Hotline
+86-136 8495 9862
Email:cennia@szmizhi.com
Add::104,Building 27,Third Industrial Zone, Longxi Community,Longgang District,Shenzhen,China.
Coil Forming & Handling Equipment
Surface Treatment Equipment
Solutions
Application
About Us
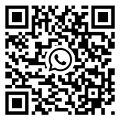
Welcome to MIZHI
For consultation/feedback, please call the service hotline: +86-136 8495 9862 Email:cennia@szmizhi.com
I. Introduction
Slitting lines play a crucial role in the metal processing and manufacturing industries. These systems are designed to cut large coils of metal sheets or strips into narrower widths according to specific requirements. The manufacturers of slitting lines are key players in providing the necessary equipment that enables efficient and precise slitting operations. This article will explore various aspects of slitting line manufacturers, including their capabilities, the technologies they employ, the types of slitting lines they produce, and their impact on different industries.
II. Capabilities of Slitting Line Manufacturers
1.Engineering and Design Expertise
Slitting line manufacturers possess extensive engineering and design knowledge. They have teams of experienced engineers who are well - versed in mechanical, electrical, and control systems engineering. These professionals are capable of designing slitting lines that can handle different types of metals, such as steel, aluminum, copper, and their alloys. The design process takes into account factors like the thickness of the coil, the desired width of the slit strips, the speed of the slitting process, and the overall production requirements of the customer. For example, for high - volume production of narrow - width metal strips used in the electronics industry, the design may focus on a high - speed slitting line with precise width control mechanisms.
2.Customization
One of the significant capabilities of slitting line manufacturers is the ability to customize their products. Every customer may have unique requirements based on their end - use applications. Manufacturers can tailor slitting lines to meet these specific needs. This may include customizing the length of the line, the number of slitting stations, the type of cutting tools used, and the integration of additional features such as automatic coil handling systems, edge trimming devices, or tension control mechanisms. For instance, a customer in the automotive industry may require a slitting line that can handle thick steel coils and has a specific width range for producing parts like seat frames. The manufacturer can design a system with heavy - duty components and adjustable slitting widths to fulfill this requirement.
3.Quality Control and Testing
Reputable slitting line manufacturers have robust quality control and testing procedures in place. During the manufacturing process, they conduct various inspections to ensure the quality of the components and the overall system. This includes checking the precision of the cutting tools, the accuracy of the mechanical assemblies, and the proper functioning of the electrical and control systems. Before delivery, the slitting line undergoes comprehensive testing. The testing may involve running the line with sample coils to verify the slitting accuracy, speed stability, and the reliability of the safety features. Manufacturers also use advanced measurement tools and techniques, such as laser - based measurement systems for width control and non - destructive testing methods for detecting any potential flaws in the structure of the line.
4.After - sales Support
Another important capability of slitting line manufacturers is providing after - sales support. This includes installation assistance, training of the customer's operating and maintenance staff, and ongoing technical support. When the slitting line is installed at the customer's facility, the manufacturer's technicians ensure that it is properly set up and calibrated. They train the operators on how to use the control panel, adjust the slitting parameters, and perform routine maintenance tasks. In case of any issues during the operation of the slitting line, the manufacturer's support team is available to provide troubleshooting advice, supply replacement parts, and conduct repairs if necessary. This after - sales support helps to ensure the long - term reliability and productivity of the slitting line.
III. Technologies Employed by Slitting Line Manufacturers
1.Cutting Technologies
There are several cutting technologies used in slitting lines. One of the most common is rotary shearing. In this method, a set of circular blades rotate at high speed to cut the metal coil. The blades are carefully designed and manufactured to ensure clean and precise cuts. The angle of the blades, the cutting speed, and the pressure applied are all critical parameters that manufacturers optimize based on the type of metal and the desired slit width. Another cutting technology is razor slitting, which is often used for thinner and more delicate metal sheets. Razor blades are used to make the cuts, and this method requires very high - precision alignment of the blades and the material. Laser cutting technology is also emerging in slitting lines. It offers extremely high precision and can be used for cutting complex shapes or materials with special properties. However, laser cutting systems are more expensive and require more sophisticated maintenance.
2.Automation and Control Technologies
Slitting line manufacturers incorporate advanced automation and control technologies to improve the efficiency and accuracy of the slitting process. Programmable logic controllers (PLCs) are widely used to control the various components of the slitting line, such as the coil feeding mechanism, the cutting stations, and the strip winding system. PLCs allow for precise control of the speed, position, and operation sequence of these components. Sensors are also an integral part of the control system. They are used to monitor parameters such as the width of the coil, the tension in the metal strip, and the position of the cutting tools. Based on the feedback from these sensors, the control system can make real - time adjustments to ensure optimal slitting performance. Additionally, manufacturers are increasingly using human - machine interface (HMI) systems that provide operators with an intuitive and easy - to - use interface for monitoring and controlling the slitting line.
3.Coil Handling and Feeding Technologies
Efficient coil handling and feeding are essential in slitting lines. Manufacturers use technologies such as motor - driven uncoilers to unwind the large metal coils. These uncoilers are designed to handle coils of different weights and diameters. They have features like adjustable tension control to ensure a smooth and continuous supply of the metal to the slitting stations. Some advanced uncoilers also have automatic coil centering and alignment functions to improve the accuracy of the slitting process. In addition, there are feeding systems that transport the metal strip from the uncoiler to the cutting stations. These feeding systems may include conveyor belts, rollers, or magnetic feeders, depending on the type of metal and the design of the slitting line.
4.Strip Winding and Packaging Technologies
After the metal coil is slit, the resulting strips need to be wound and packaged. Slitting line manufacturers use various winding technologies to ensure that the strips are wound neatly and tightly. Tension - controlled winding systems are commonly used to maintain a consistent tension in the strips during the winding process. This helps to prevent issues such as wrinkling or loose winding. For packaging, the strips may be wrapped in plastic film or placed in cardboard boxes. Some manufacturers also offer automatic packaging systems that can label the packages and prepare them for shipment. These packaging technologies ensure that the slit strips are protected during storage and transportation.
IV. Types of Slitting Lines Produced by Manufacturers
1.High - speed Slitting Lines
High - speed slitting lines are designed for applications where large volumes of metal strips need to be produced in a short time. These lines are capable of operating at very high speeds, often exceeding several hundred meters per minute. They are equipped with high - performance cutting tools and advanced control systems to maintain accuracy at high speeds. High - speed slitting lines are commonly used in industries such as the packaging industry, where narrow metal strips are used for making cans or other packaging materials. The components of these lines are carefully engineered to withstand the high - speed operation and the associated mechanical stresses. For example, the bearings and drive systems are selected for their ability to handle high - speed rotation without excessive wear.
2.Precision Slitting Lines
Precision slitting lines are focused on achieving extremely accurate slit widths. These lines are used in industries where tight tolerances are required, such as the electronics and medical device industries. The cutting tools in precision slitting lines are of the highest quality and are often customized for specific applications. The control systems have very fine - tuned width control mechanisms, which may use laser - based measurement and feedback to ensure that the slit widths are within a very narrow tolerance range. Precision slitting lines may also have additional features such as temperature control in the cutting area to minimize the effect of thermal expansion on the width accuracy. The overall design of these lines aims to minimize any factors that could cause variations in the slit width.
3.Heavy - duty Slitting Lines
Heavy - duty slitting lines are built to handle thick and heavy metal coils. They are used in industries such as the construction and automotive industries, where thick steel or aluminum plates need to be slit. These lines have robust mechanical structures with heavy - duty frames, large - diameter rollers, and powerful cutting tools. The uncoilers in heavy - duty slitting lines can handle coils weighing several tons. The cutting stations are designed to apply sufficient force to cut through the thick metal without excessive wear on the tools. Additionally, these lines may have enhanced safety features to protect the operators during the handling of heavy coils and the operation of the slitting process.
4.Multi - purpose Slitting Lines
Multi - purpose slitting lines are designed to be versatile and can handle a wide range of metal types, thicknesses, and slit width requirements. These lines are often used in job shops or small - to - medium - sized manufacturing facilities where there is a diverse range of slitting jobs. They can be adjusted and configured to meet different customer orders. The design of multi - purpose slitting lines includes modular components that can be easily replaced or reconfigured. For example, the cutting stations may have interchangeable cutting tools to handle different metal thicknesses, and the coil handling system can be adjusted to accommodate various coil sizes. This flexibility allows manufacturers to use the same slitting line for different projects without the need for extensive retooling.
V. Impact of Slitting Line Manufacturers on Different Industries
1.Metal Processing Industry
Slitting line manufacturers are at the core of the metal processing industry. Their equipment enables metal processors to transform large coils of metal into smaller, more manageable strips that are ready for further processing. This includes industries such as steel mills, aluminum smelters, and copper fabricators. The slitting lines produced by manufacturers improve the efficiency of the production process by reducing the need for manual cutting and increasing the precision of the cuts. This results in higher - quality products with more consistent dimensions, which are essential for downstream applications. For example, in the production of steel strips for construction purposes, accurate slitting ensures that the strips can be easily welded or formed into structural components.
2.Automotive Industry
In the automotive industry, slitting lines play a crucial role in the production of various parts. From the frames of seats to the body panels, many automotive components are made from slit metal strips. Slitting line manufacturers provide the equipment that allows automotive manufacturers to obtain the right width and thickness of metal strips for their specific applications. The precision slitting lines ensure that the metal parts have the required tolerances, which is vital for the proper assembly and performance of the vehicles. Moreover, the ability to handle different types of metals, such as high - strength steel and aluminum alloys, enables automotive manufacturers to choose the most suitable materials for each part based on factors like strength, weight, and cost.
3.Electronics Industry
The electronics industry demands high - precision slitting of thin metal sheets for components such as printed circuit boards (PCBs), connectors, and shielding materials. Slitting line manufacturers produce precision slitting lines that can handle these delicate materials with extreme accuracy. The narrow and precisely cut metal strips are used in the production of conductive traces on PCBs and for creating the enclosures that protect electronic components from electromagnetic interference. The high - speed slitting lines also contribute to the mass production of these components, enabling the electronics industry to meet the growing demand for consumer electronics products. The quality of the slitting directly affects the performance and reliability of the electronic devices.
4.Packaging Industry
In the packaging industry, slitting lines are used to produce the metal sheets for cans, boxes, and other packaging materials. High - speed slitting lines are particularly important in this industry as they can quickly produce the large quantities of narrow metal strips required for can production. The slitting lines ensure that the metal strips have the correct width and smooth edges, which are essential for the manufacturing process of cans. This includes the formation of the can body, the application of the lid, and the overall integrity of the packaging. The ability of slitting line manufacturers to provide reliable and efficient equipment helps the packaging industry to maintain high - quality standards and meet the production demands.
5.Construction Industry
The construction industry uses slitting lines to obtain metal strips for applications such as roofing, siding, and structural components. Heavy - duty slitting lines are used to handle the thick metal sheets typically used in construction. The slitted metal strips are used in the production of metal roofs, where they need to be of the right width and have good strength to withstand environmental conditions. In siding applications, the precision of the slitting affects the appearance and durability of the siding. The slitting lines also provide the construction industry with the flexibility to use different metals, such as steel or aluminum, depending on the project requirements. This allows for the creation of more durable and aesthetically pleasing building exteriors.
VI. Challenges Faced by Slitting Line Manufacturers
1.Meeting Stringent Quality Standards
Slitting line manufacturers must meet very high - quality standards set by various industries. In the electronics industry, for example, the slit widths need to be within extremely tight tolerances to ensure the proper functioning of electronic components. Meeting these standards requires continuous investment in advanced manufacturing technologies, precise measurement tools, and highly skilled labor. Manufacturers also need to ensure the long - term stability of their equipment, as any drift in the slitting accuracy over time can lead to rejects in the customer's production process. Additionally, they have to comply with international quality certifications and standards to be competitive in the global market.
2.Keeping Up with Technological Advancements
The field of slitting technology is constantly evolving. New cutting technologies, such as laser cutting, are emerging, and automation and control systems are becoming more sophisticated. Slitting line manufacturers need to stay updated with these technological advancements to remain competitive. This involves continuous research and development, attending industry conferences, and collaborating with research institutions. They also need to be able to integrate these new technologies into their existing product lines without sacrificing the reliability and ease - of - use of their equipment. For example, implementing a new laser - based cutting system requires not only the installation of the laser equipment but also the development of appropriate control software and training for the operators.
3.Cost Management
Cost management is a significant challenge for slitting line manufacturers. The materials used in constructing slitting lines, such as high - quality cutting tools, precision bearings, and advanced control systems, can be expensive. Additionally, the cost of labor, especially highly skilled engineers and technicians, is high. Manufacturers need to balance the quality of their products with the cost to remain competitive. This may involve finding more cost - effective suppliers for raw materials, optimizing their production processes to reduce waste and increase efficiency, and carefully managing their labor costs. At the same time, they cannot compromise on the quality of the slitting lines as this would lead to customer dissatisfaction and loss of business.
4.Environmental Regulations
Slitting line manufacturers are also subject to environmental regulations. The manufacturing process may generate waste materials, such as metal shavings and used lubricants. Manufacturers need to have proper waste management systems in place to dispose of these materials in an environmentally friendly manner. They may also need to reduce the energy consumption of their manufacturing processes to comply with environmental standards. For example, using more energy - efficient motors in the coil handling and cutting systems can help reduce the overall environmental impact. Additionally, the use of eco - friendly cutting fluids and lubricants can further contribute to environmental compliance.
VII. Future Trends in Slitting Line Manufacturing
1.Increased Automation and Industry 4.0 Integration
The future of slitting line manufacturing will see a greater degree of automation and integration with Industry 4.0 concepts. This includes the use of artificial intelligence and machine learning in the control systems. For example, AI - based algorithms can be used to predict and prevent maintenance issues by analyzing data from sensors in the slitting line. The slitting lines will be more connected, with the ability to communicate with other production systems in the factory. This will enable better production planning and coordination. Operators will be able to monitor and control the slitting line remotely using mobile devices or computer interfaces, improving overall productivity and reducing the need for on - site presence.
2.Advanced Materials and Coatings for Cutting Tools
There will be a continued focus on developing advanced materials and coatings for cutting tools. New materials with higher hardness, wear resistance, and heat resistance will be used to improve the lifespan of the cutting tools. Coatings such as diamond - like carbon coatings or ceramic coatings can enhance the cutting performance and reduce friction during the slitting process. This will not only improve the quality of the slit strips but also reduce the frequency of tool replacement, saving costs for the customers. The development of these advanced materials and coatings will be driven by both research in materials science and the specific requirements of the slitting industry.
3.Miniaturization and Micro - slitting Technologies
With the growth of the microelectronics and medical device industries, there will be an increasing demand for micro - slitting technologies. Manufacturers will need to develop slitting lines capable of handling extremely thin materials and achieving sub - millimeter slit widths. This will require new design concepts and precision manufacturing techniques. The control systems for these micro - slitting lines will need to have even higher accuracy and stability. The development of micro - slitting technologies will open up new opportunities for the production of smaller and more advanced electronic and medical components.
4.Sustainable Manufacturing Practices
Sustainable manufacturing will become a more prominent trend in slitting line manufacturing. This includes using renewable energy sources in the manufacturing process, reducing waste generation, and using recyclable materials wherever possible. Manufacturers will also focus on designing slitting lines that are more energy - efficient during operation. For example, optimizing the power consumption of the motors and reducing the amount of lubricants and cutting fluids used. The adoption of sustainable manufacturing practices will not only help manufacturers meet environmental regulations but also enhance their brand image and attract customers who are increasingly concerned about the environment.
Slitting line manufacturers are vital to numerous industries as they provide the essential equipment for metal slitting operations. Their capabilities in engineering, customization, quality control, and after - sales support ensure that customers receive reliable and efficient slitting lines. The technologies they employ, from cutting to automation and coil handling, are constantly evolving to meet the demands of different industries. The types of slitting lines they produce, whether high - speed, precision, heavy - duty, or multi - purpose, serve specific applications in various sectors. Despite facing challenges such as quality standards, technological advancements, cost management, and environmental regulations, slitting line manufacturers are well - positioned to adapt to future trends, including increased automation, advanced cutting tool materials, micro - slitting, and sustainable manufacturing. As industries continue to grow and evolve, the role of slitting line manufacturers will remain crucial in enabling the efficient processing of metal materials.