Hotline
+86-136 8495 9862
Email:cennia@szmizhi.com
Add::104,Building 27,Third Industrial Zone, Longxi Community,Longgang District,Shenzhen,China.
Coil Forming & Handling Equipment
Surface Treatment Equipment
Solutions
Application
About Us
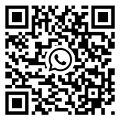
Welcome to MIZHI
For consultation/feedback, please call the service hotline: +86-136 8495 9862 Email:cennia@szmizhi.com
I. Introduction
In the world of steel processing, the steel cut to length machine has emerged as a game-changer. This advanced piece of equipment is designed to precisely cut steel sheets and coils into specific lengths, meeting the diverse needs of various industries. From construction and manufacturing to automotive and aerospace, the steel cut to length machine offers numerous benefits and has become an essential tool for businesses looking to improve efficiency and quality. In this article, we will explore the features, advantages, and applications of the steel cut to length machine.
II. Features of the Steel Cut to Length Machine
A. High Precision Cutting
1. Advanced Cutting Technology
The steel cut to length machine is equipped with state-of-the-art cutting technology that ensures accurate and consistent cuts. Whether it's using a guillotine shear or a laser cutting system, these machines are capable of achieving tight tolerances and clean cuts. For example, a high-quality guillotine shear can cut steel sheets with a tolerance of less than a millimeter, ensuring that each piece is precisely the desired length.
2. Adjustable Cutting Parameters
These machines allow operators to adjust various cutting parameters such as cutting length, speed, and force. This flexibility enables businesses to customize the cutting process according to their specific requirements. For instance, if a particular project requires shorter lengths and faster cutting speeds, the operator can easily adjust the settings on the machine to meet these needs.
3. Automated Measurement and Control
Many steel cut to length machines are equipped with automated measurement and control systems. These systems use sensors and software to accurately measure the length of the steel sheet and control the cutting process. This not only ensures precise cuts but also reduces the risk of human error and improves overall productivity.
B. Efficient Material Handling
1. Coil Uncoiling System
The steel cut to length machine typically includes a coil uncoiling system that allows for the seamless feeding of steel coils into the cutting process. This system can handle coils of various sizes and weights, making it suitable for a wide range of applications. Some uncoiling systems are equipped with automatic coil loading and unloading features, further enhancing efficiency and reducing labor requirements.
2. Straightening System
To ensure accurate cutting, many machines also feature a straightening system. This system flattens and aligns the steel sheet before it enters the cutting area, reducing the risk of crooked cuts and improving the quality of the finished product. The straightening system can be adjusted to handle different thicknesses and types of steel, providing flexibility for various applications.
3. Conveyor System
After cutting, the steel sheets are typically transported by a conveyor system to the next stage of the production process or for packaging and shipping. The conveyor system can be customized to fit the specific needs of the production line, ensuring smooth and efficient material flow.
C. Durable Construction
1. Heavy-Duty Frame
The steel cut to length machine is built with a heavy-duty frame that can withstand the rigors of continuous operation. The frame is typically made of high-quality steel or other durable materials to ensure stability and longevity. This durability is essential for businesses that rely on these machines for high-volume production.
2. Quality Components
The machine is equipped with high-quality components such as cutting blades, motors, and control systems. These components are designed to withstand heavy use and provide reliable performance over a long period. For example, a high-quality cutting blade can last for thousands of cuts before needing to be replaced, reducing maintenance costs and downtime.
3. Protective Features
To ensure operator safety and prolong the life of the machine, many steel cut to length machines are equipped with protective features such as safety guards, emergency stop buttons, and overload protection. These features help prevent accidents and damage to the machine, ensuring a safe and productive working environment.
III. Advantages of the Steel Cut to Length Machine
A. Increased Efficiency
1. High-Speed Cutting
The advanced cutting technology and automated processes of the steel cut to length machine enable high-speed cutting, significantly reducing production time. For example, a modern machine can cut steel sheets at speeds of several meters per minute, compared to manual cutting methods that are much slower and less efficient.
2. Reduced Labor Requirements
With automated material handling and cutting processes, the steel cut to length machine reduces the need for manual labor. This not only saves on labor costs but also improves productivity by minimizing human error and fatigue. Operators can focus on monitoring the machine and performing other tasks, rather than spending time on manual cutting and handling.
3. Consistent Quality
The precise cutting and material handling capabilities of the machine ensure consistent quality of the finished product. Each piece is cut to the exact length and specification, reducing waste and rework. This consistency is essential for businesses that need to meet strict quality standards and customer requirements.
B. Cost Savings
1. Material Optimization
By accurately cutting steel sheets to the required lengths, the steel cut to length machine minimizes material waste. This is especially important for businesses that work with expensive steel materials, as it can lead to significant cost savings over time. Additionally, the ability to cut multiple pieces from a single coil reduces the need for multiple purchases of smaller lengths, further optimizing material usage.
2. Reduced Maintenance Costs
The durable construction and quality components of the machine result in lower maintenance costs. With proper maintenance and care, these machines can operate for many years without major breakdowns or repairs. This reduces downtime and saves on repair and replacement costs, enhancing the overall cost-effectiveness of the equipment.
3. Energy Efficiency
Some steel cut to length machines are designed with energy-efficient features such as variable frequency drives and optimized cutting processes. These features help reduce energy consumption, lowering operating costs and minimizing the environmental impact of the production process.
C. Versatility and Flexibility
1. Wide Range of Applications
The steel cut to length machine can be used to process a variety of steel materials, including carbon steel, stainless steel, and alloy steel. It can handle different thicknesses and widths of steel sheets, making it suitable for a wide range of applications in industries such as construction, manufacturing, automotive, and aerospace.
2. Customization Options
Many machines offer customization options such as different cutting lengths, widths, and shapes. This allows businesses to meet the specific needs of their customers and projects, providing greater flexibility and competitiveness. For example, a manufacturer can use the machine to cut steel sheets into custom sizes for a particular construction project or automotive part.
3. Easy Integration
The steel cut to length machine can be easily integrated into existing production lines or used as a standalone unit. This flexibility makes it a valuable addition to any steel processing facility, regardless of its size or complexity. It can be connected to other equipment such as coil handling systems, welding machines, and painting lines to create a seamless production process.
IV. Applications of the Steel Cut to Length Machine
A. Construction Industry
1. Roofing and Siding Panels
In the construction of buildings, steel cut to length machines are used to produce roofing and siding panels. These panels are cut to specific lengths and widths to fit the dimensions of the building, providing a durable and aesthetically pleasing exterior. The precise cutting and consistent quality of the machine ensure that the panels fit together tightly and provide long-lasting protection.
2. Structural Components
The construction industry also uses steel cut to length machines to produce structural components such as beams, columns, and braces. These components are cut to the required lengths and specifications to ensure the strength and stability of the building. The high precision cutting of the machine is essential for ensuring proper fit and alignment during construction.
3. Metal Fabrication
Steel cut to length machines are widely used in metal fabrication shops for producing various metal products such as storage tanks, conveyor systems, and machinery parts. The ability to cut steel sheets accurately and efficiently allows fabricators to create complex shapes and designs, meeting the specific needs of their customers.
B. Manufacturing Industry
1. Automotive Parts
In the automotive industry, steel cut to length machines are used to produce parts such as body panels, chassis components, and engine parts. The precise cutting and consistent quality of the machine ensure that these parts fit together precisely and meet the strict quality standards of the automotive industry. The high-speed cutting capabilities of the machine also enable manufacturers to meet the demand for large quantities of parts in a timely manner.
2. Appliance Manufacturing
The manufacturing of appliances such as refrigerators, washing machines, and ovens also requires the use of steel cut to length machines. These machines are used to cut steel sheets for the production of appliance cabinets, panels, and other components. The ability to customize the cutting process allows manufacturers to create unique designs and features for their products.
3. Industrial Equipment
Steel cut to length machines are used in the production of industrial equipment such as conveyor systems, storage racks, and machinery parts. The precise cutting and durable construction of the machine ensure that these components are of high quality and can withstand the harsh environments of industrial applications.
C. Other Industries
1. Aerospace Industry
The aerospace industry uses steel cut to length machines to produce parts for aircraft and spacecraft. The high precision cutting and quality control requirements of this industry make these machines essential for ensuring the safety and performance of aerospace components.
2. Oil and Gas Industry
In the oil and gas industry, steel cut to length machines are used to produce pipes, tubes, and other components for oil and gas exploration and production. The durability and corrosion resistance of steel make it an ideal material for these applications, and the precise cutting of the machine ensures that the components fit together tightly and function properly.
3. Renewable Energy Industry
The renewable energy industry, such as solar and wind power, also uses steel cut to length machines to produce components for solar panels, wind turbines, and energy storage systems. The ability to cut steel sheets accurately and efficiently is crucial for the production of these large-scale structures.
The steel cut to length machine has revolutionized the steel processing industry by offering high precision cutting, efficient material handling, and durable construction. Its numerous advantages, including increased efficiency, cost savings, and versatility, make it an essential tool for businesses in various industries. Whether it's for construction, manufacturing, or other applications, the steel cut to length machine provides a reliable and efficient solution for cutting steel sheets to the required lengths. As technology continues to advance, we can expect these machines to become even more advanced and capable, further enhancing the productivity and quality of steel processing.