Hotline
+86-136 8495 9862
Email:cennia@szmizhi.com
Add::104,Building 27,Third Industrial Zone, Longxi Community,Longgang District,Shenzhen,China.
Coil Forming & Handling Equipment
Surface Treatment Equipment
Solutions
Application
About Us
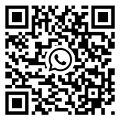
Welcome to MIZHI
For consultation/feedback, please call the service hotline: +86-136 8495 9862 Email:cennia@szmizhi.com
ion
1. Introduction
In the realm of surface preparation and cleaning, soda blasting machines have emerged as a revolutionary and highly versatile solution. Surface treatment is a critical step in numerous industries, including automotive, aerospace, restoration, and manufacturing. Traditional blasting methods often involve harsh abrasives that can damage delicate surfaces or leave behind residues that are difficult to clean. Soda blasting, on the other hand, offers a unique combination of effectiveness and gentleness, making it an ideal choice for a wide range of applications. This article will comprehensively explore soda blasting machines, covering their components, working principles, applications, advantages, challenges, and future trends.
2. Components of Soda Blasting Machines
2.1 Hopper
The hopper is a central component of a soda blasting machine. It serves as the storage container for the soda abrasive, which is typically sodium bicarbonate. Hoppers come in various sizes, depending on the scale of the operation. Small - scale, portable soda blasting machines may have hoppers with a capacity of a few kilograms, while industrial - grade machines can have hoppers that can hold hundreds of kilograms of soda. The hopper is designed to feed the soda into the blasting system at a controlled rate. Some hoppers are equipped with agitators or vibrators. These mechanisms prevent the soda from caking or bridging, ensuring a consistent flow of the abrasive material. For example, in a restoration project where the soda blasting machine is used to clean intricate metal parts, a well - functioning hopper with an agitator ensures that the soda is evenly distributed and continuously fed into the blasting process.
2.2 Compressor
A compressor is an essential part of the soda blasting setup. It provides the necessary air pressure to propel the soda particles through the blasting nozzle. The power and capacity of the compressor depend on the size and type of the soda blasting machine. For small, handheld soda blasters, a relatively small - capacity compressor, such as a 1 - 2 horsepower unit, may be sufficient. However, for larger, industrial - scale soda blasting operations, high - capacity compressors with multiple horsepower and large air - storage tanks are required. The compressor must be able to maintain a consistent air pressure to ensure uniform blasting. In an automotive refinishing shop, where soda blasting is used to remove paint from car bodies, a reliable compressor is crucial for achieving a smooth and even removal of the paint layer without causing any damage to the underlying metal.
2.3 Blasting Nozzle
The blasting nozzle is where the soda particles and compressed air meet and are directed towards the surface being treated. Nozzles are available in different shapes and sizes, each designed for specific applications. For general - purpose soda blasting, a standard conical - shaped nozzle is commonly used. However, for more precise work, such as cleaning small, detailed parts or removing paint from hard - to - reach areas, a smaller, more focused nozzle may be required. The material of the nozzle is also important. Nozzles are typically made of durable materials like tungsten carbide or ceramic, which can withstand the abrasive action of the soda particles over time. In a restoration project of antique machinery, a specialized nozzle with a narrow opening can be used to carefully clean the intricate gears and levers without causing any collateral damage.
2.4 Hoses and Tubing
Hoses and tubing connect the various components of the soda blasting machine, such as the hopper, compressor, and nozzle. The hoses must be able to withstand the pressure from the compressor and the abrasive nature of the soda particles. They are usually made of reinforced rubber or high - strength plastic materials. The length of the hoses can vary depending on the application. For example, in a large - scale industrial cleaning project where the soda blasting machine needs to reach different areas of a factory floor, long hoses may be required. However, for smaller, more localized jobs, shorter hoses can be used for better maneuverability. The hoses also need to be flexible enough to allow the operator to move freely while blasting, but not so flexible that they kink or restrict the flow of the soda - air mixture.
2.5 Control System
The control system of a soda blasting machine allows the operator to regulate the blasting process. It typically includes controls for adjusting the air pressure, the flow rate of the soda, and in some cases, the blasting pattern. Manual control systems are common in smaller, more basic soda blasting machines. These usually involve simple valves and knobs that the operator can adjust to change the blasting parameters. In more advanced, industrial - grade machines, digital control systems are used. These systems provide more precise control over the blasting process and may also offer features such as preset blasting programs for different applications. For example, in an aerospace manufacturing facility, where soda blasting is used to clean and prepare aircraft components, a digital control system can be programmed to deliver the exact amount of soda and air pressure required for each specific part.
3. Working Principle
The working principle of a soda blasting machine is based on the high - velocity impact of soda particles on the surface being treated.
1. Abrasive Feeding: The soda, stored in the hopper, is fed into the blasting system. The agitator or vibrator in the hopper, if present, ensures that the soda flows smoothly. Gravity or a mechanical feeding mechanism, such as a screw conveyor, moves the soda towards the mixing chamber.
2. Air Compression: The compressor compresses air, which is then directed towards the mixing chamber. The compressed air creates a high - pressure stream that will carry the soda particles.
3. Mixing and Propulsion: In the mixing chamber, the soda particles and the compressed air combine to form a high - velocity slurry. This slurry is then propelled through the hose and out of the blasting nozzle.
4. Surface Interaction: When the high - velocity soda - air mixture hits the surface, the soda particles act as tiny abrasives. The impact of the soda particles on the surface dislodges contaminants such as paint, rust, grease, or dirt. Sodium bicarbonate is a relatively soft abrasive, with a Mohs hardness of around 2.5 - 3. This means that it can effectively remove surface contaminants without causing significant damage to the underlying material, even if it is a soft metal like aluminum or a delicate composite material.
5. Clean - up and Recovery: After the blasting process, the used soda and the removed contaminants can be collected and disposed of or, in some cases, recycled. In industrial settings, a vacuum - based recovery system may be used to collect the used soda and debris, making the process more environmentally friendly and cost - effective.
4. Applications
4.1 Automotive Industry
In the automotive industry, soda blasting machines are widely used for paint removal and surface preparation. When a car is being repainted, soda blasting provides a gentle yet effective way to strip off the old paint. It can remove multiple layers of paint without damaging the metal body, unlike some traditional abrasive blasting methods that can cause pitting or scratching. Soda blasting is also used to clean engine components. The high - pressure soda - air mixture can reach into the nooks and crannies of the engine, removing grease, oil, and carbon deposits. This not only improves the appearance of the engine but also helps in maintaining its performance. In the restoration of classic cars, soda blasting is a preferred method as it can carefully remove the old paint and grime, revealing the original metal surface without causing any harm to the historical value of the vehicle.
4.2 Aerospace Industry
The aerospace industry has strict requirements for surface cleanliness and integrity. Soda blasting is used to clean and prepare aircraft components such as turbine blades, engine casings, and airframe parts. The gentle nature of soda blasting ensures that the delicate surfaces of these components are not damaged. For example, when removing thermal barrier coatings from turbine blades, soda blasting can precisely remove the coating without affecting the underlying superalloy material. Soda blasting is also used to clean the surface of aircraft parts before applying new coatings or adhesives. The clean and smooth surface provided by soda blasting improves the adhesion of the coatings and adhesives, enhancing the overall performance and safety of the aircraft.
4.3 Restoration and Conservation
Soda blasting is a valuable tool in the restoration and conservation of historical buildings, monuments, and artifacts. When restoring old stone buildings, soda blasting can remove layers of dirt, grime, and graffiti without eroding the stone surface. It is a non - invasive method that preserves the original texture and details of the stone. In the conservation of metal artifacts, such as antique cannons or sculptures, soda blasting can remove rust and corrosion without causing any harm to the metal. This allows for the preservation of the historical and cultural value of these artifacts. For example, in the restoration of a centuries - old cathedral, soda blasting can be used to clean the exterior stonework, bringing back its original beauty while maintaining its structural integrity.
4.4 Manufacturing and Fabrication
In manufacturing and fabrication processes, soda blasting is used for surface preparation before painting, plating, or powder coating. It provides a clean and roughened surface that enhances the adhesion of the coatings. Soda blasting is also used to clean molds in the manufacturing of plastic products. The soda particles can effectively remove the residue and release agents from the molds, ensuring a smooth production process. In the production of metal parts, soda blasting can be used to remove burrs and smooth the surface, improving the overall quality of the product. For example, in a furniture manufacturing plant, soda blasting can be used to prepare the metal frames before applying a decorative powder coating, resulting in a more durable and aesthetically pleasing finish.
5. Advantages
5.1 Gentle on Surfaces
One of the most significant advantages of soda blasting is its gentleness. The soft nature of sodium bicarbonate makes it suitable for use on a wide range of materials, including soft metals, plastics, composites, and delicate surfaces. It can remove contaminants without causing scratches, dents, or other forms of damage. This makes soda blasting an ideal choice for applications where surface integrity is crucial, such as in the restoration of historical artifacts or the cleaning of high - value components in the aerospace industry.
5.2 Environmentally Friendly
Soda blasting is a relatively environmentally friendly surface - treatment method. Sodium bicarbonate is a non - toxic, biodegradable substance. After the blasting process, the used soda and the removed contaminants can be easily collected and disposed of in an environmentally responsible manner. In some cases, the used soda can even be recycled. This is in contrast to some traditional abrasive blasting methods that use harsh chemicals or non - biodegradable abrasives, which can pose a threat to the environment.
5.3 Versatile Applications
Soda blasting machines can be used for a wide variety of applications, as seen in the automotive, aerospace, restoration, and manufacturing industries. Whether it's removing paint, rust, grease, or preparing a surface for coating, soda blasting provides an effective solution. The ability to adjust the blasting parameters, such as air pressure and soda flow rate, allows for customization based on the specific requirements of each application.
5.4 Cost - Effective in the Long Run
Although the initial investment in a soda blasting machine and its associated equipment may seem significant, it can be cost - effective in the long run. Soda is a relatively inexpensive abrasive material, and the fact that it can be recycled in some cases further reduces the operating costs. The gentle nature of soda blasting also reduces the risk of damage to the surface being treated, which can save on costly repairs or replacements. Additionally, the high - efficiency of soda blasting in removing contaminants can lead to shorter processing times, increasing productivity.
6. Challenges
6.1 Limited Abrasive Power for Some Applications
While soda blasting is gentle and effective for many applications, it may not have enough abrasive power for extremely tough or thick - layer contaminant removal. For example, removing thick, hardened industrial coatings or deeply - embedded rust on heavily corroded metal may require a more aggressive abrasive. In such cases, soda blasting may need to be combined with other methods or used as a pre - treatment step before a more abrasive blasting process.
6.2 Moisture Sensitivity
Sodium bicarbonate is sensitive to moisture. If the soda absorbs moisture, it can cake and clog the blasting system. This requires proper storage of the soda in a dry environment. In humid working conditions, additional measures may be needed to prevent moisture from affecting the soda. For example, using desiccants in the hopper or installing a moisture - removal system in the air supply line.
6.3 Dust Generation
During the soda blasting process, a significant amount of dust can be generated. This dust can be a health hazard if inhaled by the operator. Proper ventilation and personal protective equipment, such as respirators, are essential. In enclosed workspaces, dust - collection systems need to be installed to maintain a safe working environment. The dust can also be a nuisance in terms of clean - up, as it can spread to other areas of the workplace if not properly contained.
6.4 Operator Skill Requirement
Operating a soda blasting machine effectively requires a certain level of skill. The operator needs to be able to adjust the blasting parameters correctly to achieve the desired results. Incorrect settings can lead to either insufficient cleaning or damage to the surface. Training is essential to ensure that the operator can handle the machine safely and efficiently. In some cases, lack of proper training may result in sub - optimal performance and wasted resources.
7. Future Trends
7.1 Integration of Advanced Technologies
The future of soda blasting machines is likely to involve the integration of advanced technologies. For example, the use of sensors and automated control systems to optimize the blasting process. Sensors can monitor the surface condition, the amount of soda remaining in the hopper, and the air pressure. Based on this data, the control system can automatically adjust the blasting parameters to ensure consistent and efficient operation. In the future, soda blasting machines may also be integrated with robotic arms, allowing for precise and repeatable blasting in complex or dangerous environments.
7.2 Development of Specialized Soda Formulations
Research may lead to the development of specialized soda formulations for specific applications. These formulations could have enhanced abrasive properties, better moisture resistance, or improved cleaning capabilities. For example, a soda formulation designed specifically for removing a certain type of industrial adhesive or a formulation that is more effective in cleaning composite materials. This would further expand the range of applications for soda blasting machines.
7.3 Improved Dust - Control and Recycling Systems
As environmental concerns continue to grow, there will be a greater focus on improving dust - control and recycling systems for soda blasting. New dust - collection technologies may be developed to more effectively capture and contain the dust generated during the blasting process. Additionally, more efficient recycling methods for the used soda may be introduced, reducing waste and further enhancing the environmental friendliness of soda blasting.
In conclusion, soda blasting machines have carved a niche for themselves in the field of surface preparation and cleaning. Their unique combination of gentleness, versatility, and environmental friendliness makes them a valuable asset in numerous industries. While they face some challenges, ongoing technological advancements and research are likely to further enhance their performance and expand their applications in the future.