Hotline
+86-136 8495 9862
Email:cennia@szmizhi.com
Add::104,Building 27,Third Industrial Zone, Longxi Community,Longgang District,Shenzhen,China.
Coil Forming & Handling Equipment
Surface Treatment Equipment
Solutions
Application
About Us
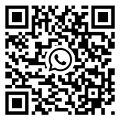
Welcome to MIZHI
For consultation/feedback, please call the service hotline: +86-136 8495 9862 Email:cennia@szmizhi.com
I. Introduction
The steel coil slitting machine is a fundamental piece of equipment in the steel processing industry. It is designed to take large steel coils and slit them into narrower coils or strips, which are more suitable for a wide range of applications in various industries such as construction, automotive, and manufacturing. This machine plays a crucial role in optimizing the use of steel coils by transforming them into customized widths according to specific requirements.
II. Working Principles of Steel Coil Slitting Machines
1. Uncoiling Process
- The first step in the operation of a steel coil slitting machine is the uncoiling of the large steel coil. The uncoiling unit is equipped with a mandrel on which the steel coil is mounted. This mandrel must be strong enough to support the substantial weight of the steel coil. The uncoiling process is carefully controlled to ensure a smooth and continuous feed of the steel into the slitting section. There are braking mechanisms associated with the uncoiling system. These brakes are essential for preventing the coil from unwinding too quickly or uncontrollably. If the coil unwinds too rapidly, it can lead to issues such as excessive slack in the steel, which can cause problems during the slitting process. Additionally, proper tension control is crucial during uncoiling. Tension control devices, such as load cells or tension rollers, are used to maintain a consistent tension in the steel as it is being unwound. This is important because inconsistent tension can result in the steel stretching or wrinkling, which will ultimately affect the quality of the slit product.
2. Slitting Mechanisms
- The slitting section of the machine is where the actual cutting of the steel coil into narrower strips occurs. There are different types of slitting mechanisms used in steel coil slitting machines. One common method is rotary slitting. In rotary slitting, circular blades are used to cut through the steel. These blades are typically mounted on shafts and rotate at a high speed. The rotary slitting mechanism is well - suited for slitting relatively thin steel coils. For thicker steel coils, shear slitting may be a more appropriate method. Shear slitting involves the use of two blades that move in a shearing motion relative to each other to cut the steel. The slitting blades need to be of high quality and sharpness to ensure clean and accurate cuts. The alignment of the blades is also critical. Any misalignment can lead to uneven slitting, resulting in strips with varying widths or rough edges. Some advanced steel coil slitting machines use laser - guided alignment systems to ensure precise blade alignment.
3. Recoiling of the Slit Strips
- After the steel coil has been slit into narrower strips, the next step is the recoiling of these strips. The recoiling system is designed to wind the slit steel strips back into coils. The recoiling mandrel is an important component of this system. It must be able to hold the slit strips firmly and wind them into neat and tight coils. Tension control during recoiling is just as important as during uncoiling. If the tension is not properly maintained, the resulting coil may be loose or have an inconsistent winding density. Edge - guiding devices are often used in the recoiling system to keep the slit strips centered during the recoiling process. This helps to ensure that the coils are wound evenly across their width.
III. Components of a Steel Coil Slitting Machine
1. Mandrel
- The mandrel is a key component in both the uncoiling and recoiling systems. In the uncoiling system, it serves as the support for the large steel coil. It needs to be made of a strong material, such as high - strength steel, to withstand the weight of the coil. The mandrel may also have features to facilitate easy mounting and removal of the coil. In the recoiling system, the mandrel is responsible for winding the slit steel strips into coils. It should have a smooth surface to prevent damage to the steel strips during the recoiling process.
2. Blades and Blade Holders
- The slitting blades are the most critical components in the slitting section. They are typically made of high - quality tool steel or carbide - tipped materials to ensure durability and sharpness. The blade holders are designed to hold the blades firmly in place and allow for precise adjustment of their position. The blade holders need to be machined to high tolerances to ensure accurate blade alignment. In addition, they should be able to withstand the forces generated during the slitting process without any deformation.
3. Guide Rollers
- Guide rollers are used throughout the steel coil slitting machine to guide the steel coil and the slit strips. These rollers are made of high - quality materials with a smooth surface finish to minimize friction. They play an important role in maintaining the proper alignment of the steel during the uncoiling, slitting, and recoiling processes. In the slitting section, the guide rollers help to ensure that the steel is fed straight into the slitting blades, which is crucial for accurate slitting.
4. Tension Control Devices
- As mentioned earlier, tension control is vital in a steel coil slitting machine. Tension control devices include load cells, tension rollers, and associated control systems. Load cells are used to measure the tension in the steel, and the data is fed back to the control system. Based on this feedback, the control system can adjust the speed of the uncoiling or recoiling motors to maintain the desired tension. Tension rollers are designed to apply a consistent force to the steel to keep it under the correct tension.
IV. Control Systems in Steel Coil Slitting Machines
1. Programmable Logic Controllers (PLCs)
- Programmable Logic Controllers (PLCs) are widely used in steel coil slitting machines to control various aspects of the machine's operation. PLCs can be programmed to manage the uncoiling speed, slitting speed, and recoiling speed. For example, they can adjust the uncoiling speed based on the diameter of the coil being unwound. As the coil diameter decreases, the uncoiling speed may need to be adjusted to maintain a constant feed rate to the slitting section. In the slitting section, PLCs can control the rotation speed of the slitting blades and the cutting force. In the recoiling system, PLCs can regulate the tension and the winding speed. PLCs also play an important role in safety - related functions, such as emergency stop procedures and interlocking between different components to prevent accidental operation.
2. Human - Machine Interfaces (HMIs)
- Human - Machine Interfaces (HMIs) provide an interface between the operators and the steel coil slitting machine. Through the HMI, operators can set parameters such as the desired slitting widths, the production speed, and the number of coils to be produced. The HMI also displays real - time information about the status of the slitting machine, including the current uncoiling speed, slitting speed, and recoiling speed. It can also show the status of each component, such as whether a blade needs to be replaced or if there is a problem with the tension control. Modern HMIs are often touch - screen based, making it easy for operators to interact with the machine and monitor its performance.
3. Sensor - based Feedback Control
- Sensor - based feedback control is essential for the accurate operation of steel coil slitting machines. There are various types of sensors used in these machines. Photoelectric sensors are used to detect the presence and position of the steel. For example, they can be used to ensure that the steel is properly aligned during the slitting process. Load cells, as mentioned before, are used to measure the tension in the steel. The data from these sensors is fed back to the control system (usually the PLC). Based on this feedback, the control system can make real - time adjustments to optimize the operation of the slitting machine.
V. Applications of Steel Coil Slitting Machines in Different Industries
1. Construction Industry
- In the construction industry, steel coil slitting machines are used to produce steel strips for various applications. For example, they are used to slit steel coils for roofing materials. The slit steel strips can be formed into roofing sheets of the desired width, which are then installed on buildings. Steel coil slitting machines are also used to produce steel strips for siding materials. These strips provide a durable and aesthetically pleasing exterior finish for buildings. In addition, they can be used to slit steel for structural components such as beams and columns, where the steel may need to be in specific widths for proper construction.
2. Automotive Industry
- The automotive industry is another major user of steel coil slitting machines. They are used to slit steel coils for the production of car body parts. For example, the steel used for car doors, hoods, and fenders is often slit from large coils using these machines. The ability to produce steel strips of precise widths is crucial for ensuring that the body parts fit together properly during assembly. Steel coil slitting machines are also used to slit steel for engine parts and interior components. For instance, the steel used for seat frames or dashboard components may be produced by slitting steel coils.
3. Manufacturing Industry
- In the manufacturing industry, steel coil slitting machines have a wide range of applications. They are used to slit steel for the production of machinery parts. For example, gears, shafts, and bearings may require steel strips of specific widths and thicknesses, which can be obtained by slitting steel coils. In the production of consumer products such as appliances and furniture, steel coil slitting machines can be used to slit steel for frames and panels. The ability to customize the width of the steel strips allows for more efficient use of materials and better product design.
VI. Advantages of Steel Coil Slitting Machines
1. Customization
- One of the main advantages of steel coil slitting machines is their ability to customize the width of the steel strips. This allows different industries to obtain steel in the exact widths they need for their specific applications. For example, in the construction of a complex building structure, the ability to produce steel strips of different widths for various components can significantly improve the efficiency and quality of the construction process.
2. High - quality Output
- Steel coil slitting machines are designed to produce high - quality slit steel. The precise slitting mechanisms and control systems ensure that the slit steel strips have accurate widths and smooth edges. This high - quality output is important in industries where the performance and appearance of the end - product depend on the quality of the steel used. For example, in the automotive industry, high - quality slit steel is crucial for the safety and aesthetics of the vehicles.
3. Cost - effectiveness
- Although the initial investment in a steel coil slitting machine may be relatively high, in the long run, it can be cost - effective. By slitting large steel coils into narrower strips as needed, material waste is reduced. This is because only the required amount of steel in the desired widths is produced. Additionally, the high - quality output reduces the need for rework or rejection of products due to poor - quality steel, which further saves costs.
VII. Challenges and Solutions in Steel Coil Slitting Machine Operation
1. Blade Wear and Replacement
- One of the significant challenges in operating a steel coil slitting machine is blade wear. The slitting blades are subjected to high - stress conditions during the cutting of steel, which can cause them to wear out quickly. Blade wear can lead to a decrease in slitting quality, such as producing strips with rough edges or inaccurate widths. To address this, high - quality blades made of durable materials like carbide - tipped steel should be used. Regular blade inspection and replacement are also necessary. Some machines are equipped with blade - monitoring systems that can detect when a blade needs to be replaced based on factors such as blade wear or vibration.
2. Tension Control
- Tension control is a crucial aspect of steel coil slitting machine operation. Inconsistent tension can cause problems such as steel stretching, wrinkling, or misalignment. Maintaining the correct tension throughout the uncoiling, slitting, and recoiling processes is challenging. To overcome this, advanced tension control systems, such as those based on load cells and PID controllers, are used. These systems can measure the tension in real - time and make adjustments to the speed of the relevant components (such as the uncoiling or recoiling motors) to maintain the correct tension.
3. Alignment and Straightness of Steel
- Ensuring the alignment and straightness of the steel during the slitting process is another challenge. If the steel is not properly aligned or straight, it can lead to inaccurate slitting and poor - quality output. To address this, the machine is equipped with alignment and guiding devices. Guide rollers are used to keep the steel in the correct position, and some machines may use laser - guided alignment systems to ensure precise alignment of the steel during slitting.
VIII. Future Trends in Steel Coil Slitting Machines
1. Automation and Robotics
- The future of steel coil slitting machines will see increased automation and the integration of robotics. Robotic arms can be used for tasks such as loading and unloading steel coils, which can improve safety and efficiency. Automation can also be extended to the slitting process itself, with the ability to automatically adjust slitting parameters based on real - time data from sensors. This will further increase the precision and productivity of steel coil slitting machines.
2. Integration with Industry 4.0
- Steel coil slitting machines will be increasingly integrated with Industry 4.0 concepts. This means that they will be connected to the factory's overall network, allowing for real - time data sharing. Operators will be able to remotely monitor and control the slitting machine, and predictive maintenance will become more common. Sensors on the line will be able to detect potential problems before they cause a breakdown, and the necessary maintenance can be scheduled in advance.
3. Advanced Materials and Slitting Technologies
- As new materials are developed in the steel industry, steel coil slitting machines will need to adapt. For example, the development of high - strength and lightweight steels will require new slitting technologies. Laser - slitting technology may become more prevalent in steel coil slitting machines as it offers high - precision slitting for a wide range of steels. Additionally, new blade materials and designs may be developed to improve slitting efficiency and quality.
In conclusion, steel coil slitting machines are an essential part of the steel processing industry. Their ability to transform large steel coils into customized, high - quality slit steel strips makes them indispensable in various industries. As technology continues to evolve, these machines will continue to improve and adapt to meet the ever - changing needs of the manufacturing world.