Hotline
+86-136 8495 9862
Email:cennia@szmizhi.com
Add::104,Building 27,Third Industrial Zone, Longxi Community,Longgang District,Shenzhen,China.
Coil Forming & Handling Equipment
Surface Treatment Equipment
Solutions
Application
About Us
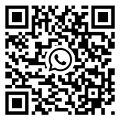
Welcome to MIZHI
For consultation/feedback, please call the service hotline: +86-136 8495 9862 Email:cennia@szmizhi.com
I. Introduction
The slitting and cut to length line is a highly versatile and essential piece of equipment in the metal processing industry. It combines two crucial functions: slitting, which involves dividing wide metal coils into narrower strips, and cut to length, where these strips or the original coils are precisely cut into specific lengths. This dual-capability machine caters to a wide array of industrial needs, playing a pivotal role in the production of everything from automotive parts and electrical components to construction materials and packaging.
II. Key Components and Their Functions
1. Uncoiler
The uncoiler is the first stage of the process. It is designed to hold and unwind metal coils of various sizes and weights. For heavy-duty industrial applications, the uncoiler can handle coils weighing several tons. It features a mandrel that can be adjusted to fit the coil's inner diameter snugly. A reliable braking system is incorporated to control the unwinding speed, preventing the coil from spinning too fast and causing damage or inaccurate feeding. In the production of steel sheets for building construction, the uncoiler must ensure a steady and controlled release of the coil to initiate the subsequent slitting and cutting operations smoothly.
2. Straightener
After uncoiling, the metal often has some degree of curvature or warp. The straightener's role is to flatten the metal using a series of rollers. These rollers apply pressure in different directions to eliminate any bends. The adjustment of the rollers is a delicate process as too much pressure can damage the metal, while too little won't achieve the desired straightening effect. In the manufacturing of aluminum strips for the electrical industry, where flatness is crucial for conductivity and proper assembly, the straightener ensures the metal is in optimal condition before further processing.
3. Slitting Unit
The slitting unit is the core component for the slitting function. It consists of circular knives or blades that are arranged in a specific configuration. The number and spacing of the blades can be adjusted according to the desired width of the slit strips. For example, in the production of narrow steel strips for springs, the slitting unit can be set to produce strips with a precise width tolerance to meet the exact requirements of the spring manufacturing process. The blades need to be of high quality, sharp, and properly maintained to ensure clean and accurate slits. Some advanced slitting units also incorporate automatic blade gap adjustment systems to optimize cutting performance.
4. Tension Control System
Maintaining the right tension in the metal throughout the process is vital. The tension control system uses sensors and actuators to monitor and adjust the tension. This ensures that the metal doesn't sag or become overly taut during slitting and cutting, which could lead to inconsistent widths or lengths. In the production of thin copper strips for electronics, precise tension control is essential to prevent the strips from wrinkling or breaking, safeguarding the integrity of the final product.
5. Cutting Unit (for Cut to Length)
Similar to the cut to length lines described earlier, this unit has its own set of features. It can employ shearing or laser cutting methods. Shearing is often used for thicker materials and involves two blades moving relative to each other to make a clean cut. Laser cutting, on the other hand, offers higher precision and is suitable for thinner materials or when complex shapes are required. In the production of decorative metal panels for architecture, laser cutting allows for the creation of intricate patterns and smooth edges, enhancing the aesthetic appeal.
6. Stacker or Conveyor
Once the metal has been slit and cut to length, it needs to be organized. The stacker is used to neatly pile up the cut pieces. It can be programmed to stack them in a particular order or pattern, which is beneficial for inventory management and subsequent handling. In some cases, a conveyor system is preferred. The conveyor can transport the cut pieces directly to the next stage of production, such as a welding station or a packaging area. For example, in a furniture manufacturing plant, the conveyor quickly moves the cut metal parts to the painting area, streamlining the production process.
III. Working Principle
The operation begins with loading the metal coil onto the uncoiler. As the uncoiler unwinds the coil, the metal passes through the straightener to be flattened. Then, it enters the slitting unit where it is divided into narrower strips according to the preset width. The tension control system continuously monitors and adjusts the tension to keep the process stable. After slitting, the strips (or the original coil if only cut to length is required) move to the cutting unit. Here, the cutting process is initiated based on the desired length settings, which are entered and controlled through a user-friendly interface. Once cut, the final products are either stacked or conveyed as per the production requirements. The entire process is overseen by a central control system that ensures the smooth running of the line and the accuracy of the output.
IV. Applications
1. Automotive Industry
In the automotive industry, slitting and cut to length lines are used to process metal sheets for body panels, chassis components, and interior trim. The ability to slit coils into precise widths and cut them to exact lengths is essential for the proper assembly of vehicles. For example, the production of car doors requires metal sheets that are both the right width and length to ensure a seamless fit and optimal aerodynamic performance.
2. Electrical and Electronics Industry
For the electrical and electronics sectors, these lines are used to produce copper and aluminum strips for conductors, connectors, and circuit boards. The precision slitting and cutting ensure that the metal components meet the exact electrical and dimensional requirements. In the manufacture of printed circuit boards, the copper foil needs to be slit and cut to precise dimensions to enable accurate etching and component mounting.
3. Construction and Building Materials
In the construction field, the lines are employed to make metal roofing sheets, siding panels, and structural steel components. The efficient slitting and cutting capabilities enable on-site installation to be carried out smoothly. Metal roofing sheets can be cut to the exact length required for a particular roof design, minimizing waste and installation effort.
4. Packaging Industry
In the packaging industry, slitting and cut to length lines are used to produce metal foils for food and beverage packaging, as well as paperboard and plastic substrates. The ability to control the width and length of the materials is crucial for creating packaging that is both functional and aesthetically pleasing. For example, the production of aluminum foil for chocolate wrappers requires precise slitting and cutting to fit the product snugly.
V. Advantages
1. Versatility
The combination of slitting and cut to length functions in one machine makes it highly adaptable to different manufacturing requirements. It can handle a wide range of metal materials, thicknesses, and widths, catering to diverse industries.
2. Precision
These lines offer high precision in both slitting and cutting operations. The width and length tolerances can be extremely tight, ensuring that the final products meet the exact specifications of the end-users. In the production of high-tech products like microelectronics, this precision is non-negotiable.
3. Efficiency
By integrating two essential functions, the slitting and cut to length line reduces production time and costs. It eliminates the need for separate slitting and cutting machines, streamlining the manufacturing process and increasing productivity.
4. Quality of Output
The advanced components and control systems result in a high-quality output. Clean slits and accurate cuts mean fewer defects and rework, leading to a more reliable final product.
VI. Maintenance and Safety Considerations
1. Maintenance
Regular maintenance is crucial to keep the slitting and cut to length line in top-notch condition. The blades of the slitting and cutting units need to be sharpened or replaced regularly. The rollers of the straightener should be checked for wear and tear and lubricated as needed. The tension control system and sensors also require periodic calibration to ensure accurate operation.
2. Safety
Safety is of utmost importance. The machine has many moving parts, such as the uncoiler, rollers, blades, and conveyor, which can pose hazards. Safety guards should be installed around the cutting and slitting areas to prevent accidental contact. Operators should be trained to follow proper safety procedures, including wearing appropriate personal protective equipment and ensuring the machine is properly shut down and locked out during maintenance.
In conclusion, the slitting and cut to length line is a powerhouse of the metal processing industry. Its dual functionality, precision, and versatility make it an invaluable asset for manufacturers across multiple industries. With proper maintenance and safety measures, it can continue to deliver high-quality slit and cut metal products for years to come.