Hotline
+86-136 8495 9862
Email:cennia@szmizhi.com
Add::104,Building 27,Third Industrial Zone, Longxi Community,Longgang District,Shenzhen,China.
Coil Forming & Handling Equipment
Surface Treatment Equipment
Solutions
Application
About Us
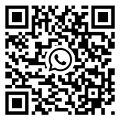
Welcome to MIZHI
For consultation/feedback, please call the service hotline: +86-136 8495 9862 Email:cennia@szmizhi.com
1. Introduction
Steel coil slitting is a crucial operation in the metalworking industry, serving as a bridge between the raw material supply and the diverse manufacturing needs of various sectors. It involves the precise cutting of large steel coils into narrower strips, tailored to the specific requirements of downstream applications. This process is not only about dividing the material but also about ensuring high - quality, consistent results that meet the exacting standards of industries such as automotive, construction, electronics, and packaging. The ability to transform a single large - scale steel coil into multiple, precisely sized strips is a cornerstone of modern manufacturing, enabling efficient production, waste reduction, and customization.
2. The Process of Steel Coil Slitting
2.1. Uncoiling
The first step in steel coil slitting is uncoiling. The large steel coil, which can weigh several tons and have a diameter of up to several meters, is loaded onto an uncoiler. There are different types of uncoilers, including fixed - type and movable - type. Fixed uncoilers are suitable for operations where the coil size and weight are relatively consistent. They are cost - effective and easy to maintain. Movable uncoilers, on the other hand, offer greater flexibility. They can be adjusted to accommodate coils of different diameters and weights, making them ideal for facilities that deal with a wide variety of coil sizes.
Once the coil is loaded, the uncoiler begins to unwind the steel strip at a controlled speed. This speed is carefully regulated to ensure a smooth and consistent feed into the subsequent processing stages. Advanced uncoilers are equipped with automatic tension control systems. These systems are essential for maintaining the integrity of the steel strip during unwinding. If the tension is too high, the steel may stretch or even break, while too low a tension can cause the strip to sag, leading to inaccuracies in the slitting process. The tension control system uses sensors to measure the tension in real - time and adjusts the speed of the uncoiler accordingly.
2.2. Straightening and Leveling
Before the steel strip can be slit, it often needs to be straightened and leveled. Steel coils, during the manufacturing and transportation processes, may acquire some curvature, bow, or waviness. These imperfections can affect the accuracy of the slitting process and the quality of the final slit strips. The straightening and leveling process is designed to eliminate these irregularities.
The straightening and leveling unit typically consists of a series of rollers. As the steel strip passes through these rollers, the rollers apply pressure to the strip, gradually straightening and flattening it. The number of rollers and their configuration depend on the thickness and type of steel being processed. For example, thicker steels may require fewer but larger - diameter rollers, while thinner steels may need more rollers with smaller diameters to achieve the desired flatness. Some advanced straightening and leveling units are equipped with sensors that can detect any remaining imperfections in the strip and make real - time adjustments to the roller pressure. This ensures that the steel strip is in an optimal condition for slitting, resulting in higher - quality slit products.
2.3. Slitting
The slitting process is the core of the steel coil slitting operation. It involves using a set of cutting blades to divide the wide steel strip into narrower strips of the desired width. The cutting blades are usually circular and are made of high - quality materials such as hardened steel or carbide. These materials are chosen for their ability to withstand the high - stress cutting process and maintain their sharpness over an extended period.
There are two main types of slitting methods: shear slitting and score slitting. In shear slitting, two sets of blades work together to shear the steel strip as it passes through. The upper blade and the lower blade are offset slightly, creating a shearing action that cleanly cuts the material. This method is suitable for a wide range of steel grades and thicknesses. Score slitting, on the other hand, uses a single blade to score the surface of the steel strip. The strip is then broken along the scored line, either by the tension in the strip or by a separate breaking mechanism. Score slitting is often used for more brittle materials or when a particular edge finish is required.
The slitting head, which houses the cutting blades, is designed to be highly precise. The distance between the blades can be adjusted to achieve different strip widths. In modern slitting machines, this adjustment can be done manually or, more commonly, through an automated system. The automated systems use motorized actuators to move the blades to the desired positions accurately. This allows for quick and easy changes in strip width, enabling manufacturers to respond rapidly to different customer requirements.
2.4. Recoiling
After the steel strip has been slit into the desired widths, the next step is recoiling. The recoiler winds each of the slit strips into smaller coils. The recoiling process is just as important as the previous steps, as it determines the quality of the final product in terms of how the slit strips are wound and packaged.
The recoiler has a variable - speed motor that can adjust the winding speed according to the speed of the slitting process. This ensures that the tension in the slit strips is maintained during the winding process. If the tension is not properly controlled, the coils may be wound unevenly, which can lead to problems during subsequent handling and processing. The recoiler also has a mechanism to control the diameter of the wound coils. Different applications may require coils of specific diameters, and the recoiler can be adjusted to meet these requirements.
Some advanced recoilers are equipped with an automatic coil - transfer system. Once a coil is fully wound, the system automatically transfers the coil to a pallet or another storage area. This allows the recoiler to start winding the next coil without interruption, significantly increasing the productivity of the slitting line.
3. Types of Steel Coils Suitable for Slitting
3.1. Carbon Steel Coils
Carbon steel coils are one of the most commonly slit materials. They are widely used in various industries due to their relatively low cost, good mechanical properties, and versatility. Low - carbon steel coils, with a carbon content typically less than 0.3%, are known for their excellent formability. They are often slit into strips for applications such as automotive body panels, where the ability to be easily shaped through processes like stamping is crucial.
Medium - carbon steel coils, with a carbon content ranging from 0.3% to 0.6%, offer a good balance between strength and formability. They are used in applications that require higher strength, such as in the construction of machinery parts and some structural components. High - carbon steel coils, with a carbon content above 0.6%, are very strong and are often slit for applications like springs and cutting tools, where high strength and hardness are essential.
3.2. Stainless Steel Coils
Stainless steel coils are highly sought - after for their corrosion - resistance properties. Austenitic stainless steel coils, which contain a significant amount of nickel and chromium, are the most common type. They are widely slit for applications in the food and beverage industry, where the corrosion - resistance of the steel is crucial to prevent contamination of the products. In the medical industry, austenitic stainless steel slit strips are used to manufacture surgical instruments and implantable devices.
Ferritic stainless steel coils, which have a lower nickel content and are mainly composed of iron and chromium, are also slit for applications where corrosion - resistance and formability are required, but at a lower cost compared to austenitic stainless steel. Martensitic stainless steel coils, known for their high strength and hardness after heat - treatment, are slit for applications such as knives and turbine blades.
3.3. Galvanized Steel Coils
Galvanized steel coils have a zinc coating on the surface, which provides excellent corrosion - protection. Hot - dipped galvanized steel coils, where the steel is immersed in a bath of molten zinc, are commonly slit for applications in the construction industry, such as roofing and wall cladding. The zinc coating not only protects the steel from rust but also gives the final product an attractive appearance.
Electro - galvanized steel coils, which are coated with zinc through an electrochemical process, are often slit for applications in the automotive industry, such as in the production of interior parts. The smooth and uniform coating of electro - galvanized steel makes it suitable for applications where a high - quality finish is required.
3.4. Aluminum - Coated Steel Coils
Aluminum - coated steel coils combine the strength of steel with the corrosion - resistance and heat - reflectivity of aluminum. These coils are often slit for applications in the automotive exhaust system, where the ability to withstand high temperatures and resist corrosion is essential. The aluminum coating also helps to reduce the weight of the components, which is beneficial for improving fuel efficiency in vehicles. In the building industry, aluminum - coated steel slit strips are used for applications such as heating, ventilation, and air - conditioning (HVAC) ducts, as they offer good corrosion - resistance and thermal performance.
4. Applications of Steel Coil Slitting
4.1. Automotive Industry
In the automotive industry, steel coil slitting plays a vital role in the production of various components. The high - precision slitting of steel strips is essential for manufacturing car body panels. Door panels, hoods, and fenders are all made from precisely slit steel strips. The accuracy of the slitting process ensures that these panels fit together perfectly during the assembly process, which is crucial for the structural integrity and aesthetic appearance of the vehicle.
Steel coil slitting is also used to produce strips for automotive interior components. Seat frames, for example, are made from slit steel strips that are further formed and welded. The strength and quality of the slit strips are essential for ensuring the safety and comfort of vehicle occupants. In addition, the automotive industry uses slit steel strips for the production of various mechanical components, such as gears and shafts. The ability to obtain strips of specific widths and qualities through slitting allows for efficient manufacturing and customization of these components.
4.2. Construction Industry
The construction industry is a major beneficiary of steel coil slitting. In roofing applications, slit steel strips are used to create long, continuous roofing sheets. The precision of the slitting process ensures that these sheets fit together tightly, providing a watertight and durable roofing solution. For wall cladding, slit steel strips are formed into panels that are used to cover the exterior of buildings. The consistent width and quality of the slit strips result in a uniform and attractive appearance for the building.
In the construction of structural components, such as steel beams and columns, steel coil slitting is used to produce the raw materials. The slitting process allows for the customization of the strip widths and thicknesses, which are tailored to the specific requirements of the construction project. Whether it's a small - scale residential building or a large - scale commercial structure, the use of slit steel strips in construction ensures the strength and stability of the building.
4.3. Electronics Industry
In the electronics industry, steel coil slitting is used to produce components for electronic devices. For example, steel strips are slit for the manufacturing of electronic enclosures, such as those for computers, smartphones, and tablets. The precise slitting of the steel strips ensures a proper fit for the components inside the enclosure and provides protection against external factors.
Steel coil slitting is also crucial for the production of electrical connectors and circuit boards. The narrow and accurately slit steel strips are used to create the conductive paths and contact points in these components. In the electronics industry, even the slightest deviation in the width or quality of the slit strips can affect the performance of the final product. Therefore, the high - precision slitting process is essential for meeting the strict quality requirements of the electronics manufacturing sector.
4.4. Packaging Industry
The packaging industry relies on steel coil slitting for the production of various packaging materials. Steel strips are slit for the manufacturing of cans, which are used to package food, beverages, and other products. The precision of the slitting process ensures that the cans are of consistent quality and can be easily formed and sealed.
In addition, slit steel strips are used to produce metal lids and closures for containers. The accurate width and flatness of the slit strips are important for ensuring a proper fit and seal. The packaging industry also uses slit steel strips for the production of decorative elements on packaging, such as embossed patterns on metal boxes. The ability to slit steel coils into narrow and precise strips allows for the creation of intricate and attractive packaging designs.
5. Equipment and Technology in Steel Coil Slitting
5.1. Slitting Machines
Modern slitting machines are highly sophisticated pieces of equipment. They are designed to handle a wide range of steel coil sizes, weights, and types. The slitting head, as mentioned earlier, is the core component of the slitting machine. It is equipped with advanced features such as automatic blade adjustment systems. These systems can quickly and accurately adjust the distance between the cutting blades to achieve the desired strip widths.
The drive systems in slitting machines are powerful and efficient. They are capable of providing the necessary torque to drive the uncoiler, slitting head, and recoiler at high speeds. The speed of the slitting process can be adjusted according to the thickness and type of steel being processed. For example, thinner steels can be slit at higher speeds, while thicker steels may require a slower speed to ensure a clean and accurate cut.
Some slitting machines are also equipped with advanced monitoring and control systems. These systems use sensors to monitor various parameters during the slitting process, such as the tension in the steel strip, the speed of the machine, and the temperature of the cutting blades. If any of these parameters deviate from the set values, the control system can automatically adjust the operation of the machine to ensure a smooth and consistent slitting process.
5.2. Blade Technology
The cutting blades used in steel coil slitting are a critical aspect of the technology. As mentioned, the blades are typically made of hardened steel or carbide. Carbide blades, in particular, offer excellent wear - resistance and can maintain their sharpness for a long time. This is especially important when slitting hard or abrasive steels.
The design of the blades also plays a crucial role in the slitting process. The shape of the blade edge, the angle of the cut, and the clearance between the blades are all carefully engineered to ensure a clean and efficient cut. Some blades are designed with special coatings to reduce friction and improve the cutting performance. In addition, the blades need to be regularly maintained and sharpened to ensure optimal cutting quality. Advanced blade - sharpening techniques are used to restore the sharpness of the blades and extend their lifespan.
5.3. Automation and Control Systems
Automation and control systems have revolutionized the steel coil slitting process. Programmable logic controllers (PLCs) are widely used to control the operation of the slitting machine. The operator can input the desired parameters, such as the strip width, the coil weight, and the type of steel, into the PLC. The PLC then controls the various components of the slitting machine, including the uncoiler, slitting head, and recoiler, to ensure that the slitting process is carried out accurately and efficiently.
Automation also extends to the material handling aspects of the slitting process. Automatic coil - loading and unloading systems are used to reduce the labor required and improve the safety of the operation. These systems can quickly and precisely position the steel coils on the uncoiler and remove the wound coils from the recoiler. In addition, some slitting lines are integrated with quality control systems that use sensors and cameras to detect any defects in the slit strips. If a defect is detected, the system can automatically stop the machine and alert the operator.
6. Quality Control in Steel Coil Slitting
6.1. Width and Thickness Tolerances
One of the primary aspects of quality control in steel coil slitting is ensuring that the slit strips meet the specified width and thickness tolerances. The width tolerance is crucial as it affects the fit and functionality of the final product. In industries such as automotive and electronics, where precision is of utmost importance, the width tolerance of the slit strips can be as tight as ±0.1 mm.
To maintain these tolerances, the slitting machine is equipped with highly accurate measurement systems. These systems use sensors to measure the width of the slit strips in real - time. If the width deviates from the set value, the control system can automatically adjust the position of the cutting blades to correct the width. The thickness tolerance is also closely monitored. The thickness of the steel strip can affect its strength and other mechanical properties. Thickness gauges are used to measure the thickness of the strip before and after slitting. If the thickness is not within the specified tolerance, the process parameters, such as the tension in the strip or the cutting force, can be adjusted.
6.2. Edge Quality
The edge quality of the slit strips is another critical factor in quality control. The edges should be clean, free from burrs, and have a smooth finish. Burrs, which are small protrusions on the edge of the strip, can be a significant problem as they can cause damage to other components during subsequent processing or use. In the automotive industry, for example, burrs on the edges of body panels can affect the painting process and the overall appearance of the vehicle.
To ensure good edge quality, the cutting blades need to be sharp and properly maintained. The cutting process parameters, such as the cutting speed, the cutting force, and the clearance between the blades, are carefully optimized. In addition, some slitting machines are equipped with deburring systems that can remove any burrs that may be present on the edges of the slit strips. These systems can use mechanical, chemical, or electrochemical methods to achieve a smooth and burr - free edge.
6.3. Surface Finish
The surface finish of the slit strips is also important, especially in applications where the appearance of the final product is crucial. In the construction industry, for example, the surface finish of the steel strips used for wall cladding and roofing can affect the aesthetic appearance of the building. In the electronics industry, the surface finish of the steel strips used for enclosures and components can affect the performance of the device, as a rough surface can cause electrical interference.
To achieve a good surface finish, the steel coil should be in good condition before slitting. Any surface defects on the coil, such as scratches or dents, can be magnified during the slitting process. The slitting machine should also be properly maintained to ensure that the rollers and other components that come in contact with the steel strip do not cause any additional surface damage. In some cases, post - slitting surface treatment processes, such as polishing or coating, may be used to improve the surface finish of the slit strips.
7. Future Trends in Steel Coil Slitting
7.1. Advanced Materials and Their Processing
As new and advanced steel alloys are developed, the steel coil slitting industry will need to adapt to process these materials. For example, high - strength low - alloy (HSLA) steels with enhanced mechanical properties are becoming increasingly popular in various industries. These steels may require different cutting parameters and blade technologies to ensure a clean and accurate cut. In addition, the development of new coating technologies