Hotline
+86-136 8495 9862
Email:cennia@szmizhi.com
Add::104,Building 27,Third Industrial Zone, Longxi Community,Longgang District,Shenzhen,China.
Coil Forming & Handling Equipment
Surface Treatment Equipment
Solutions
Application
About Us
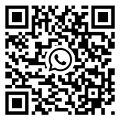
Welcome to MIZHI
For consultation/feedback, please call the service hotline: +86-136 8495 9862 Email:cennia@szmizhi.com
1. Introduction
In the vast and complex world of steel processing, the steel cut - to - length machine stands as a cornerstone of modern manufacturing operations. Steel, being one of the most widely used materials across industries such as construction, automotive, and manufacturing, requires precise and efficient processing. The cut - to - length machine is designed to meet this need by accurately slicing steel coils, sheets, or bars into specific lengths as per the requirements of downstream applications. This not only streamlines the production process but also significantly enhances the overall quality and usability of the steel products.
2. Working Mechanism
2.1 Material Feeding
The operation of a steel cut - to - length machine commences with the feeding of the steel material. When dealing with coil - fed machines, a decoiling unit is an essential component. This unit is responsible for carefully unwinding the steel coil. It must ensure a smooth and consistent release of the steel strip to prevent any kinks, twists, or uneven feeding that could disrupt the cutting process. The decoiling speed is often adjustable to match the processing speed of the subsequent cutting and measuring operations.
For sheet - fed machines, the steel sheets are either manually or automatically loaded onto a feeding table. In automated systems, conveyors or robotic arms are used to precisely position the sheets for accurate cutting. The feeding table may be equipped with features such as adjustable guides and clamps to hold the steel in place during the feeding process.
2.2 Measurement Systems
Accurate measurement is the heart of a steel cut - to - length machine. Encoders are commonly employed for this purpose. These devices can be mechanical, optical, or magnetic, and they work by tracking the movement of the steel material as it passes through the machine. As the steel moves, the encoder generates pulses that are directly proportional to the distance traveled. By counting these pulses, the machine can precisely determine the length of the steel that has passed through.
Laser measurement systems are also increasingly popular. A laser beam is directed onto the surface of the steel, and the reflection of the beam is detected. The time it takes for the laser to travel to the steel and back is used to calculate the distance, providing highly accurate length measurements. Some advanced machines may even use a combination of encoders and laser sensors to achieve even greater precision.
2.3 Cutting Mechanisms
Once the desired length has been accurately measured, the cutting mechanism swings into action. Shearing is one of the most common cutting methods for steel. In a shearing operation, two sharp blades are used. One blade is fixed, while the other moves in a controlled manner to exert a shearing force on the steel. The blades are made from high - strength, wear - resistant materials such as hardened steel or carbide - tipped alloys to ensure a clean and precise cut. The design of the blades, including their shape, angle, and sharpness, is carefully optimized to suit the thickness and type of steel being cut.
Plasma cutting is another viable option, especially for thicker steel sections. In this process, a high - temperature plasma arc is generated. The plasma arc melts and vaporizes the steel as it moves along the cutting path, creating a clean cut. Plasma cutting is known for its ability to cut through thick steel quickly, but it may require some post - processing to clean the edges and remove any slag or oxidation.
Laser cutting is also gaining popularity in the steel cut - to - length industry, particularly for applications that demand extremely high precision and fine - quality cuts. A high - power laser beam is focused onto the steel surface, melting and vaporizing the material in a highly controlled manner. Laser cutting can produce very narrow kerfs (the width of the cut), resulting in minimal material waste, and is suitable for cutting complex shapes and patterns in addition to straight lengths.
3. Types of Steel Cut - to - Length Machines
3.1 Roll - to - Roll Cut - to - Length Machines
Roll - to - roll steel cut - to - length machines are specifically designed for processing steel coils. These machines are widely used in industries such as metal stamping and automotive component manufacturing. They can handle a wide range of coil widths and thicknesses, from thin - gauge steel used in the production of electrical components to thicker steel coils for automotive body panels.
The roll - to - roll process allows for continuous production, with the steel being fed from the coil, cut to length, and then discharged in a seamless operation. This type of machine often has a high - speed cutting mechanism to maximize productivity, and it can be integrated with other downstream processes such as stamping or welding lines.
3.2 Sheet - Fed Cut - to - Length Machines
Sheet - fed steel cut - to - length machines are used when the starting material is in the form of pre - cut steel sheets. These machines are commonly found in the construction industry, where they are used to cut steel sheets for roofing, siding, and structural components. They can also be used in the manufacturing of metal furniture and storage units.
Sheet - fed machines typically have a flat feeding table and a cutting mechanism that can move across the table to make cuts at various positions. Some models are equipped with multiple cutting heads or adjustable cutting fences to enable the cutting of different sheet sizes and shapes.
3.3 Bar Cut - to - Length Machines
Bar cut - to - length machines are designed to cut steel bars into specific lengths. These machines are used in applications such as construction (for cutting rebar), manufacturing of machinery parts, and the production of metal fasteners. The bar - cutting process may involve different cutting methods, such as cold sawing, where a circular saw blade with sharp teeth cuts through the steel bar. Cold sawing is preferred for applications that require a smooth cut surface and minimal burr formation.
In some cases, for very large - diameter bars or when a faster cutting speed is required, abrasive cutting methods may be used. Abrasive cutting involves using a high - speed abrasive wheel to grind through the steel bar. However, this method may produce more heat and require additional cooling and post - processing to ensure the quality of the cut ends.
4. Applications across Industries
4.1 Construction Industry
In the construction industry, steel cut - to - length machines play a vital role. For building structures, steel reinforcement bars (rebar) need to be cut to precise lengths depending on the design of the foundation, columns, and beams. The use of a cut - to - length machine ensures that each rebar is of the correct length, which is crucial for the structural integrity of the building.
Steel sheets are also cut to length for various construction applications, such as roofing and siding. The accurate cutting of these sheets ensures a proper fit, reducing the need for on - site adjustments and minimizing the risk of water leakage or other issues. In addition, steel beams and structural members may be cut to length from larger steel sections, allowing for efficient construction and assembly on - site.
4.2 Automotive Industry
The automotive industry relies heavily on steel cut - to - length machines for the production of various components. Steel sheets are cut to precise lengths for the manufacturing of car body panels, such as the hood, doors, and trunk lid. The accuracy of the cut is essential for the proper fit and assembly of these panels, as well as for the overall aerodynamics and aesthetics of the vehicle.
Steel bars and tubes are also cut to length for the production of chassis components, suspension parts, and engine components. The high - precision cutting provided by the cut - to - length machines ensures the consistent quality and performance of these automotive parts, contributing to the safety and reliability of the vehicles.
4.3 Manufacturing Industry
In the general manufacturing industry, steel cut - to - length machines are used in a wide range of applications. For example, in the production of industrial machinery, steel components such as shafts, brackets, and frames are cut to length. The precise cutting allows for easy assembly and ensures the proper functioning of the machinery.
In the production of metal furniture, steel tubes and sheets are cut to create the frames and components of chairs, tables, and cabinets. The accurate cutting not only improves the quality of the furniture but also reduces the production time and cost by minimizing the need for rework.
5. Advantages of Steel Cut - to - Length Machines
5.1 High Precision
One of the most significant advantages of steel cut - to - length machines is their high precision. They can achieve cutting tolerances as low as ±0.1mm or even less in some advanced models. This level of precision ensures that the cut steel pieces are of the exact dimensions required for the subsequent manufacturing processes. For example, in the automotive industry, precise cuts are essential for the proper fit of body panels, reducing the need for costly rework and improving the overall quality of the vehicle.
5.2 Increased Efficiency
Steel cut - to - length machines are designed to operate at high speeds, which significantly increases production efficiency. In a roll - to - roll cut - to - length machine, for instance, the continuous feeding and cutting process can process hundreds of meters of steel per minute. The automated nature of these machines also reduces the need for manual labor, further enhancing productivity. This increased efficiency allows manufacturers to meet high - volume production demands in a timely manner.
5.3 Waste Reduction
By accurately cutting steel to the required lengths, these machines minimize material waste. In traditional cutting methods, inaccurate cuts often result in excess material that needs to be discarded. With the high - precision cutting capabilities of steel cut - to - length machines, manufacturers can optimize the use of raw materials. This not only reduces the cost of raw materials but also has a positive environmental impact by reducing waste and the need for additional steel production.
5.4 Versatility
Steel cut - to - length machines are highly versatile. They can handle different types of steel, including carbon steel, stainless steel, and alloy steel, as well as a wide range of thicknesses and widths. This versatility makes them suitable for a variety of industries and applications. Additionally, many machines can be easily adjusted to cut different lengths and shapes, providing flexibility in production.
6. Challenges and Solutions
6.1 Wear and Tear of Cutting Tools
The cutting tools in a steel cut - to - length machine, such as blades or plasma torches, are subject to significant wear and tear due to the high - strength nature of steel. Over time, the cutting edges may become dull, leading to poor - quality cuts, increased cutting forces, and reduced productivity. To address this issue, manufacturers use high - quality, wear - resistant cutting tools. Regular maintenance, including sharpening or replacing the cutting tools at appropriate intervals, is also crucial. Some advanced machines are equipped with automatic tool - monitoring systems that can detect the wear of the cutting tools and alert the operator when replacement is necessary.
6.2 Material Variability
Steel can vary in its properties from batch to batch, such as hardness, thickness, and surface finish. These variations can pose challenges to the cutting process. For example, if the steel is harder than expected, it may require more cutting force, which can affect the accuracy of the cut and the lifespan of the cutting tools. To overcome this, modern steel cut - to - length machines are often equipped with sensors that can detect the properties of the incoming steel material. Based on the data collected by these sensors, the machine can automatically adjust the cutting parameters, such as cutting speed, force, and power, to ensure a consistent and high - quality cut.
6.3 Integration with Other Systems
In many manufacturing processes, the steel cut - to - length machine needs to be integrated with other equipment, such as stamping presses, welding robots, or automated conveyor systems. Ensuring seamless integration can be a complex task. To solve this problem, manufacturers are increasingly adopting standard communication protocols and interfaces in their machines. This allows for easier connection and coordination between different pieces of equipment, enabling the implementation of fully automated manufacturing lines. For example, a steel cut - to - length machine can be integrated with a stamping press such that the cut - to - length steel pieces are automatically fed into the stamping process without the need for manual handling.
7. Future Trends
7.1 Automation and Robotics Integration
The future of steel cut - to - length machines lies in increased automation and integration with robotics. More advanced machines will be able to operate with minimal human intervention. Robots can be used for tasks such as material loading, unloading, and quality inspection. For example, robotic arms can precisely load steel coils onto the decoiling unit or pick up the cut - to - length steel pieces and place them onto the conveyor for further processing. This not only increases productivity but also improves workplace safety by reducing the risk of human - related accidents.
7.2 Smart Manufacturing and IoT Connectivity
Steel cut - to - length machines will become an integral part of the smart manufacturing ecosystem. Through Internet of Things (IoT) connectivity, these machines will be able to send and receive data in real - time. Manufacturers can monitor the performance of the machines remotely, including parameters such as cutting speed, tool wear, and energy consumption. Predictive maintenance can be implemented based on the data collected, allowing for the replacement of parts before they fail, reducing downtime, and increasing the overall efficiency of the production process.
7.3 Advanced Cutting Technologies
New and improved cutting technologies will continue to emerge. For example, the development of more powerful and precise laser cutting systems will enable even higher - quality cuts on a wider range of steel materials. Hybrid cutting methods, combining different cutting techniques such as laser and water - jet cutting, may also become more common. These hybrid methods can offer unique advantages in terms of cut quality, speed, and material compatibility, further enhancing the capabilities of steel cut - to - length machines.
In conclusion, the steel cut - to - length machine is an essential piece of equipment in the steel processing and manufacturing industries. Its ability to accurately cut steel to the required lengths, combined with its high efficiency, versatility, and waste - reduction benefits, makes it a crucial component in modern production lines. As technology continues to advance, these machines will play an even more significant role in driving innovation and productivity in the steel - related industries.