Hotline
+86-136 8495 9862
Email:cennia@szmizhi.com
Add::104,Building 27,Third Industrial Zone, Longxi Community,Longgang District,Shenzhen,China.
Coil Forming & Handling Equipment
Surface Treatment Equipment
Solutions
Application
About Us
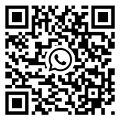
Welcome to MIZHI
For consultation/feedback, please call the service hotline: +86-136 8495 9862 Email:cennia@szmizhi.com
Standing seam panel machines are a crucial part of the roofing and cladding industry. These machines are specifically designed to manufacture standing seam panels, which are known for their durability, weather resistance, and aesthetic appeal.
The standing seam panel machine operates by continuously forming a flat metal sheet into a standing seam profile. The process begins with the loading of the metal coil onto the machine. The coil is unwound and fed into the forming section. This forming section consists of a series of rollers that gradually bend and shape the metal sheet. The rollers are precisely engineered to create the characteristic standing seam profile with its raised seams and flat panels in between.
One of the main advantages of using a standing seam panel machine is the flexibility it offers in terms of panel length. Since the panels are formed continuously, they can be produced in custom lengths according to the specific requirements of the roofing or cladding project. This eliminates the need for on - site cutting and reduces waste. The ability to produce long panels also provides a seamless and continuous appearance, enhancing the aesthetic quality of the finished roof or cladding.
The metal used in the standing seam panel machine can vary. Commonly used metals include steel, aluminum, and zinc. Each metal has its own unique properties. Steel is known for its strength and durability, making it suitable for applications where the roof or cladding needs to withstand heavy loads or harsh environmental conditions. Aluminum is lightweight and corrosion - resistant, which is ideal for coastal areas or areas with high humidity. Zinc has a natural patina that gives it a unique and attractive appearance over time.
The machine's control system plays a vital role in ensuring the quality and consistency of the standing seam panels. Modern standing seam panel machines are often equipped with computer - controlled systems that allow for precise adjustment of the forming process. This includes controlling the speed at which the metal is fed through the rollers, the pressure applied by the rollers, and the overall shape and dimensions of the panels. The control system can also store different profiles and settings, making it easy to switch between different panel designs.
Another important aspect of the standing seam panel machine is its ability to incorporate additional features. For example, some machines are capable of adding perforations or embossments to the panels. Perforations can be used for ventilation or aesthetic purposes, while embossments can add texture and visual interest. These additional features can enhance the functionality and design of the standing seam panels.
The production capacity of the standing seam panel machine is an important consideration. High - volume production facilities may require machines with a high output rate to meet the demand for panels. Some machines are designed for industrial - scale production, capable of producing large quantities of panels in a short period of time. On the other hand, smaller, portable standing seam panel machines are available for on - site production or for smaller projects.
During the manufacturing process, quality control is essential. This includes monitoring the thickness of the metal, the integrity of the seams, and the overall flatness of the panels. Any defects or deviations from the specified standards can affect the performance and appearance of the roofing or cladding. Regular inspection and maintenance of the machine are necessary to ensure its optimal operation and to produce high - quality panels.
In terms of installation, standing seam panels produced by the machine are typically installed using a clip - based system. This allows for thermal movement of the panels without causing damage or distortion. The clips are attached to the underlying structure, and the panels are then snapped onto the clips. This installation method provides a secure and weather - tight seal.
In conclusion, the standing seam panel machine is a key component in the production of standing seam panels. Its ability to form high - quality panels with custom lengths and additional features has made it an essential tool in the roofing and cladding industry. By ensuring the efficient and accurate production of these panels, the machine contributes to the durability, aesthetic appeal, and overall performance of roofing and cladding systems.