Hotline
+86-136 8495 9862
Email:cennia@szmizhi.com
Add::104,Building 27,Third Industrial Zone, Longxi Community,Longgang District,Shenzhen,China.
Coil Forming & Handling Equipment
Surface Treatment Equipment
Solutions
Application
About Us
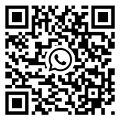
Welcome to MIZHI
For consultation/feedback, please call the service hotline: +86-136 8495 9862 Email:cennia@szmizhi.com
I. Introduction
Steel slitter manufacturers play a vital role in the steel industry. These manufacturers produce machines that are essential for processing steel coils into narrower strips, which are then used in a wide range of applications across various industries. The quality, innovation, and reliability of steel slitter manufacturers can significantly impact the efficiency and effectiveness of steel processing operations.
II. Types of Steel Slitters Produced
A. Manual Steel Slitters
1. Small - scale Operations
Some steel slitter manufacturers produce manual steel slitters, which are suitable for small - scale operations or workshops. These machines are often more affordable and simpler in design. Manual steel slitters are typically used for cutting relatively thin and narrow steel strips. For example, in a small metal fabrication shop that specializes in custom - made metal products, a manual slitter might be used to cut steel strips for decorative purposes or for small - scale manufacturing of items like brackets or hinges.
2. Advantages and Limitations
The main advantage of manual steel slitters is their cost - effectiveness and ease of use for simple tasks. They require less initial investment compared to automated slitters. However, they are limited in terms of production speed and precision. Manual operation means that the cutting speed is dependent on the operator's skill and physical ability, and it may be difficult to achieve extremely accurate and consistent slitting widths.
B. Semi - automated Steel Slitters
1. Mid - range Applications
Semi - automated steel slitters are designed to bridge the gap between manual and fully automated machines. These are popular among medium - sized manufacturing companies that need more efficiency than what manual slitters can offer but may not require the high - volume production capabilities of fully automated systems. For instance, a company that produces a moderate quantity of steel components for the construction industry might use a semi - automated slitter.
2. Features and Benefits
Semi - automated steel slitters often come with features such as motor - driven blade rotation and some level of automatic feed control. This combination allows for faster slitting speeds compared to manual slitters while still maintaining a certain level of operator control. They can also be more precise than manual slitters, as the automated components help in maintaining consistent blade rotation and feed rates. However, they still require some operator intervention, such as loading and unloading the steel coils and adjusting certain parameters during the slitting process.
C. Fully Automated Steel Slitters
1. High - volume Production
Fully automated steel slitter manufacturers target large - scale steel processing plants that demand high - volume production with maximum precision. These machines are capable of handling large - diameter steel coils and can slit them into multiple narrow strips simultaneously. In the automotive or large - scale construction industries, where huge quantities of precisely slit steel strips are required, fully automated steel slitters are the go - to choice.
2. Technological Sophistication
Fully automated steel slitters incorporate advanced technologies such as computer - controlled blade adjustment, real - time monitoring of the slitting process, and automated coil handling systems. For example, the blade gap can be adjusted automatically based on the thickness of the steel coil being processed, ensuring optimal slitting quality. These machines also often have high - speed cutting capabilities and can maintain a consistent slitting width throughout the entire coil, minimizing waste and maximizing productivity.
III. Factors Influencing Steel Slitter Manufacturers' Success
A. Technological Innovation
1. Research and Development
Successful steel slitter manufacturers invest heavily in research and development. They are constantly exploring new ways to improve the slitting process, such as developing more efficient blade materials or advanced cutting algorithms. For example, manufacturers may be researching new types of carbide - based blade materials that can withstand higher cutting forces and last longer when slitting hard - to - cut steels. They also study ways to optimize the slitting mechanism to reduce energy consumption while maintaining high - speed and accurate slitting.
2. Adaptation to New Steel Grades
As the steel industry evolves and new steel grades are developed, steel slitter manufacturers need to adapt their machines. New steel grades may have different mechanical properties, such as increased hardness or ductility, which can pose challenges for slitting. Manufacturers must ensure that their slitters can handle these new materials effectively. For instance, with the rise of high - strength, low - alloy steels in the construction and automotive industries, slitter manufacturers have had to modify their machines' cutting parameters and blade designs to achieve proper slitting.
B. Quality Control
1. Manufacturing Processes
High - quality steel slitter manufacturers have strict manufacturing processes. They start with high - quality raw materials for building the slitter components. For example, using high - grade steel for the machine frames and precision - engineered parts for the slitting blades and drive systems. During the assembly process, they follow stringent quality control procedures to ensure that all parts are properly fitted and calibrated. This includes using advanced metrology tools to measure and adjust components to exact specifications.
2. Testing and Certification
Before a steel slitter leaves the factory, it undergoes rigorous testing. Manufacturers test the slitter for various parameters, such as slitting accuracy, blade performance, and overall machine reliability. They also seek relevant certifications, such as ISO standards, which validate the quality of their machines. These certifications not only give customers confidence in the product but also help manufacturers in competing in the global market.
C. Customer Service
1. Technical Support
Providing excellent technical support is crucial for steel slitter manufacturers. Customers may encounter issues during installation, operation, or maintenance of the slitter. Manufacturers need to have a team of experienced technicians who can offer timely and effective support. This can include on - site assistance for large - scale installations or remote support via phone or internet for minor issues. Technical support also involves training the customer's staff on how to operate and maintain the slitter properly.
2. Customization Options
Many customers have specific requirements for their steel slitters. Manufacturers that can offer customization options are more likely to succeed. For example, a customer in the automotive industry may need a slitter with a particular slitting width range and a high - speed cutting capability to meet their production demands. A steel slitter manufacturer that can design and produce a machine tailored to these requirements will have an edge in the market.
IV. Global Market for Steel Slitter Manufacturers
A. Key Regions and Their Characteristics
1. Europe
In Europe, steel slitter manufacturers are known for their high - quality engineering and precision - made machines. German manufacturers, for example, are renowned for their advanced technology and strict quality control. Their steel slitters are often used in high - end manufacturing sectors such as automotive and aerospace. Italian manufacturers may focus more on the design aspect, producing steel slitters with aesthetically pleasing and ergonomic designs, which are also suitable for medium - scale manufacturing in sectors like furniture and machinery.
2. Asia
Asia is a major hub for steel slitter manufacturing. Chinese manufacturers have a large market share, especially in the production of cost - effective steel slitters for a wide range of industries. They are able to offer competitive prices due to their large - scale production capabilities and relatively lower labor costs. Japanese manufacturers, on the other hand, are known for their technological innovation and reliability. Their steel slitters are often used in high - tech industries such as electronics and precision machinery.
3. North America
In North America, steel slitter manufacturers tend to focus on meeting the specific needs of the local industries. For example, in the United States, manufacturers may produce steel slitters that are compliant with strict environmental and safety regulations. These machines are often designed for the construction, oil and gas, and heavy - equipment manufacturing industries in the region. Canadian manufacturers may have a niche in the production of steel slitters for the forestry and mining industries, where the machines need to be adapted to handle specific types of steel used in those sectors.
B. Market Trends and Competition
1. Increasing Demand for High - Precision Slitters
The global market is seeing an increasing demand for high - precision steel slitters. With the growth of industries such as electronics and aerospace, where tight tolerances are required for steel components, manufacturers are competing to produce slitters with the highest accuracy. This has led to a race among steel slitter manufacturers to develop more precise blade adjustment systems, better measurement and control technologies, and improved overall machine stability.
2. Cost - competitiveness
Cost - competitiveness is also a major factor in the global market for steel slitter manufacturers. As companies strive to reduce production costs, they are looking for cost - effective steel slitting solutions. Manufacturers in low - cost regions, such as Asia, are expanding their market share by offering affordable yet reliable steel slitters. At the same time, manufacturers in high - cost regions are focusing on adding value through superior quality, advanced technology, and better customer service to justify their higher prices.
V. Future Developments in Steel Slitter Manufacturing
A. Integration with Industry 4.0
1. Smart Manufacturing Features
The future of steel slitter manufacturing is likely to see greater integration with Industry 4.0 concepts. Manufacturers will incorporate more smart manufacturing features into their machines. For example, using the Internet of Things (IoT) to connect steel slitters to a network, allowing for remote monitoring and control. This will enable operators to monitor the machine's performance, such as blade wear, slitting speed, and coil handling, from a remote location. Machine - learning algorithms can be used to optimize the slitting process based on real - time data, such as automatically adjusting the blade gap or cutting speed depending on the characteristics of the steel coil being processed.
2. Predictive Maintenance
Another aspect of Industry 4.0 integration is predictive maintenance. Sensors will be installed on steel slitters to monitor various parameters related to the machine's health. Based on the data collected, predictive models can be developed to anticipate when a component is likely to fail or when maintenance is required. This will help manufacturers and users to reduce unplanned downtime, increase machine reliability, and save on maintenance costs.
B. Environmental Considerations
1. Energy - efficient Designs
As environmental concerns grow, steel slitter manufacturers will focus on developing more energy - efficient designs. This could involve using more efficient motors and drive systems, optimizing the slitting process to reduce energy consumption, and incorporating energy - recovery mechanisms. For example, some manufacturers may explore ways to recover and reuse the energy generated during the slitting process, such as converting the heat generated by blade friction into useful energy.
2. Sustainable Manufacturing Practices
Manufacturers will also adopt more sustainable manufacturing practices. This includes using recyclable materials in the construction of steel slitters, reducing waste during the manufacturing process, and ensuring that their production facilities are environmentally friendly. For example, using recycled steel for non - critical machine components or implementing water - recycling systems in the manufacturing plant.
In conclusion, steel slitter manufacturers are at the heart of the steel processing industry. Their ability to innovate, maintain high - quality standards, provide excellent customer service, and adapt to market trends will determine their success in a highly competitive global market. With future developments in Industry 4.0 integration and environmental considerations, the steel slitter manufacturing industry is poised for significant changes in the coming years.