Hotline
+86-136 8495 9862
Email:cennia@szmizhi.com
Add::104,Building 27,Third Industrial Zone, Longxi Community,Longgang District,Shenzhen,China.
Coil Forming & Handling Equipment
Surface Treatment Equipment
Solutions
Application
About Us
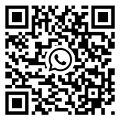
Welcome to MIZHI
For consultation/feedback, please call the service hotline: +86-136 8495 9862 Email:cennia@szmizhi.com
I. Introduction
Slitting line manufacturers play a crucial role in the metal processing and manufacturing industries. These manufacturers design, produce, and supply slitting lines that are used to cut large coils of metal into narrower strips of specific widths. The quality and performance of slitting lines directly impact the efficiency and precision of metal production processes, making these manufacturers an integral part of the supply chain for various end - use industries such as automotive, construction, and electronics.
II. The Significance of Slitting Lines in Metal Processing
1.
Meeting Diverse Industry Requirements
Slitting lines are essential for fulfilling the specific width requirements of different metal products. In the automotive industry, for example, the slitting of steel coils into precise widths is necessary for manufacturing parts like seat frames, body panels, and engine components. The construction sector relies on slitting lines to produce metal strips for roofing materials, structural supports, and siding. In electronics, narrow metal strips are used for components such as connectors and printed circuit boards. The ability of slitting lines to accurately cut metal coils into the desired widths ensures that these industries can obtain the materials they need for their manufacturing processes.
2.
Enhancing Material Utilization
By cutting large metal coils into smaller strips, slitting lines improve material utilization. Manufacturers can make the most of the raw material by producing multiple strips of different widths from a single coil. This not only reduces waste but also optimizes the cost - effectiveness of the production process. For instance, a slitting line can be programmed to slit a coil of aluminum into various widths for different applications within the same factory, maximizing the value of the purchased coil.
3.
Quality Control in Metal Strip Production
The precision of slitting lines is vital for maintaining high - quality metal strips. The cutting process must ensure straight edges, consistent widths, and minimal burrs or deformations. High - quality slitting lines from reputable manufacturers are equipped with advanced control systems that monitor and adjust the cutting process in real - time. This results in metal strips that meet strict quality standards, reducing the need for rework or rejection of materials during subsequent manufacturing processes.
III. Types of Slitting Lines Manufactured
1.
Roll - slitting Lines
Roll - slitting lines are the most common type. They use circular knives mounted on shafts to cut the metal coil. The coil is unwound, and the metal passes through a series of rollers that guide it to the slitting section. The circular knives can be adjusted to achieve different slit widths. These lines are suitable for a wide range of metals, including steel, aluminum, and copper. They are often used for high - volume production due to their relatively fast slitting speed. Roll - slitting lines can be further classified based on the number of slitting stations and the complexity of the setup. For example, some roll - slitting lines have multiple slitting stations to simultaneously produce several different widths of strips from a single coil.
2.
Shear - slitting Lines
Shear - slitting lines utilize a shearing action to cut the metal coil. Instead of circular knives, they have a set of straight blades that move vertically or horizontally to cut the metal. Shear - slitting is often preferred for thicker metals or when a more precise cut is required. The shearing process can provide cleaner cuts with less deformation compared to some roll - slitting methods. These lines are commonly used in industries where the quality of the cut edge is of utmost importance, such as in the production of high - precision mechanical parts.
3.
Laser - slitting Lines
Laser - slitting lines are emerging as a high - tech option. They use high - power lasers to cut the metal coil. The laser beam is focused onto the metal surface, melting or vaporizing the material to create a slit. Laser - slitting offers extremely high precision and can handle complex cutting patterns. It is suitable for cutting thin and delicate metals as well as materials with special requirements. For example, in the electronics industry, laser - slitting lines can cut very thin metal foils for micro - components with minimal heat - affected zones. However, laser - slitting lines are generally more expensive and require more specialized maintenance compared to other types.
IV. Key Considerations in Slitting Line Manufacturing
1.
Machine Design and Engineering
The design of a slitting line starts with a thorough understanding of the metal - cutting process. Manufacturers need to consider the mechanical structure of the machine, including the frame, rollers, and cutting mechanisms. The frame must be sturdy enough to withstand the forces during the slitting operation. The rollers should be designed to provide smooth and stable material feeding, with proper alignment to prevent the metal coil from deviating during the process. The cutting mechanisms, whether circular knives, shearing blades, or lasers, must be precisely engineered for accurate and efficient cutting. For example, in roll - slitting lines, the design of the knife - holding shafts and the ability to adjust the knife positions with high precision are critical factors.
2.
Control Systems and Automation
Modern slitting lines are equipped with advanced control systems. These systems manage the speed of the coil unwinding, the feeding of the metal through the machine, and the cutting process. Automation features allow for continuous operation with minimal human intervention. The control systems can be programmed to adjust the slit width, cutting speed, and other parameters based on the input from the operator or pre - set production requirements. For instance, a control system can automatically slow down the slitting speed if it detects an increase in cutting force, indicating a potential problem with the cutting tools or the material.
3.
Cutting Tool Selection and Maintenance
The choice of cutting tools depends on the type of slitting line and the metal being processed. In roll - slitting lines, high - quality circular knives made of tool steel or carbide are commonly used. The knives need to have the right hardness, sharpness, and wear - resistance properties. In shear - slitting lines, the straight blades must be carefully selected and maintained. For laser - slitting lines, the laser source and associated optical components need to be of high quality. Regular maintenance of the cutting tools is essential to ensure consistent cutting performance. Manufacturers often provide guidelines for tool replacement and maintenance schedules to their customers.
4.
Safety Features and Compliance
Slitting lines involve high - speed rotating knives, powerful lasers, or heavy - duty shearing mechanisms, making safety a top priority. Manufacturers incorporate various safety features into their machines. These include emergency stop buttons, safety guards around the cutting area, and interlocks that prevent the machine from operating when safety conditions are not met. Additionally, slitting line manufacturers must comply with relevant industry standards and regulations regarding machine safety, electrical systems, and environmental protection.
V. The Manufacturing Process of Slitting Lines
1.
Component Fabrication
The manufacturing process begins with the fabrication of individual components. This includes the production of the machine frame, rollers, shafts, and other mechanical parts. The frame is usually made of heavy - duty steel, welded and machined to ensure its strength and dimensional accuracy. The rollers are carefully manufactured with smooth surfaces and precise diameters to ensure proper material handling. Shafts for holding the cutting tools are machined to high tolerances to enable accurate positioning of the tools. In the case of laser - slitting lines, the fabrication of the laser - generating and - focusing components requires specialized manufacturing techniques to ensure their performance.
2.
Assembly and Integration
Once the components are fabricated, they are assembled in the factory. The assembly process involves carefully fitting the rollers, shafts, and cutting mechanisms into the machine frame. The alignment of these components is crucial for the proper functioning of the slitting line. In roll - slitting lines, the circular knives are mounted on the shafts and adjusted for the desired slit widths. In shear - slitting lines, the shearing blades are installed and calibrated. For laser - slitting lines, the laser system is integrated with the rest of the machine, and the optical path is carefully adjusted to ensure the laser beam is focused correctly on the metal coil.
3.
Testing and Quality Assurance
After assembly, each slitting line undergoes extensive testing. The testing process includes checking the mechanical operation of the machine, such as the smooth running of the rollers and the correct functioning of the cutting mechanisms. The control systems are also tested to ensure that they can accurately control the slitting process. In the case of laser - slitting lines, the laser power, beam quality, and cutting precision are evaluated. Quality assurance procedures involve measuring the slit widths, checking for burrs or deformations on the cut metal strips, and verifying that the machine meets all safety and performance standards. Only after successful testing and quality assurance is the slitting line ready for shipment to the customer.
VI. Challenges and Solutions in Slitting Line Manufacturing
1.
Meeting Diverse Customer Requirements
Customers have a wide range of requirements in terms of slit widths, metal types, production speeds, and automation levels. Slitting line manufacturers need to be able to customize their machines to meet these diverse needs. To address this, manufacturers often have modular designs that allow for easy configuration of the slitting line. They also work closely with customers during the design phase to understand their specific requirements and develop tailored solutions.
2.
Technology Upgrades and Innovation
The metal processing industry is constantly evolving, with new materials and higher - quality requirements emerging. Slitting line manufacturers must keep up with these changes by investing in research and development. This includes adopting new cutting technologies, improving control systems, and enhancing the efficiency of their machines. For example, manufacturers are exploring ways to integrate artificial intelligence into control systems to optimize the slitting process further. To fund these upgrades, they may form partnerships with research institutions or seek government grants for innovation - related projects.
3.
Cost Management and Competitiveness
Manufacturing high - quality slitting lines can be expensive due to the use of advanced materials, precision manufacturing techniques, and sophisticated control systems. Slitting line manufacturers need to manage costs effectively to remain competitive. This involves optimizing the supply chain for raw materials, improving production efficiency, and streamlining the manufacturing process. They may also look for ways to reduce waste during production and find more cost - effective ways to provide after - sales service and maintenance.
4.
After - sales Service and Support
Providing excellent after - sales service is crucial for slitting line manufacturers. Once the machine is installed at the customer's site, issues may arise during operation. Manufacturers need to have a dedicated service team that can quickly respond to customer inquiries and provide technical support. This includes troubleshooting problems with the machine, providing spare parts, and conducting regular maintenance. Offering training programs for the customer's operators can also help ensure the proper use and maintenance of the slitting line.
VII. Conclusion
Slitting line manufacturers are at the forefront of the metal processing industry, providing the essential machinery for converting metal coils into valuable narrow strips. Their expertise in machine design, manufacturing, and after - sales support is vital for the success of numerous industries that rely on accurately slit metal materials. Despite the challenges they face, continuous innovation, cost - effective production, and a focus on customer satisfaction will enable these manufacturers to thrive and contribute to the growth of the global manufacturing sector.
Coil Slitting Line Manufacturers
Introduction:
In the metal processing industry, coil slitting lines play a crucial role in transforming large coils of metal into narrower strips of specific widths. Coil slitting line manufacturers are responsible for designing, manufacturing, and supplying these sophisticated machines that are essential for various applications in different sectors.
The demand for high-quality coil slitting lines has been on the rise due to the growing need for precision-cut metal strips in industries such as automotive, construction, appliance manufacturing, and packaging. Manufacturers of coil slitting lines must constantly innovate and improve their products to meet the evolving requirements of these industries.
Design and Engineering:
The design and engineering of a coil slitting line is a complex process that requires expertise in mechanical, electrical, and control systems engineering. Manufacturers must consider various factors such as the type of metal to be slit, the required strip widths and thicknesses, the production speed, and the overall efficiency of the line.
The heart of a coil slitting line is the slitting head, which consists of circular knives or blades that cut the coil into narrower strips. The design of the slitting head must ensure accurate and clean cuts, while also being able to handle different types of metals and thicknesses. Manufacturers may use advanced materials and manufacturing techniques to ensure the durability and performance of the slitting head.
In addition to the slitting head, a coil slitting line also includes a decoiler, a tension control system, a recoiler, and various auxiliary equipment such as conveyors and stackers. The decoiler is used to unwind the large coil of metal, while the tension control system ensures that the metal strip is maintained at a constant tension during the slitting process. The recoiler is responsible for rewinding the slit strips into smaller coils.
The control system of a coil slitting line is also an important aspect of its design. Modern coil slitting lines are equipped with advanced control systems that allow for precise control of the slitting process, including speed, tension, and knife positioning. These control systems may include programmable logic controllers (PLCs), human-machine interfaces (HMIs), and sensors to ensure accurate and efficient operation.
Manufacturing Process:
The manufacturing process of a coil slitting line involves several stages, including fabrication, assembly, and testing. Manufacturers must use high-quality materials and precision machining techniques to ensure the durability and performance of the line.
Fabrication typically involves cutting, welding, and machining of various components such as the frame, rollers, and shafts. The components are then assembled into a complete line, with careful attention paid to alignment and precision. Once assembled, the line is thoroughly tested to ensure that it meets the required specifications and performance standards.
Testing may include running the line with dummy coils to check for proper operation of the slitting head, tension control system, and recoiler. Manufacturers may also perform quality control checks such as dimensional accuracy, surface finish, and strip straightness to ensure that the slit strips meet the required quality standards.
Advantages of Working with Reputable Manufacturers:
There are several advantages to working with reputable coil slitting line manufacturers. These include:
1. Quality and Reliability:
Reputable manufacturers are known for producing high-quality coil slitting lines that are reliable and durable. They use advanced materials and manufacturing techniques to ensure that their products can withstand the rigors of continuous operation in industrial environments.
2. Customization:
Many manufacturers offer customization options to meet the specific needs of their customers. This may include customizing the slitting line's dimensions, capabilities, and control systems to suit a particular application or production requirement.
3. Technical Support and Service:
Reputable manufacturers provide excellent technical support and after-sales service. They have a team of experienced engineers and technicians who can assist with installation, commissioning, and troubleshooting. In addition, they may offer maintenance contracts and spare parts support to ensure the long-term performance of the slitting line.
4. Innovation and Upgrades:
Leading manufacturers are constantly innovating and upgrading their products to stay ahead of the competition. They may introduce new features and technologies to improve the efficiency, accuracy, and flexibility of their coil slitting lines. This allows customers to benefit from the latest advancements in metal processing technology.
Applications of Coil Slitting Lines:
Coil slitting lines are used in a wide range of applications across different industries. Some of the common applications include:
1. Automotive Industry:
In the automotive industry, coil slitting lines are used to produce metal strips for body panels, chassis components, and other parts. The precision-cut strips are used in stamping and forming processes to create complex shapes and structures.
2. Construction Industry:
The construction industry uses coil slitting lines to produce metal strips for roofing, siding, and other building materials. The slit strips are often coated or painted to provide corrosion resistance and aesthetic appeal.
3. Appliance Manufacturing:
Appliance manufacturers use coil slitting lines to produce metal strips for refrigerator panels, washing machine drums, and other components. The precision-cut strips are used in stamping and welding processes to create durable and functional appliance parts.
4. Packaging Industry:
The packaging industry uses coil slitting lines to produce metal strips for cans, lids, and other packaging materials. The slit strips are often coated or printed to provide product identification and branding.
Conclusion:
Coil slitting line manufacturers play a crucial role in the metal processing industry by providing high-quality machines that are essential for transforming large coils of metal into narrower strips. With their expertise in design, engineering, and manufacturing, these manufacturers are able to meet the diverse needs of different industries and applications. By working with reputable manufacturers, customers can ensure that they receive reliable and efficient coil slitting lines that meet their specific requirements and contribute to the success of their businesses.