Hotline
+86-136 8495 9862
Email:cennia@szmizhi.com
Add::104,Building 27,Third Industrial Zone, Longxi Community,Longgang District,Shenzhen,China.
Coil Forming & Handling Equipment
Surface Treatment Equipment
Solutions
Application
About Us
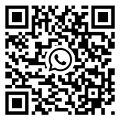
Welcome to MIZHI
For consultation/feedback, please call the service hotline: +86-136 8495 9862 Email:cennia@szmizhi.com
I. Introduction
The slitting and cut - to - length line is a crucial piece of equipment in the metal processing industry. It combines two important functions: slitting wide coils of metal into narrower widths and cutting these slit coils to specific lengths. This technology has revolutionized the way metal is processed, allowing for greater flexibility, efficiency, and precision in manufacturing processes across various industries.
II. Components of a Slitting and Cut - to - Length Line
A. Uncoiling Unit
1. Mandrel and Expansion Mechanism
The uncoiling unit is the starting point of the slitting and cut - to - length line. The mandrel is a central component where the metal coil is placed. It has an expansion mechanism, which is typically hydraulic or mechanical. The expansion mechanism is designed to firmly grip the inner diameter of the coil. For example, in a steel coil slitting and cut - to - length line, the mandrel must be able to accommodate different coil sizes. A hydraulic expansion system can provide more precise control, ensuring a secure fit for coils with varying inner diameters, which can range from a few hundred millimeters to over a meter in some cases.
2. Brake and Tension Control
To control the uncoiling process, a brake system is installed. This system regulates the speed at which the coil unwinds. Tension control is also an important aspect of the uncoiling unit. Maintaining the right tension is crucial as it affects the quality of the slitting and cutting processes. If the tension is too high, it can cause the coil to deform or break, while too low tension may result in wrinkling or improper feeding of the material. Advanced uncoiling units use sensors and feedback systems to adjust the brake and tension in real - time.
B. Slitting Section
1. Slitting Blades
The slitting section contains the slitting blades, which are the key elements for dividing the wide coil into narrower widths. These blades are made of high - quality materials such as tool steel or carbide, depending on the type of metal being slit. For instance, when slitting hard - to - cut metals like high - strength alloy steels, carbide blades are often preferred due to their superior hardness and wear resistance. The blades are mounted on shafts, and the number of blades can be adjusted according to the desired number of slits. Usually, the slitting blades are arranged in a parallel configuration, and their spacing determines the width of the slit coils.
2. Blade Gap Adjustment
Precise adjustment of the blade gap is essential for accurate slitting. The gap needs to be set according to the thickness of the coil. If the gap is too wide, the slitting quality will deteriorate, leading to rough edges and burrs. On the other hand, if the gap is too narrow, the blades may collide or wear out quickly. Modern slitting and cut - to - length lines often feature automated blade gap adjustment systems, which can be calibrated based on the input of the coil thickness. This ensures consistent slitting quality across different coil batches.
3. Blade Drive System
The slitting blades are driven by a drive system, usually consisting of an electric motor. The drive system provides the rotational force required for the blades to cut through the metal coil. The power of the drive system needs to be sufficient to handle different coil thicknesses and widths. For example, thicker coils demand a more powerful drive system to ensure smooth and continuous slitting. The speed of the blade rotation can also be adjusted to optimize the slitting process based on factors such as the type of metal and the desired slit width.
C. Edge Trimming Unit
1. Trimming Blades
The edge trimming unit is responsible for removing any irregular or damaged edges from the slit coils. The trimming blades are similar in nature to the slitting blades but are specifically designed for edge trimming. They are often adjustable in terms of their cutting depth, allowing for precise removal of the edges. In a slitting and cut - to - length line for aluminum coils, for example, the trimming blades can be set to remove a small amount of material from the edges to ensure a clean and smooth finish.
2. Alignment and Positioning
Accurate alignment and positioning of the trimming blades are crucial for effective edge trimming. The unit uses sensors and servo - motor - based control systems to detect the position of the coil edges and adjust the trimming blades accordingly. This ensures that the edges are trimmed evenly and precisely, which is important for the final quality of the product.
D. Cut - to - Length Section
1. Measuring System
The cut - to - length section begins with a measuring system that determines the exact length of the material to be cut. There are various methods for measuring, such as encoder - based systems. Encoders are devices that convert the mechanical movement of the material into electrical signals, which are then processed to calculate the length. Laser - based measurement systems are also becoming more common. They use lasers to detect the position of the material and can provide very high - precision measurements, especially for materials with irregular surfaces or when extremely accurate cuts are required.
2. Cutting Mechanism
The cutting mechanism in the cut - to - length section can be of different types. Shear - type cutting is a common method, where a sharp blade moves perpendicular to the direction of the material flow to cut through it. This method is simple and reliable for cutting metal coils. Another option is laser cutting, which offers extremely high precision and the ability to cut complex shapes. However, laser cutting is generally more expensive and may be slower for some applications. Plasma cutting can also be used, especially for thicker - gauge metals within the slitting and cut - to - length line operations.
3. Stacking and Bundling System
After the material is cut to length, a stacking and bundling system is used to organize the cut pieces. The stacking system can be automated, using robotic arms or conveyors to pick up the cut pieces and place them in an orderly fashion. Bundling systems are then used to group multiple cut pieces together, often using straps or wire to hold them in place. This is important for easy handling, storage, and transportation of the cut - to - length products.
III. Working Principles of a Slitting and Cut - to - Length Line
A. Uncoiling and Initial Feed
The process starts with the uncoiling of the metal coil on the uncoiling unit. The coil is slowly unwound, and the material is fed through a series of rollers towards the slitting section. The rollers guide the material and help maintain the proper tension. The speed of the uncoiling and feeding is carefully controlled to ensure a smooth and continuous flow of the material.
B. Slitting Process
As the material enters the slitting section, the slitting blades start to cut the wide coil into narrower widths. The blades rotate at a high speed, and the coil is continuously fed through them. The cutting force exerted by the blades is determined by factors such as the blade sharpness, the speed of rotation, and the thickness of the coil. During the slitting process, the edge trimming unit may also be activated simultaneously to remove any unwanted edges from the newly slit coils.
C. Cut - to - Length Operation
After slitting, the now - slit coils move to the cut - to - length section. The measuring system first determines the length of the material to be cut. Based on this measurement, the cutting mechanism is activated when the appropriate length of material has passed through. The cut pieces are then sent to the stacking and bundling system for further processing.
IV. Applications of Slitting and Cut - to - Length Lines
A. Construction Industry
1. Roofing and Siding
In the construction industry, slitting and cut - to - length lines are used to produce roofing and siding materials. Metal coils are slit into the appropriate widths for roofing sheets and siding panels, and then cut to length for easy installation. This allows for efficient use of materials and ensures that the roofing and siding components fit together precisely during construction. For example, steel or aluminum coils can be processed to produce roofing and siding materials with different widths and lengths to meet the specific design requirements of a building.
2. Structural Components
These lines are also used to produce structural components such as purlins and girts. The ability to slit and cut to length allows for the production of components with the exact dimensions required for a building's frame. This is crucial for ensuring the structural integrity of the building and for optimizing the use of materials.
B. Automotive Industry
1. Body Panels
In the automotive industry, slitting and cut - to - length lines are used to process metal coils for body panels. The coils are slit into widths suitable for car doors, hoods, fenders, etc., and then cut to the appropriate lengths for assembly. This helps in reducing waste and ensuring that the body panels fit together perfectly during the manufacturing process. For example, aluminum coils can be slit and cut to length to produce lightweight body panels that contribute to improved fuel efficiency in vehicles.
2. Interior Components
Metal coils are also processed through slitting and cut - to - length lines for the production of interior automotive components such as dashboards and seat frames. The ability to customize the width and length of the metal pieces is essential for meeting the design and functionality requirements of these components.
C. Electrical Industry
1. Transformer Coils
In the electrical industry, slitting and cut - to - length lines are used to produce the narrow - width metal strips required for transformer coils. The precise slitting and cutting to length are crucial for the proper functioning of transformers, as it affects the electrical properties of the coils. Copper or aluminum coils are slit and cut to the exact dimensions needed for winding around the transformer cores.
2. Electrical Enclosures
These lines are also used to produce metal sheets for electrical enclosures. The sheets are slit to the appropriate widths and cut to length to form enclosures that protect electrical components from environmental factors such as dust, moisture, and electromagnetic interference.
V. Factors Affecting the Performance of a Slitting and Cut - to - Length Line
A. Metal Properties
1. Thickness
The thickness of the metal coil has a significant impact on the performance of the slitting and cut - to - length line. Thicker coils require more powerful slitting blades and drive systems, as well as more precise tension control. For example, a 5 - mm - thick steel coil will need a more robust slitting setup compared to a 1 - mm - thick coil.
2. Type of Metal
The type of metal, such as steel, aluminum, or copper, also affects the performance. Different metals have different hardness levels, ductility, and melting points. For instance, aluminum is relatively softer and more ductile than steel, which means that the slitting and cutting parameters need to be adjusted accordingly. Copper has a high electrical conductivity and a relatively low melting point, which can pose challenges during the slitting and cutting processes if not properly controlled.
B. Machine - related Factors
1. Blade Quality
The quality of the slitting and cutting blades is crucial for the performance of the line. High - quality blades made of appropriate materials (e.g., carbide for hard metals) will result in better slitting and cutting quality. Dull or damaged blades will lead to rough cuts, burrs, and increased wear on other machine components.
2. Machine Calibration
Proper calibration of the entire slitting and cut - to - length line is essential. This includes calibrating the uncoiling and tension control systems, the slitting section for blade gap and rotation speed, the cut - to - length section for measurement accuracy and cutting mechanism, and the edge trimming unit for proper alignment. Incorrect calibration can result in poor - quality products and reduced efficiency.
VI. Advantages of Using a Slitting and Cut - to - Length Line
A. Precision
One of the main advantages is the high precision that can be achieved. The ability to slit and cut to length with a high degree of accuracy ensures that the final products meet the exact requirements of various industries. For example, in the automotive industry, precise body panel dimensions are crucial for a perfect fit during assembly.
B. Efficiency
These lines can significantly improve the efficiency of the metal processing operation. By combining slitting and cut - to - length functions in one line, the production process is streamlined. The automated nature of many of these lines also reduces the need for manual labor, further increasing efficiency. Additionally, the ability to process coils continuously reduces downtime and increases throughput.
C. Material Utilization
Slitting and cut - to - length lines allow for better material utilization. By slitting wide coils into narrower widths and then cutting to length, manufacturers can produce a variety of products from a single coil, reducing waste. This is especially important in industries where the cost of raw materials is high, such as the metal industry.
VII. Challenges and Future Developments
A. Challenges
1. Blade Wear
Blade wear is a significant challenge in slitting and cut - to - length lines. The slitting and cutting blades are subject to high - stress conditions during operation, which leads to wear. Regular blade replacement is necessary, which can be costly and time - consuming. The wear rate also depends on factors such as the type of metal being processed and the cutting parameters.
2. Maintenance and Downtime
The complex nature of these lines requires regular maintenance. Components such as the uncoiling unit, slitting section, and cut - to - length section need to be maintained to ensure optimal performance. Downtime for maintenance can be a problem, especially in high - volume production environments. Finding ways to reduce maintenance time and increase the reliability of the line is a continuous challenge.
B. Future Developments
1. Automation and Industry 4.0 Integration
The future of slitting and cut - to - length lines will likely see increased automation and integration with Industry 4.0 concepts. Machines will be more connected, allowing for remote monitoring and control. Predictive maintenance based on real - time data analysis will become more common. For example, sensors can be installed to monitor blade wear, tension levels, and other key parameters, and the system can predict when maintenance is required and schedule it accordingly.
2. Advanced Cutting Technologies
There will be continuous improvement in cutting technologies. New blade materials and designs may be developed to reduce blade wear and improve cutting quality. For example, the development of self - sharpening blades or blades with advanced coatings could significantly extend their lifespan. Additionally, new cutting methods, such as hybrid cutting techniques that combine the advantages of different cutting mechanisms, may emerge.
In conclusion, the slitting and cut - to - length line is an essential part of the metal processing industry. It offers numerous advantages in terms of precision, efficiency, and material utilization, but also faces challenges such as blade wear and maintenance requirements. With future developments in automation and cutting technologies, these lines are expected to become even more efficient and reliable, further enhancing their importance in various industries.