Hotline
+86-136 8495 9862
Email:cennia@szmizhi.com
Add::104,Building 27,Third Industrial Zone, Longxi Community,Longgang District,Shenzhen,China.
Coil Forming & Handling Equipment
Surface Treatment Equipment
Solutions
Application
About Us
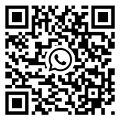
Welcome to MIZHI
For consultation/feedback, please call the service hotline: +86-136 8495 9862 Email:cennia@szmizhi.com
1. Introduction
In the complex and vital landscape of metal manufacturing and processing, the slitting machine line stands as a cornerstone piece of equipment. Its primary function is to transform large - scale metal coils into narrower, more manageable strips, which are then used as fundamental building blocks in countless downstream applications. From the production of automotive parts to the creation of consumer electronics, construction materials, and packaging, the slitting machine line plays an indispensable role in meeting the exacting demands of modern industries. This article delves deep into the components, working principles, applications, advantages, challenges, and future trends associated with slitting machine lines.
2. Components of a Slitting Machine Line
2.1 Uncoiler
The uncoiler is the starting point of the slitting process. It is designed to hold and unwind large metal coils in a controlled manner. There are several types of uncoilers, with the expandable mandrel uncoiler being a popular choice. This type can adapt to different inner diameters of coils, making it versatile for handling a wide range of coil sizes. Hydraulic or pneumatic systems are often used to expand and contract the mandrel, ensuring a secure grip on the coil. The uncoiler is equipped with a tension - control mechanism. Tension control is crucial during unwinding as it prevents the metal strip from sagging or getting over - tightened. For example, in the processing of thin - gauge copper coils for the electronics industry, maintaining the right tension ensures that the delicate strip is unwound smoothly without any creases or breaks.
2.2 Leveler
After unwinding, the metal strip typically has some curvature and unevenness due to the coiling process. The leveler is responsible for straightening the strip. It consists of multiple rolls arranged in a specific pattern. The number of rolls can vary depending on the thickness and material of the metal. For thinner materials like aluminum foil, a 7 - roll leveler might be sufficient, while thicker steel strips may require a 21 - roll leveler. The rolls apply a combination of bending and stretching forces to the strip, gradually eliminating any waves, curls, or bowing. Some advanced levelers have adjustable roll - gap settings, allowing operators to fine - tune the leveling process according to the characteristics of the metal strip, such as its hardness and thickness.
2.3 Slitting Unit
The slitting unit is the core of the slitting machine line. It is where the actual cutting of the wide metal strip into multiple narrower strips takes place. The slitting unit uses circular slitting knives, which are mounted on a shaft. These knives are made of high - quality tool steel and are sharpened to a fine edge. The spacing between the knives can be adjusted to achieve the desired strip widths. There are two main types of slitting operations: shear slitting and razor slitting.
- Shear Slitting: In shear slitting, the circular knives overlap slightly, and as the metal strip passes through, the knives shear the material. This method is suitable for a wide range of metal thicknesses and is commonly used for general - purpose slitting. It can handle materials like mild steel, stainless steel, and aluminum coils efficiently.
- Razor Slitting: Razor slitting uses very sharp, thin blades that are set at a precise angle to the metal strip. This method is mainly used for slitting thin - gauge materials, usually less than 1 mm thick. It is ideal for applications where high - precision edges are required, such as in the production of electronic components.
2.4 Scrap Handling System
During the slitting process, small strips of scrap metal, known as burrs or trimmings, are generated at the edges of the cut strips. A scrap handling system is essential to collect and manage this waste. The system usually consists of scrap winders located at the sides of the slitting unit. These winders continuously collect the scrap and wind it up into a manageable form. Some advanced scrap handling systems can also separate different types of scrap based on their composition, which is useful for recycling purposes.
2.5 Take - up Reels
Once the metal strip is slit into multiple narrower strips, these strips need to be wound back into coils. Take - up reels are used for this purpose. Each take - up reel is designed to wind one of the slit strips. The take - up reels are driven by motors, and they are equipped with tension - control mechanisms to ensure that the strip is wound evenly. Maintaining the right tension during winding is crucial as it affects the quality of the final coil. If the tension is too low, the coil may be loose and prone to tangling; if it is too high, the strip may be stretched or damaged.
2.6 Control System
The control system of a slitting machine line is like the brain of the entire operation. It coordinates the functions of all the components, ensuring smooth and efficient operation. The control system can be based on programmable logic controllers (PLCs) or more advanced computer - numerical - control (CNC) systems. These systems allow operators to set parameters such as the desired strip widths, the speed of the slitting line, the tension levels for unwinding and winding, and the position of the slitting knives. The control system also monitors the operation of the slitting line in real - time. It can detect any abnormal conditions, such as over - tension, under - tension, or misalignment of the slitting knives, and take corrective actions automatically or alert the operator.
3. Working Principle
The operation of a slitting machine line is a highly coordinated and sequential process.
1. Unwinding: The metal coil is loaded onto the uncoiler, and the mandrel is expanded to grip the inner core of the coil. The control system activates the uncoiler motor, which starts to unwind the metal strip at a controlled speed. The tension - control system monitors and adjusts the tension to ensure a smooth unwinding process.
2. Leveling: As the unwound strip enters the leveler, it passes through the series of rolls. The rolls apply bending and stretching forces to straighten the strip. The operator can adjust the roll - gap settings based on the thickness and material of the strip to achieve the best leveling results.
3. Slitting: After leveling, the strip enters the slitting unit. The circular slitting knives, set at the desired spacing, cut the wide strip into multiple narrower strips. The type of slitting operation (shear or razor) depends on the material and the requirements of the final product.
4. Scrap Handling: While the slitting is taking place, the scrap generated at the edges of the cut strips is collected by the scrap winders. The scrap winders continuously wind up the scrap, keeping the work area clean and the slitting process uninterrupted.
5. Winding: The slit strips then move towards the take - up reels. Each take - up reel winds one of the slit strips into a coil. The motors driving the take - up reels maintain a consistent tension on the strips during the winding process, ensuring that the coils are tightly and evenly wound.
4. Applications
4.1 Automotive Industry
In the automotive manufacturing sector, the slitting machine line is of great importance. The automotive industry requires large quantities of precisely cut metal strips for various components. For example, the body panels of cars, such as the doors, hoods, and fenders, are made from metal sheets that are first slit into the appropriate widths and then formed into the required shapes. The high - precision slitting capabilities of the slitting machine line ensure that the metal strips have the exact dimensions needed for the subsequent stamping and forming processes. This precision is crucial for maintaining the structural integrity and aesthetic appeal of the vehicle. Additionally, metal strips are used for the manufacturing of automotive frames, suspension components, and exhaust systems. The ability to produce high - quality slit strips in large volumes meets the high - demand requirements of the automotive industry.
4.2 Electronics Industry
The electronics industry also benefits significantly from the use of slitting machine lines. In the production of electronic components, such as circuit boards, connectors, and enclosures, precise metal strips are required. The razor - slitting option available in many slitting machine lines is particularly well - suited for processing thin - gauge metals, such as copper and aluminum foils, which are commonly used in the electronics industry. The high - precision edges produced by the razor - slitting process are essential for ensuring the proper functioning of electronic components. For example, in the manufacturing of connectors, the precise slitting of metal strips allows for accurate fitting and reliable electrical connections.
4.3 Construction Industry
In the construction industry, the slitting machine line is used for the production of various building materials. Steel strips are slit to specific widths and lengths for applications such as roofing, siding, and structural components. For roofing, the slit steel strips are often further processed into corrugated sheets. The precise slitting ensures that the sheets fit together perfectly during installation, providing a watertight and durable roofing solution. In the case of siding, the metal strips can be cut to the desired dimensions and then coated with protective layers to enhance their corrosion resistance and aesthetic appeal. For structural components, such as steel joists and trusses, the accurate slitting of the steel strips is crucial for the overall strength and stability of the construction structure.
4.4 Packaging Industry
The packaging industry relies on the slitting machine line for the production of metal - based packaging materials. Metal strips are slit to create components for cans, containers, and closures. For example, the sheets for making beverage cans are first slit into narrow strips and then formed into the cylindrical shape of the cans. The high - precision slitting capabilities of the slitting machine line ensure that the cans have consistent dimensions and high - quality seams, which are essential for the integrity and functionality of the packaging. In addition, metal strips are also used for the production of metal lids and closures, where the precise slitting of the strips is crucial for ensuring a proper fit and seal.
5. Advantages
5.1 High Precision
One of the most significant advantages of a slitting machine line is its ability to achieve high - precision cuts. The advanced control systems and precise slitting knives allow for the production of metal strips with very tight width tolerances. In industries where a perfect fit of components is crucial, such as aerospace and medical device manufacturing, this precision is essential. For example, in the production of medical implants made from metal alloys, the slitting machine line can produce strips with tolerances within a few micrometers, ensuring the accuracy and reliability of the final products.
5.2 High - Speed and High - Volume Production
Slitting machine lines are designed for high - speed and high - volume production. They can process large - diameter metal coils at a rapid pace, significantly reducing the production time per unit of slit strip. The automated nature of the entire process, from unwinding to winding, minimizes the need for manual intervention, further enhancing productivity. In a large - scale manufacturing plant, a slitting machine line can produce thousands of meters of slit strips per hour, meeting the high - demand requirements of mass - production industries.
5.3 Material Versatility
These lines are highly versatile in terms of the materials they can process. They can handle a wide range of metals, including different grades of carbon steel, stainless steel, aluminum, copper, and various metal alloys. Whether it is a soft and malleable metal like aluminum or a hard and tough alloy like high - strength steel, the slitting machine line can effectively slit the material with precision. This versatility makes it suitable for a diverse range of industries with different material requirements.
5.4 Cost - Efficiency in the Long Run
Although the initial investment in a slitting machine line can be significant, it offers long - term cost - efficiency. By producing precisely cut metal strips, it reduces material waste. The high - speed production capabilities also mean that more products can be produced in less time, increasing overall productivity. Additionally, the low maintenance requirements of modern slitting machine lines, thanks to their durable components and advanced control systems, further contribute to cost savings over time.
6. Challenges
6.1 High Initial Capital Investment
The purchase and installation of a slitting machine line represent a substantial capital investment. The cost of the equipment can range from hundreds of thousands to several million dollars, depending on its size, capabilities, and the level of automation. In addition to the cost of the slitting machine line itself, there are also expenses associated with infrastructure development, such as a suitable workshop space with proper ventilation, electrical systems to power the equipment, and safety measures. Small and medium - sized enterprises may find it difficult to afford such high - cost equipment, which can limit their growth and competitiveness in the market.
6.2 Skilled Labor Requirement
Operating and maintaining a slitting machine line requires a high level of technical expertise. Workers need to be trained in setting up the machine, programming the control system, adjusting the slitting knives and tension levels, and troubleshooting any issues that may arise during operation. The shortage of skilled labor in some regions can pose a challenge to the efficient use of these machines. Employers may need to invest in comprehensive training programs or hire experienced technicians, which can add to the overall operational costs.
6.3 Quality Control Complexities
Ensuring consistent quality of the slit metal strips is a complex task. Variations in the metal material, such as differences in hardness, thickness, and chemical composition, can affect the slitting process and the quality of the final product. Any misalignment of the slitting knives, improper tension control, or wear and tear of the equipment can also lead to quality issues, such as uneven strip widths, burrs on the edges, and inconsistent coil winding. Implementing effective quality - control measures, such as regular inspections, in - line monitoring, and statistical process control, is essential but can be resource - intensive and time - consuming.
6.4 Technological Obsolescence
The field of metal - processing technology is constantly evolving. New and more advanced slitting technologies and equipment are being developed regularly. Slitting machine lines may face the challenge of technological obsolescence over time. To remain competitive, manufacturers may need to upgrade their existing slitting machine lines or invest in new, more advanced models. This not only involves significant financial investment but also disrupts the production process during the transition period.
7. Future Trends
7.1 Integration of Industry 4.0 Technologies
The future of slitting machine lines lies in the integration of Industry 4.0 technologies, such as the Internet of Things (IoT), artificial intelligence (AI), and machine learning (ML). IoT sensors can be installed on the slitting machine line to monitor various parameters, such as temperature, vibration, and cutting forces, in real - time. This data can be transmitted to a central control system, where AI and ML algorithms can analyze it to predict equipment failures, optimize cutting parameters, and improve overall efficiency. For example, AI can adjust the cutting speed and tension based on the real - time condition of the metal strip and the cutting tool, reducing the risk of tool wear and improving the quality of the cuts.
7.2 Development of Sustainable and Energy - Efficient Solutions
As environmental concerns become more prominent, there will be a growing focus on developing sustainable and energy - efficient slitting machine lines. This may involve the use of more energy - efficient motors, the development of recycling systems for scrap materials generated during the slitting process, and the optimization of the overall manufacturing process to reduce energy consumption. Additionally, manufacturers may explore the use of alternative materials and manufacturing techniques that are more environmentally friendly.
7.3 Customization and Flexibility
In response to the increasing demand for customized products in various industries, slitting machine lines will likely become more customizable and flexible. Manufacturers will be able to adjust the slitting machine line to produce a wider range of strip widths, thicknesses, and edge qualities. This will allow them to better meet the specific requirements of individual customers and serve niche markets more effectively.
In conclusion, the slitting machine line is an essential and highly sophisticated piece of equipment in the metal - processing industry. Its components, working principle, wide - ranging applications, numerous advantages, and the challenges it faces all contribute to its significance in modern manufacturing. With the advent of new technologies and the evolving demands of various industries, the slitting machine line is set to undergo further advancements, playing an even more crucial role in the future of metal processing.