Hotline
+86-136 8495 9862
Email:cennia@szmizhi.com
Add::104,Building 27,Third Industrial Zone, Longxi Community,Longgang District,Shenzhen,China.
Coil Forming & Handling Equipment
Surface Treatment Equipment
Solutions
Application
About Us
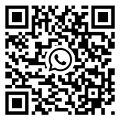
Welcome to MIZHI
For consultation/feedback, please call the service hotline: +86-136 8495 9862 Email:cennia@szmizhi.com
In the world of metal fabrication and manufacturing, the stainless steel coil slitting machine plays a crucial role in transforming large coils of stainless steel into narrower strips with precision and efficiency. This advanced piece of equipment is designed to handle the unique properties of stainless steel, offering a range of benefits that are essential for various industries.
The stainless steel coil slitting machine is a complex combination of mechanical, electrical, and hydraulic systems that work together to achieve accurate slitting of stainless steel coils. The machine typically consists of an unwind stand, a slitting section, and a rewind stand. The unwind stand holds the large coil of stainless steel and feeds it into the slitting section, where it is cut into narrower strips by a set of circular knives or blades. The rewind stand then takes the slit strips and winds them onto smaller coils for easy handling and storage.
One of the key features of the stainless steel coil slitting machine is its precision. The machine is designed to cut the stainless steel coil with extremely tight tolerances, ensuring that the resulting strips are of consistent width and thickness. This precision is achieved through the use of advanced cutting technology, such as high-speed circular knives or blades, and precise control systems that monitor and adjust the cutting process in real-time.
Another important aspect of the stainless steel coil slitting machine is its durability. Stainless steel is a tough and corrosion-resistant material, and the machine must be able to handle the stresses and strains of slitting it without breaking down or wearing out quickly. To achieve this durability, the machine is typically constructed from high-quality materials, such as hardened steel and durable alloys, and is designed with robust mechanical and electrical components that can withstand the rigors of continuous operation.
In addition to precision and durability, the stainless steel coil slitting machine also offers a high level of productivity. The machine is capable of processing large coils of stainless steel quickly and efficiently, reducing production time and increasing output. This productivity is achieved through the use of automated feeding and cutting systems, as well as advanced control systems that optimize the cutting process and minimize downtime.
The stainless steel coil slitting machine is used in a wide range of industries, including automotive, aerospace, construction, and appliance manufacturing. In the automotive industry, for example, the machine is used to slit stainless steel coils for use in exhaust systems, fuel tanks, and other components. In the aerospace industry, it is used to slit stainless steel coils for use in aircraft engines, landing gear, and other parts. In the construction industry, it is used to slit stainless steel coils for use in roofing, siding, and other applications. And in the appliance manufacturing industry, it is used to slit stainless steel coils for use in refrigerators, ovens, and other appliances.
When considering the purchase of a stainless steel coil slitting machine, there are several factors to consider. First, it is important to determine the specific needs of your business, including the types and sizes of stainless steel coils you will be processing, the required strip widths and thicknesses, and the production volume. This will help you choose a machine that is suitable for your application.
Second, you should consider the quality and reputation of the manufacturer. Look for a manufacturer with a proven track record of producing high-quality stainless steel coil slitting machines and providing excellent customer service and support.
Finally, you should consider the cost of the machine. While it is important to find a machine that meets your needs and budget, it is also important to remember that the cheapest option may not always be the best. Consider the long-term costs of ownership, including maintenance, repair, and replacement parts, when evaluating the cost of a stainless steel coil slitting machine.
In conclusion, the stainless steel coil slitting machine is an essential tool for metal fabrication and manufacturing. Its precision, durability, and productivity make it suitable for a wide range of applications, and its advanced features and capabilities ensure that it can handle the unique properties of stainless steel. Whether you are a small business or a large manufacturing operation, a stainless steel coil slitting machine can help you improve your production processes and increase your competitiveness in the market.
CR Slitting Machine
I. Introduction
CR slitting machines play a crucial role in the processing of cold - rolled (CR) materials. These machines are specifically designed to slit wide coils of cold - rolled steel, aluminum, or other similar materials into narrower strips with high precision. The development of CR slitting machines has been driven by the increasing demand for customized widths of cold - rolled materials in industries such as automotive, electronics, and construction.
II. Working Principle of CR Slitting Machines
1. Unwinding System
The process begins with the unwinding of the CR coil. The unwinding system of a CR slitting machine is carefully designed to handle the weight and size of the coil. It usually consists of a mandrel onto which the coil is mounted. The mandrel is equipped with a drive mechanism that allows for controlled rotation. As the coil unwinds, sensors are used to monitor the tension in the material. Maintaining the correct tension is vital as it affects the quality of the slitting process. If the tension is too high, it can cause the material to stretch or even break. On the other hand, if the tension is too low, it may lead to wrinkling or misalignment during slitting.
2. Guiding and Feeding
Once the material starts to unwind, it is guided through a series of rollers. These rollers are precisely aligned to ensure that the material moves in a straight line towards the slitting section. The rollers are made of materials with low friction coefficients to minimize any resistance to the material's movement. Some advanced CR slitting machines have automatic guiding systems that can detect and correct any lateral displacement of the material. The feeding speed of the material is carefully controlled to match the slitting speed of the machine. This synchronization is crucial for achieving accurate and consistent slitting results.
3. Slitting Mechanism
The slitting mechanism in a CR slitting machine can vary depending on the design. One common type is the roll - slitting method. In this approach, circular knives are mounted on shafts. The number of knives and their positions can be adjusted according to the desired widths of the slit strips. The knives are made of high - quality tool steel or carbide to ensure sharpness and durability. As the material passes between the rotating knives and the backup rollers, it is cut into the specified widths. Another type of slitting mechanism is the shear - slitting method. Shear - slitting uses straight blades that move vertically or horizontally to cut the material. This method is often preferred for thicker CR materials or when a more precise cut is required. The blades are actuated by hydraulic or mechanical systems with high force to penetrate the cold - rolled material cleanly.
4. Edge Trimming and Scrap Removal
During the slitting process, the edges of the material may need to be trimmed to remove any burrs or irregularities. Special edge - trimming devices are incorporated into the CR slitting machine. These devices can be adjusted to accommodate different strip widths. The trimmed edges and any scrap material generated during the slitting process are efficiently removed from the machine. This is important not only for maintaining the quality of the slit strips but also for the proper functioning of the machine. Scrap that accumulates within the machine can interfere with the slitting operation and cause damage to the cutting tools or other components.
5. Tension Control and Rewinding or Stacking
After slitting, the tension of the cut strips needs to be carefully controlled again. This is to ensure that the strips are wound onto the take - up reels smoothly or stacked neatly if they are not rewound. In the case of rewinding, the take - up reels are designed to hold the slit strips in a tight and organized manner. The rewinding speed is synchronized with the slitting and feeding speeds to prevent any slack or excessive tension in the strips. If the strips are to be stacked, special stacking mechanisms are used to ensure that they are placed in an orderly fashion for further processing or packaging.
III. Key Components of CR Slitting Machines
1. Unwinding Mandrel and Coil Handling Equipment
The unwinding mandrel is a key component for handling the CR coil. It is usually made of high - strength steel to support the weight of the coil. The mandrel has a design that allows for easy loading and unloading of the coil. Some mandrels have expandable features to securely hold the coil during the unwinding process. Coil handling equipment may also include cranes or forklifts for moving the coils to and from the machine. Additionally, there are safety features associated with the coil handling process to prevent accidents during loading and unloading.
2. Roller System for Guiding and Feeding
The roller system consists of multiple rollers that are strategically placed along the path of the material. These rollers have different functions. Some are used for guiding the material, ensuring that it moves in the correct direction. Others are responsible for applying the necessary tension to the material. The rollers are usually made of hardened steel or have special coatings to reduce friction. The diameter, length, and surface finish of the rollers are carefully selected based on the type and thickness of the CR material being processed. The roller system may also include tension - measuring sensors that provide feedback to the control system for adjusting the tension as needed.
3. Cutting Unit (Knives or Blades)
The cutting unit is the heart of the CR slitting machine. In roll - slitting machines, the circular knives are carefully designed and manufactured. They have a specific cutting edge geometry to ensure clean cuts. The knives are mounted on shafts that are driven by motors. The shaft - mounting system allows for precise adjustment of the knife positions. In shear - slitting machines, the straight blades are made of high - quality tool steel. The blades are attached to a hydraulic or mechanical actuating system that provides the necessary force for cutting. The cutting unit also includes backup rollers or anvils that support the material during the cutting process.
4. Edge - trimming and Scrap Handling Devices
Edge - trimming devices are usually adjustable cutting tools that are positioned at the edges of the slit material. They can be either rotary cutters or stationary blades. These devices are designed to remove any burrs or rough edges from the slit strips. Scrap handling devices include conveyors, chutes, or bins that collect and transport the trimmed edges and other scrap material away from the slitting area. The design of these devices ensures that the scrap is removed efficiently without interfering with the normal operation of the machine.
5. Tension Control and Rewinding/Stacking System
The tension control system consists of tension rollers, load cells, and control valves. Tension rollers are used to apply and adjust the tension in the material. Load cells measure the tension force, and control valves regulate the movement of the rollers to maintain the desired tension level. The rewinding system, if applicable, includes take - up reels with motors and braking mechanisms. The motors drive the reels to wind the slit strips, and the braking mechanisms control the speed and tension during the rewinding process. In the case of stacking systems, they have mechanisms for accurately placing the cut strips in a stack.
IV. Advantages of CR Slitting Machines
1. High - precision Slitting
CR slitting machines are designed to provide extremely high - precision slitting of cold - rolled materials. The combination of advanced guiding systems, precise cutting mechanisms, and accurate tension control ensures that the slit strips have consistent widths and minimal burrs. This precision is crucial in industries where the dimensions of the material directly affect the quality of the final product. For example, in the production of automotive parts, precise slitting of cold - rolled steel is required for manufacturing components such as seat frames, body panels, and engine parts. The accurate widths of the slit strips ensure proper fit and assembly of these components.
2. Increased Productivity
These machines can significantly increase productivity in the processing of CR materials. The automated unwinding, feeding, slitting, and rewinding or stacking processes reduce the need for manual intervention. The high - speed operation of CR slitting machines allows for large quantities of material to be processed in a relatively short time. For instance, in a steel processing plant, a CR slitting machine can slit multiple coils of cold - rolled steel in a day, providing the necessary strips for various manufacturing applications. This increased productivity helps to meet the high - volume demands of industries that rely on cold - rolled materials.
3. Versatility in Material Processing
CR slitting machines are highly versatile and can handle a wide variety of cold - rolled materials. They can process different grades of cold - rolled steel, including those with different alloy compositions. Additionally, they can also handle cold - rolled aluminum and other similar materials. The ability to adjust the slitting parameters, such as the number of knives, cutting speed, and tension control, allows these machines to adapt to different material thicknesses and properties. This versatility makes them suitable for a diverse range of manufacturing applications across multiple industries.
4. Improved Quality Control
The integrated control systems in CR slitting machines contribute to better quality control. The sensors and monitoring devices within the machine can detect any variations in tension, material alignment, or cutting quality. If an issue is detected, the control system can make adjustments in real - time to correct the problem. For example, if the tension in the material becomes too high or too low, the tension control system can automatically adjust the tension rollers. This continuous monitoring and control of the slitting process ensure that the quality of the slit strips meets the required standards, reducing the number of defective products in subsequent manufacturing processes.
V. Challenges and Solutions in the Operation of CR Slitting Machines
1. Cutting Tool Wear
One of the main challenges in operating CR slitting machines is the wear of cutting tools. The continuous cutting of cold - rolled materials, especially those with high hardness, can cause the knives or blades to dull over time. Dull cutting tools can lead to poor cut quality, such as rough edges, burrs, or inaccurate cut widths. To address this issue, high - quality cutting tools made from advanced materials such as carbide - enhanced steels are used. Regular inspection of the cutting tools is essential. The tools should be sharpened or replaced when they show signs of wear. Some CR slitting machines also have built - in tool - changing mechanisms to facilitate quick and easy replacement of worn - out tools.
2. Material Deformation
Cold - rolled materials can be prone to deformation during the slitting process. Factors such as improper tension control, misalignment of the rollers, or excessive cutting force can cause the material to stretch, wrinkle, or distort. To prevent material deformation, the tension control system needs to be highly accurate and responsive. The roller system should be properly aligned and maintained to ensure smooth material movement. Additionally, the cutting force and speed should be carefully adjusted based on the type and thickness of the material. Advanced CR slitting machines use sensors to monitor the material's condition during slitting and make real - time adjustments to prevent deformation.
3. Energy Consumption
CR slitting machines, especially those with high - power motors for driving the unwinding, slitting, and rewinding operations, can consume a significant amount of energy. To manage energy consumption, manufacturers are incorporating energy - efficient components into the machine design. This includes using motors with high - efficiency ratings, optimizing the control systems to reduce unnecessary power usage, and implementing power - saving modes during idle periods. Additionally, proper maintenance of the machine, such as keeping the rollers and moving parts well - lubricated, can also reduce energy consumption by improving the overall efficiency of the machine's operation.
4. Safety Concerns
CR slitting machines involve several safety hazards due to the presence of moving parts, sharp cutting tools, and high - tension materials. To ensure the safety of operators, these machines are equipped with various safety features. These include emergency stop buttons, safety guards around the cutting area, and interlocks that prevent the machine from starting or operating when safety conditions are not met. Operators should also be trained in proper safety procedures, such as wearing appropriate personal protective equipment and understanding how to operate the machine safely. Regular safety inspections of the machine are necessary to identify and address any potential safety issues.
VI. Conclusion
CR slitting machines are essential equipment in the processing of cold - rolled materials. Their unique working principle, key components, advantages, and the challenges associated with their operation all contribute to the complex landscape of modern manufacturing. With continuous technological advancements, these machines are expected to become even more efficient, precise, and safe, further enhancing the productivity and quality of the processing of cold - rolled materials for various industries. By addressing the challenges through proper design, maintenance, and operation, CR slitting machines will continue to play a vital role in meeting the demands of the manufacturing sector.