with a variety of safety features to protect operators. These may include safety guards, emergency stop buttons, and interlocks to prevent accidental operation. Additionally, some machines are designed with ergonomic features to reduce operator fatigue and improve working conditions.
III. Working Principles of Slitting Line Machine
The slitting line machine operates on a relatively simple principle. It consists of a series of rollers and cutting tools that work together to cut a large coil of metal into narrower strips. The process typically involves the following steps:
1. Uncoiling
The large coil of metal is loaded onto the uncoiler, which unwinds the coil and feeds the metal strip into the slitting line. The uncoiler is usually equipped with a tension control system to ensure smooth feeding of the strip.
2. Leveling
Before slitting, the metal strip may pass through a leveling machine to remove any wrinkles or distortions. The leveling process ensures that the strip is flat and smooth, improving the quality of the cut.
3. Slitting
The metal strip then enters the slitting section, where it is cut into narrower strips by a set of circular knives or razor blades. The cutting tools are mounted on a shaft and are driven by a motor. The spacing between the cutting tools can be adjusted to produce strips of different widths.
4. Rewinding
After slitting, the narrower strips are wound onto separate reels using the rewinder. The rewinder is also equipped with a tension control system to ensure that the strips are wound tightly and evenly.
5. Inspection and Packaging
Finally, the slit strips are inspected for quality and defects. If necessary, they may be further processed or packaged for shipment.
IV. Applications of Slitting Line Machine
1. Steel Industry
In the steel industry, slitting line machines are widely used for cutting large coils of steel into narrower strips for various applications. These include the production of steel sheets for construction, automotive, and appliance industries, as well as the production of steel pipes and tubes.
2. Aluminum Industry
The aluminum industry also relies on slitting line machines for cutting aluminum coils into strips for applications such as packaging, construction, and transportation. Aluminum strips are used in the production of cans, foil, and other products.
3. Other Metal Industries
Slitting line machines are also used in the processing of other metals such as copper, brass, and stainless steel. These machines can be configured to handle different materials and thicknesses, providing manufacturers with a versatile cutting solution.
4. Metal Service Centers
Metal service centers use slitting line machines to process and distribute metal coils to customers. They can cut coils to specific widths and lengths as per customer requirements, providing a value-added service.
V. Factors to Consider When Choosing a Slitting Line Machine
1. Material and Thickness
The type of metal and its thickness will determine the capabilities of the slitting line machine. Different materials may require different cutting tools and settings, so it is important to choose a machine that is suitable for the specific materials being processed.
2. Production Capacity
Consider the required production volume and choose a machine that can meet your production needs. Look for machines with high-speed cutting capabilities and automated features to increase productivity.
3. Precision Requirements
If tight tolerances are required for your application, choose a machine with high-precision cutting tools and control systems. This will ensure accurate and consistent cuts, resulting in high-quality finished products.
4. Flexibility
If you need to process a variety of materials and widths, choose a machine that is highly versatile and can be easily configured to meet different requirements. Look for machines with adjustable cutting tools and programmable control systems.
5. Cost
The cost of a slitting line machine can vary significantly depending on its features and capabilities. Consider your budget and choose a machine that offers the best value for money. Don't forget to factor in the cost of maintenance and operation over the life of the machine.
VI. Maintenance and Troubleshooting of Slitting Line Machine
1. Regular Maintenance
To ensure the smooth operation and longevity of the slitting line machine, regular maintenance is essential. This may include cleaning and lubricating the machine, inspecting and replacing worn parts, and calibrating the cutting tools and control systems. Follow the manufacturer's recommended maintenance schedule and procedures to keep your machine in top condition.
2. Troubleshooting
Despite regular maintenance, problems may still occur with the slitting line machine. Some common issues include blade wear, misalignment, and tension problems. When troubleshooting, start by identifying the problem and then follow a systematic approach to diagnose and resolve the issue. Consult the machine's manual and seek professional help if necessary.
VII. Future Prospects of Slitting Line Machine
The slitting line machine is expected to continue to play a crucial role in the metal processing industry in the coming years. With the growing demand for high-quality metal products and the need for increased productivity and efficiency, manufacturers will continue to invest in advanced slitting line machines. Some of the future trends in slitting line machines include:
1. Automation and Robotics
The integration of automation and robotics in slitting line machines will further increase productivity and reduce labor costs. Automated systems can perform tasks such as loading and unloading coils, adjusting cutting parameters, and inspecting finished products.
2. Digitalization and Connectivity
The use of digital technologies such as sensors, data analytics, and the Internet of Things (IoT) will enable real-time monitoring and optimization of the slitting process. This will improve quality control, reduce waste, and increase efficiency.
3. Energy Efficiency
As environmental concerns grow, there will be a greater focus on energy-efficient slitting line machines. Manufacturers will develop machines that consume less power and use sustainable materials and processes.
4. Customization and Flexibility
To meet the diverse needs of customers, slitting line machines will become more customizable and flexible. Manufacturers will offer machines that can be easily configured to process different materials, widths, and lengths, providing a tailored solution for each application.
The slitting line machine has revolutionized the metal processing industry, providing efficient and precise cutting solutions for a wide range of materials. With its high precision, high production capacity, versatility, and advanced control systems, this machinery has become an essential tool for manufacturers in the steel, aluminum, and other metal industries. When choosing a slitting line machine, consider factors such as material and thickness, production capacity, precision requirements, flexibility, and cost. Regular maintenance and troubleshooting are also important to ensure the smooth operation and longevity of the machine. Looking to the future, the slitting line machine is expected to become even more advanced, with automation, digitalization, energy efficiency, and customization being the key trends. As the demand for high-quality metal products continues to grow, the slitting line machine will play a crucial role in meeting these needs.