Hotline
+86-136 8495 9862
Email:cennia@szmizhi.com
Add::104,Building 27,Third Industrial Zone, Longxi Community,Longgang District,Shenzhen,China.
Coil Forming & Handling Equipment
Surface Treatment Equipment
Solutions
Application
About Us
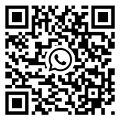
Welcome to MIZHI
For consultation/feedback, please call the service hotline: +86-136 8495 9862 Email:cennia@szmizhi.com
1. Introduction
In the vast landscape of metal processing, steel coil slitting machines stand as indispensable workhorses. These sophisticated pieces of equipment are engineered to transform large, unwieldy steel coils into precisely cut, narrow strips. The importance of steel coil slitting machines cannot be overstated, as they serve as the linchpin for numerous industries. From the construction of towering skyscrapers to the manufacturing of intricate automotive components and the production of everyday household appliances, the need for accurately slit steel strips is ubiquitous.
The ability to convert large coils into customized widths is crucial for optimizing material usage, reducing waste, and enhancing overall production efficiency. Manufacturers across various sectors rely on these machines to meet the exacting demands of their customers, whether it's providing specific strip widths for a high - end electronics product or creating uniform strips for a large - scale construction project. As technology continues to advance, steel coil slitting machines are evolving, becoming more precise, efficient, and adaptable to diverse materials and production requirements.
2. Working Principle
2.1. Fundamental Cutting Mechanism
At the heart of a steel coil slitting machine lies the cutting mechanism. This typically involves a set of circular blades that rotate at high speeds. The steel coil, which is initially in a rolled - up form, is fed into the machine. As the coil moves forward, the rotating blades slice through the steel, creating narrow strips of the desired width. The blades are mounted on a shaft, and the distance between adjacent blades can be adjusted to achieve different strip widths.
For example, in a common setup, the slitting head may have multiple pairs of blades. Each pair is responsible for cutting a single strip. The blades are made from high - quality materials such as hardened steel or carbide, which can withstand the high - stress cutting process. The sharp edges of the blades ensure a clean and precise cut, minimizing burrs and other imperfections on the cut edges of the steel strips.
2.2. Coil Unwinding and Feeding
Before the cutting process can commence, the steel coil needs to be unwound and fed into the slitting section. This is achieved through an uncoiler, which is designed to hold the heavy coil securely and release the steel in a controlled manner. The uncoiler can be either manually operated or automated, depending on the size and complexity of the slitting machine.
In an automated system, the uncoiler is equipped with motors and sensors. The motors control the speed at which the coil is unwound, ensuring a consistent feed rate. The sensors monitor the tension in the steel strip as it is being unwound. Maintaining the right tension is crucial, as too much tension can cause the steel to stretch or break, while too little tension can result in uneven feeding and inaccurate cuts.
The feeding mechanism then guides the unwound steel strip towards the slitting blades. This may involve a series of rollers that help to straighten the strip and keep it in a stable position. Some advanced feeding systems also incorporate alignment sensors to ensure that the steel strip is centered correctly before it enters the cutting zone.
2.3. Strip Winding and Collection
Once the steel strip has been slit into the desired widths, it needs to be wound into smaller coils or collected in a suitable manner. A recoiler is used for winding the slit strips into coils. Similar to the uncoiler, the recoiler is designed to control the tension and speed of the winding process.
The recoiler's core expands to grip the inner diameter of the coil being formed. As the strip is wound around the core, the recoiler adjusts the tension to ensure that the coil is wound tightly and evenly. In some cases, the slit strips may not be wound into coils but instead collected as straight lengths. This is common when the strips are going to be used in applications where a continuous coil is not required, such as in certain construction or fabrication processes.
3. Components of a Steel Coil Slitting Machine
3.1. Uncoiler
The uncoiler is the starting point of the slitting process. It comes in various designs to accommodate different coil sizes and weights. For small - scale operations, a simple, manually - operated uncoiler may be sufficient. This type of uncoiler typically consists of a spindle on which the steel coil is mounted. The operator can then manually rotate the spindle to unwind the coil.
However, in large - scale industrial settings, automated uncoilers are the norm. These are more complex and are equipped with features such as hydraulic or pneumatic expansion shafts. The expansion shaft allows for easy loading and unloading of the steel coil. When the coil is loaded, the shaft expands to grip the inner diameter of the coil firmly. This ensures that the coil remains stable during the unwinding process.
Automated uncoilers also often have motorized drive systems. These drives can be adjusted to control the speed of unwinding, which is crucial for maintaining a consistent feed rate to the slitting section. Some high - end uncoilers are even equipped with advanced tension control systems. These systems use sensors to measure the tension in the steel strip as it is being unwound. If the tension deviates from the set parameters, the system can automatically adjust the speed of the uncoiler or apply additional braking force to correct the tension.
3.2. Slitting Head
The slitting head is the most critical component of the steel coil slitting machine, as it is responsible for the actual cutting of the steel. The slitting head contains the cutting blades, which are mounted on a shaft. The blades are designed to be highly precise and durable. As mentioned earlier, they are typically made from materials like hardened steel or carbide.
The distance between the blades can be adjusted to achieve different strip widths. This adjustment can be done manually in some basic models, where the operator loosens the nuts or bolts holding the blades in place, moves the blades to the desired position, and then tightens the fasteners again. In more advanced machines, the blade adjustment is automated. Motorized actuators are used to move the blades accurately to the required positions. These actuators can be controlled through a computer - based control system, allowing for quick and precise changes in strip width.
The slitting head also includes a mechanism to ensure that the blades are properly aligned. Misaligned blades can result in uneven cuts, burrs, and other defects in the slit strips. Some slitting heads use precision - ground bearings to support the blade shaft, which helps to maintain the alignment of the blades during operation. Additionally, there may be alignment sensors that can detect any misalignment and alert the operator or automatically adjust the position of the blades.
3.3. Recoiler
The recoiler, as the name implies, is responsible for winding the slit steel strips into coils. It has a similar structure to the uncoiler but operates in reverse. The recoiler's core can expand and contract to accommodate different coil sizes. When the slit strips are fed into the recoiler, the core expands to grip the inner diameter of the coil being formed.
The recoiler is equipped with a motorized drive system that controls the speed of winding. The speed of the recoiler needs to be synchronized with the speed of the slitting process to ensure that the strips are wound evenly and without any slack or over - tension. This synchronization is typically achieved through a control system that monitors the speed of both the slitting head and the recoiler and adjusts the motor speeds accordingly.
Tension control is also a crucial aspect of the recoiler. The tension in the slit strips as they are being wound affects the quality of the final coil. If the tension is too high, the coil may be too tightly wound, which can cause the strips to deform or the coil to become unstable. On the other hand, if the tension is too low, the coil may be loose and prone to tangling. To address this, the recoiler is often equipped with a tension control system. This system can use various methods to control the tension, such as applying a braking force to the recoiler's core or adjusting the speed of the winding motor based on the measured tension.
3.4. Straightening and Leveling Units
Before the steel strip is slit, it may have some curvature or unevenness due to the coiling process or transportation. Straightening and leveling units are used to correct these imperfections. These units typically consist of a series of rollers.
The straightening unit works by passing the steel strip through a set of rollers that are arranged in a specific pattern. As the strip passes through the rollers, the rollers apply pressure to the strip, gradually straightening it. The number of rollers and their diameter can vary depending on the thickness and type of steel being processed. Thicker steels may require fewer but larger - diameter rollers, while thinner steels may need more rollers with smaller diameters.
The leveling unit, which is often used in conjunction with the straightening unit, further improves the flatness of the steel strip. It uses a similar principle of applying pressure through rollers but with a more refined adjustment mechanism. The leveling unit can be adjusted to correct for any remaining bow or camber in the strip, ensuring that the strip is perfectly flat before it enters the slitting section. This is crucial for achieving accurate and consistent cuts, as an uneven strip can cause the cutting blades to wear unevenly and result in inconsistent strip widths.
3.5. Control System
Modern steel coil slitting machines are equipped with sophisticated control systems. These control systems are typically based on programmable logic controllers (PLCs) or industrial computers. The control system allows the operator to set various parameters for the slitting process, such as the strip width, the cutting speed, the tension of the steel strip during unwinding and winding, and the speed of the uncoiler and recoiler.
For example, the operator can input the desired strip width on a touch - screen interface. The control system then calculates the required position of the cutting blades in the slitting head and automatically adjusts the blade positions using the motorized actuators. The control system also monitors the operation of the machine in real - time. It uses sensors to detect various parameters such as the speed of the motors, the tension in the steel strip, and the temperature of critical components.
If any of these parameters deviate from the set values, the control system can take corrective action. For instance, if the tension in the steel strip being unwound is too high, the control system can reduce the speed of the uncoiler or adjust the braking force to bring the tension back to the desired level. In case of a malfunction or an emergency, the control system can also immediately stop the machine to prevent damage to the equipment or the material. Some advanced control systems also offer remote monitoring and diagnostic capabilities, allowing plant managers or maintenance personnel to monitor the performance of the slitting machine from a remote location and perform troubleshooting without having to be physically present at the machine.
4. Types of Steel Coil Slitting Machines
4.1. Manual Slitting Machines
Manual slitting machines are the simplest and most basic type of steel coil slitting machines. They are typically used in small - scale workshops or for occasional slitting tasks where the volume of work is low. In a manual slitting machine, most of the operations are carried out by hand.
The operator is responsible for loading the steel coil onto the uncoiler, adjusting the position of the cutting blades in the slitting head to the desired width, and manually guiding the steel strip through the machine. The cutting process is often initiated by the operator turning a hand - crank or pressing a manual switch. The speed of the slitting process is relatively slow compared to automated machines, as it is limited by the operator's ability to control the movement of the steel strip and the cutting mechanism.
Manual slitting machines are relatively inexpensive to purchase and maintain. They do not require complex electrical or hydraulic systems, making them a cost - effective option for small - scale fabricators or hobbyists. However, their productivity is low, and the accuracy of the cuts may vary depending on the skill and experience of the operator. They are best suited for applications where the requirements for strip width precision are not extremely high and where the volume of slitting work is sporadic.
4.2. Semi - Automatic Slitting Machines
Semi - automatic slitting machines represent an intermediate level of automation. These machines combine some automated functions with manual operations. For example, the uncoiling and recoiling processes may be automated, while the adjustment of the cutting blades and the initial setup of the machine still require manual intervention.
The uncoiler in a semi - automatic machine is usually motorized, allowing for a more consistent and controlled unwinding of the steel coil. The recoiler also has a motorized drive system, which can wind the slit strips into coils at a relatively stable speed. However, when it comes to changing the strip width, the operator still needs to manually adjust the position of the cutting blades in the slitting head. This may involve loosening and tightening bolts or using a manual adjustment mechanism to move the blades to the desired position.
Semi - automatic slitting machines offer a balance between cost and productivity. They are more productive than manual machines as the automated uncoiling and recoiling processes save time. At the same time, they are less expensive than fully automatic machines, as they do not require complex control systems for blade adjustment. They are suitable for medium - scale operations where the volume of slitting work is not extremely high, but where a higher level of productivity and accuracy is desired compared to manual machines.
4.3. Fully Automatic Slitting Machines
Fully automatic slitting machines are the most advanced and sophisticated type of steel coil slitting machines. They are designed for high - volume production environments where precision, speed, and efficiency are of utmost importance. In a fully automatic slitting machine, virtually all aspects of the slitting process are automated.
The uncoiler, slitting head, and recoiler are all controlled by a computer - based control system. The operator only needs to input the desired parameters such as the strip width, the coil weight, and the material type into the control system. The control system then automatically adjusts the position of the cutting blades, controls the speed of the uncoiler and recoiler, and monitors the tension in the steel strip throughout the process.
Fully automatic slitting machines are equipped with advanced sensors and actuators. For example, the slitting head may have sensors that can detect the position of the cutting blades with high precision and adjust their position automatically if there is any deviation. The tension control system uses sensors to continuously monitor the tension in the steel strip and adjusts the speed of the uncoiler and recoiler in real - time to maintain the desired tension. These machines can also be integrated with other manufacturing systems, such as material handling systems and quality control systems, to create a seamless production line.
While fully automatic slitting machines are more expensive to purchase and maintain compared to manual and semi - automatic machines, they offer significant advantages in terms of productivity, accuracy, and consistency. They are capable of processing large volumes of steel coils quickly and producing slit strips with extremely tight tolerances. They are the preferred choice for large - scale steel processing plants, automotive manufacturers, and other industries where high - volume, high - precision slitting is required.
5. Applications in Different Industries
5.1. Automotive Industry
In the automotive industry, steel coil slitting machines play a crucial role in the production of various components. Steel strips of precise widths are required for manufacturing car body panels, such as doors, hoods, and fenders. The high - precision cutting capabilities of steel coil slitting machines ensure that the panels fit together perfectly during the assembly process.
For example, the doors of a car need to be made from steel strips that are cut to exact widths to ensure a proper fit and smooth operation. Any deviation in the width of the steel strips can lead to problems such as misalignment, difficulty in closing the door, or gaps in the body panels, which can affect the aesthetic appearance and the structural integrity of the vehicle. Steel coil slitting machines are also used to produce strips for automotive interior components, such as seat frames and dashboard supports. The strength and precision of the slit steel strips are essential for ensuring the safety and comfort of the vehicle's occupants.
5.2. Construction Industry
The construction industry is another major consumer of steel coil slitting machines. Steel strips are used in a wide range of construction applications, including roofing, wall cladding, and structural components. In roofing applications, steel coil slitting machines are used to produce long, continuous strips of the appropriate width for covering roofs. These strips need to be cut accurately to ensure a proper fit and a watertight seal.
For wall cladding, the slit steel strips are used to create panels that are both aesthetically pleasing and durable. The precision of the cutting process ensures that the panels fit together tightly, providing a weather - resistant and attractive exterior for buildings. In the case of structural components, such as steel beams and columns, steel coil slitting machines may be used to produce the raw materials that are further processed into the final structural elements. The ability to produce steel strips of consistent quality and width is crucial for the safety and stability of construction projects.
5.3. Electronics Industry
In the electronics industry, steel coil slitting machines are used to produce components for various electronic devices. For example, steel strips are used in the manufacturing of electronic enclosures, such as those for computers, servers, and consumer electronics. The precise cutting of the steel strips is essential for ensuring a proper fit of the components and for protecting the delicate electronic components inside.
Steel coil slitting machines are also used to produce parts for electrical connectors and circuit boards. The high - precision cutting capabilities of these machines allow for the production of small, intricate steel parts with tight tolerances. In the electronics industry, even the slightest deviation in the dimensions of the components can affect the performance of the final product. Therefore, the use of steel coil slitting machines is crucial for meeting the strict quality requirements of the electronics manufacturing sector.
5.4. Metal Service Centers
Metal service centers act as intermediaries between steel producers and end - users. They purchase large steel coils and use steel coil slitting machines to cut them into smaller, more manageable sizes and widths as per the requirements of their customers. These service centers need to be able to provide a wide range of strip widths and lengths to meet the diverse needs of different industries.
Steel coil slitting machines enable metal service centers to offer customized solutions to their customers. They can quickly and efficiently process large coils into the specific widths and lengths required by manufacturers in various sectors. The ability to provide such customized services helps metal service centers to stay competitive in the market and meet the demands of their customers in a timely manner.
6. Maintenance and Troubleshooting
6.1. Regular Maintenance Procedures
Regular maintenance is essential to keep a steel coil slitting machine operating at peak performance. One of the key maintenance tasks is the inspection and replacement of the cutting blades. The blades are subject to wear and tear during the cutting process, and dull blades can lead to poor - quality cuts, increased burrs, and higher energy consumption. The blades should be inspected regularly for signs of wear, such as dull edges or chips. When the blades are worn beyond a certain point, they should be replaced with new ones.