Hotline
+86-136 8495 9862
Email:cennia@szmizhi.com
Add::104,Building 27,Third Industrial Zone, Longxi Community,Longgang District,Shenzhen,China.
Coil Forming & Handling Equipment
Surface Treatment Equipment
Solutions
Application
About Us
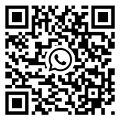
Welcome to MIZHI
For consultation/feedback, please call the service hotline: +86-136 8495 9862 Email:cennia@szmizhi.com
In the manufacturing realm, the production of miniature castings has witnessed a significant upswing in recent years. These tiny components find applications in diverse industries such as electronics, medical devices, and jewelry. Given their small size and often delicate nature, the surface treatment of miniature castings demands specialized equipment. Enter the small - parts - friendly tumble belt shot blasting machine, a revolutionary piece of machinery designed specifically to meet the unique requirements of treating miniature castings. This machine offers a highly efficient and gentle yet effective method of surface treatment, ensuring that the quality and integrity of these small components are maintained while achieving the desired surface finish and properties.
Working Principle of the Tumble Belt Shot Blasting Machine
Tumble Belt Mechanism
The tumble belt is the core of this machine's operation for handling small parts. It consists of a specially designed conveyor belt that moves in a continuous loop. The belt is made of a material that is both durable and gentle on the miniature castings to prevent any physical damage during the treatment process. The belt has a series of small compartments or pockets evenly spaced along its length. These compartments are sized to securely hold the miniature castings without allowing them to move freely and collide with each other in a way that could cause scratches or deformations.
As the belt moves, the miniature castings placed in these compartments are gradually tumbled. This tumbling action is crucial as it exposes all surfaces of the castings to the abrasive media in the shot blasting chamber. The speed of the tumble belt can be adjusted according to the type and size of the castings, as well as the intensity of surface treatment required. For very delicate miniature castings, a slower belt speed may be chosen to ensure a more gentle tumbling motion, while for castings that can withstand a more vigorous treatment, a faster speed can be utilized to expedite the process.
Shot Blasting System
Complementing the tumble belt is the shot blasting system. This system is responsible for propelling abrasive media, typically small metal or ceramic shots, at high velocities onto the surface of the miniature castings. The shot blasting unit is equipped with one or more powerful centrifugal wheels. These wheels are designed to accelerate the abrasive shots to speeds ranging from 50 to 100 meters per second, depending on the specific machine settings and the requirements of the surface treatment.
The shots are fed into the center of the centrifugal wheels and are then flung outwards through carefully engineered vanes. The direction and intensity of the shot flow can be precisely controlled. Multiple nozzles or shot - throwing wheels are strategically positioned around the tumble belt within the blasting chamber. This arrangement ensures that the miniature castings, as they are tumbled along the belt, are exposed to a comprehensive and even distribution of abrasive shots from various angles. This thorough coverage is essential for achieving a uniform surface finish across all parts of the miniature castings.
Abrasive Recovery and Recycling
In a production environment, efficient use of resources is paramount. The tumble belt shot blasting machine is equipped with an advanced abrasive recovery and recycling system. After the abrasive shots have impacted the surface of the miniature castings and fallen to the bottom of the blasting chamber, they are collected through a series of chutes and conveyors. The used shots are then passed through a separation system. This system is designed to remove any dust, debris, or broken shots that may have been generated during the blasting process.
The separation process typically involves a combination of mechanical sieving and air - based separation techniques. The clean and reusable shots are then recycled back into the shot blasting system for further use. This closed - loop system not only reduces the cost associated with constantly purchasing new abrasive media but also minimizes environmental waste, making it an environmentally friendly and cost - effective solution for the surface treatment of miniature castings.
Advantages of the Tumble Belt Shot Blasting Machine for Miniature Castings
Gentle Treatment for Delicate Parts
1. Minimal Physical Damage: Miniature castings, especially those used in the electronics and medical device industries, are often extremely delicate. The tumble belt's gentle handling mechanism, with its carefully designed compartments and controlled movement, ensures that the castings are not subjected to excessive mechanical stress. Unlike traditional tumbling methods where parts may collide haphazardly, the tumble belt keeps the miniature castings in a controlled position, reducing the risk of scratches, dents, or other physical damage that could compromise the functionality or aesthetics of the components.
2. Preservation of Precision Dimensions: In applications such as micro - electromechanical systems (MEMS) or precision medical implants, the dimensional accuracy of miniature castings is of utmost importance. The gentle tumbling and shot blasting process of this machine helps preserve the precise dimensions of the castings. The controlled exposure to abrasive media ensures that only the surface layer is affected, without causing any significant changes to the overall shape or size of the components. This is crucial as even a slight deviation in dimensions could render the miniature casting unusable in its intended application.
Uniform Surface Finish
1. Comprehensive Coverage: The combination of the tumbling action of the belt and the strategically positioned shot - throwing wheels results in a comprehensive coverage of the surface of the miniature castings. As the castings are continuously tumbled along the belt, all sides and corners are exposed to the abrasive shots. This ensures that the entire surface of the casting receives an even treatment, eliminating any areas that may be missed in less sophisticated surface treatment methods. Whether it is a complex - shaped miniature casting with intricate details or a simple geometric shape, the tumble belt shot blasting machine can achieve a uniform surface finish across the entire part.
2. Consistent Surface Roughness: For many applications, a consistent surface roughness is required for proper functionality. The machine allows for precise control over the intensity of the shot blasting process. By adjusting parameters such as the speed of the centrifugal wheels (which determines the velocity of the abrasive shots) and the duration of exposure, manufacturers can achieve a highly consistent surface roughness across all miniature castings in a production batch. This consistency is vital, for example, in the case of jewelry - making where a uniform surface finish is essential for a high - quality, aesthetically pleasing product.
High - Efficiency in Small - Parts Production
1. Continuous Processing: The continuous operation of the tumble belt enables a high - volume production of miniature castings. Unlike batch - processing methods that require manual loading and unloading of parts between each treatment cycle, the tumble belt shot blasting machine can continuously feed small parts into the blasting chamber. This significantly increases the throughput, allowing manufacturers to meet the high demand for miniature castings in a timely manner. In an electronics manufacturing facility that produces thousands of tiny connectors or sensors daily, the continuous processing capability of this machine can greatly enhance production efficiency.
2. Customizable Processing Parameters: The machine offers a wide range of customizable processing parameters to accommodate different types of miniature castings and surface treatment requirements. The speed of the tumble belt, the intensity of shot projection, and the type and size of abrasive media can all be adjusted. This flexibility means that manufacturers can quickly adapt the machine to treat different batches of miniature castings, whether they are made of different materials (such as aluminum, brass, or stainless steel) or require different levels of surface cleaning, polishing, or strengthening.
Cost - Effectiveness
1. Reduced Labor Costs: The automated nature of the tumble belt shot blasting machine reduces the need for extensive manual labor. In traditional surface treatment methods for small parts, workers may need to manually load, unload, and tumble the components, which is a time - consuming and labor - intensive process. With this machine, the only human intervention required is periodic monitoring and maintenance. This not only cuts down on labor costs but also reduces the variability in the quality of surface treatment that may be associated with manual work, leading to more consistent product quality.
2. Efficient Abrasive Usage: The abrasive recovery and recycling system of the machine ensures that the abrasive media is used efficiently. In a production environment where large quantities of miniature castings are treated, the cost of abrasive media can be a significant expense. By recycling and reusing the shots, manufacturers can save a substantial amount of money over time. Additionally, the reduced need to dispose of used abrasive media also reduces environmental costs associated with waste management.
Applications of the Tumble Belt Shot Blasting Machine in Miniature Casting Production
Electronics Industry
1. Miniature Connectors and Components: In the electronics industry, there is a constant need for small, high - performance connectors and components. These miniature castings are often made of materials such as copper or its alloys. The tumble belt shot blasting machine is used to clean the surface of these components, removing any impurities or oxidation that may have formed during the casting process. The resulting clean surface improves the electrical conductivity and soldering properties of the connectors. For example, in the production of micro - USB connectors, the shot - blasted surface ensures a reliable connection and better adhesion of solder during the assembly process.
2. MEMS Devices: Micro - electromechanical systems (MEMS) devices are at the forefront of modern electronics. These tiny devices, which combine mechanical and electrical components, require extremely precise surface treatment. The tumble belt shot blasting machine can be used to etch or smooth the surface of MEMS components, improving their performance and reliability. By controlling the shot blasting parameters, manufacturers can achieve the desired surface roughness and microstructure, which is crucial for the proper functioning of MEMS sensors and actuators.
Medical Device Industry
1. Surgical Implants and Instruments: Miniature castings are widely used in the production of surgical implants and instruments. The surface quality of these components is of critical importance as it can affect their biocompatibility and functionality. The tumble belt shot blasting machine is used to clean and polish the surface of implants such as screws, pins, and stents. The gentle treatment of the machine ensures that the integrity of the implant material is maintained while achieving a smooth surface that reduces the risk of tissue irritation. In the case of surgical instruments, the shot - blasted surface can improve the grip and durability of the instrument, enhancing the surgeon's control during procedures.
2. Diagnostic Equipment Components: Many diagnostic equipment components, such as those used in microfluidic systems for medical testing, are made of miniature castings. The tumble belt shot blasting machine can be used to clean and prepare the surface of these components for further processing, such as coating or bonding. The uniform surface finish achieved by the machine is essential for ensuring the proper flow of fluids and the accurate performance of diagnostic tests.
Jewelry Industry
1. Fine Jewelry Components: The jewelry industry relies heavily on miniature castings for creating intricate and delicate jewelry pieces. The tumble belt shot blasting machine is used to give the cast jewelry components a uniform and polished surface finish. Whether it is a small pendant, a delicate earring, or a detailed charm, the machine can enhance the aesthetic appeal of the piece. The ability to achieve a consistent surface roughness allows jewelers to apply different finishing techniques, such as electroplating or enameling, with better results.
2. Watch Components: Miniature castings are also used in the production of watch components, such as watch cases, bracelets, and gears. The tumble belt shot blasting machine can be used to clean and strengthen the surface of these components. The shot - peening effect of the blasting process can improve the fatigue resistance of watch gears, ensuring smooth and accurate movement. For watch cases and bracelets, the machine can create a satin - like or polished finish, enhancing the overall appearance of the timepiece.
Operation and Maintenance of the Tumble Belt Shot Blasting Machine
Operation
1. Initial Setup: Before starting the treatment of miniature castings, the machine needs to be properly set up. This involves adjusting the speed of the tumble belt according to the size and fragility of the castings. The operator also needs to select the appropriate abrasive media and set the intensity of the shot blasting by adjusting the speed of the centrifugal wheels. Additionally, safety checks must be carried out to ensure that all protective guards are in place and the machine is in proper working condition.
2. Loading and Unloading: Miniature castings are carefully loaded into the compartments of the tumble belt at the input end of the machine. The operator needs to ensure that the castings are evenly distributed and securely placed in the compartments. At the output end, the treated castings are unloaded and inspected for quality. If any castings show signs of improper treatment, the machine settings may need to be adjusted for subsequent batches.
3. Monitoring: During the operation, the operator should continuously monitor the machine. This includes checking the performance of the shot blasting system, ensuring that the tumble belt is moving smoothly, and observing the quality of the treated castings. If any issues are detected, such as uneven surface treatment, abnormal noise from the machine, or problems with the abrasive recovery system, the machine should be stopped immediately for troubleshooting.
Maintenance
1. Regular Inspection: Regular inspection of the machine is essential to ensure its long - term reliable operation. Components such as the tumble belt, centrifugal wheels, and abrasive recovery system should be inspected for wear and tear. The tumble belt may need to be replaced periodically if it shows signs of damage or stretching. The vanes on the centrifugal wheels, which are subject to high - velocity impacts from the abrasive shots, should be checked for wear and replaced when necessary. The abrasive recovery system should be inspected to ensure that there are no blockages in the chutes or conveyors.
2. Lubrication: Proper lubrication of moving parts is crucial for the smooth operation of the machine. The bearings on the tumble belt rollers and the motors driving the centrifugal wheels need to be lubricated regularly to reduce friction and prevent premature failure. This helps to maintain the efficiency of the machine and reduces the risk of breakdowns during production.
3. Abrasive Media Management: The quality of the abrasive media also needs to be managed. Over time, the abrasive shots may become worn or contaminated. The operator should periodically check the quality of the recycled abrasive and add new abrasive as needed to maintain the effectiveness of the shot blasting process. The size and type of abrasive media may also need to be adjusted depending on the changing requirements of the miniature casting production.
Conclusion
The small - parts - friendly tumble belt shot blasting machine has emerged as an essential tool in the production of miniature castings. Its unique design and working principle offer a host of advantages, including gentle treatment for delicate parts, uniform surface finish, high - efficiency production, and cost - effectiveness. With applications spanning across diverse industries such as electronics, medical devices, and jewelry, this machine has revolutionized the surface treatment of miniature castings. By understanding its operation and maintenance requirements and leveraging its capabilities, manufacturers can enhance the quality and productivity of their miniature casting production processes, meeting the growing demand for high - quality small components in the global market. As technology continues to evolve, it is expected that further improvements will be made to the tumble belt shot blasting machine, further enhancing its performance and versatility in the treatment of miniature castings.