Hotline
+86-136 8495 9862
Email:cennia@szmizhi.com
Add::104,Building 27,Third Industrial Zone, Longxi Community,Longgang District,Shenzhen,China.
Coil Forming & Handling Equipment
Surface Treatment Equipment
Solutions
Application
About Us
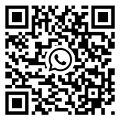
Welcome to MIZHI
For consultation/feedback, please call the service hotline: +86-136 8495 9862 Email:cennia@szmizhi.com
In the world of metal fabrication and manufacturing, steel slitter manufacturers play a crucial role in providing the equipment and technology needed to transform large coils of steel into narrower strips with precision and efficiency. These manufacturers are at the forefront of innovation, constantly striving to improve their products and meet the evolving needs of various industries.
The steel slitting process is a complex and demanding operation that requires specialized machinery and expertise. Steel slitter manufacturers design and build machines that can handle the tough and durable nature of steel, while also ensuring accurate cuts and consistent quality. These machines typically consist of an unwind stand, a slitting section, and a rewind stand, along with a variety of control systems and safety features.
One of the key challenges faced by steel slitter manufacturers is the need to produce machines that can handle a wide range of steel grades and thicknesses. Different types of steel have different properties and require different cutting techniques and blade materials. Manufacturers must therefore have a deep understanding of metallurgy and materials science in order to design machines that can handle the diverse requirements of their customers.
In addition to handling different steel grades and thicknesses, steel slitter manufacturers must also ensure that their machines are capable of producing high-quality cuts with minimal waste. This requires precise control of the slitting process, including blade speed, tension, and alignment. Manufacturers use advanced technologies such as computer numerical control (CNC) systems and laser-guided cutting to achieve the highest levels of precision and accuracy.
Another important aspect of steel slitter manufacturing is the design and construction of the machines themselves. These machines must be robust and reliable, able to withstand the rigors of continuous operation in a demanding industrial environment. Manufacturers use high-quality materials and advanced manufacturing techniques to ensure that their machines are built to last and can provide years of trouble-free service.
In addition to manufacturing steel slitters, many manufacturers also offer a range of services to their customers. These services may include installation, training, maintenance, and repair. Manufacturers understand that their customers need not only high-quality machines but also comprehensive support to ensure that their operations run smoothly.
The steel slitting industry is highly competitive, and manufacturers must constantly innovate and improve their products in order to stay ahead. This has led to the development of new technologies and features, such as automated slitting systems, advanced control systems, and energy-efficient designs. Manufacturers are also exploring new materials and manufacturing processes to improve the performance and durability of their machines.
As the demand for steel products continues to grow, steel slitter manufacturers will play an increasingly important role in meeting the needs of the market. These manufacturers are committed to providing high-quality, reliable machines that can help their customers improve productivity, reduce waste, and increase profitability. With their expertise and innovation, steel slitter manufacturers are driving the future of metal processing.
When choosing a steel slitter manufacturer, it is important to consider several factors. First, look for a manufacturer with a proven track record of quality and reliability. Check their reputation in the industry and read reviews from other customers. Second, consider the manufacturer's range of products and services. Do they offer machines that meet your specific needs? Do they provide installation, training, and maintenance services? Third, look for a manufacturer that is committed to innovation and continuous improvement. Are they investing in research and development to stay ahead of the competition?
In conclusion, steel slitter manufacturers are essential players in the metal fabrication and manufacturing industries. Their expertise and innovation are driving the development of advanced slitting technology, enabling businesses to produce high-quality steel products with precision and efficiency. When choosing a steel slitter manufacturer, it is important to consider factors such as quality, reliability, product range, and innovation to ensure that you get the best possible equipment and support for your operations.
Coil Slitting Machine
Introduction:
In the metal processing industry, the coil slitting machine is a crucial piece of equipment. This specialized machine is designed to cut large coils of metal into narrower strips with precision and efficiency. With the increasing demand for customized metal products in various industries, the importance of a reliable and high-performance coil slitting machine cannot be overstated.
The coil slitting machine combines advanced technology with robust construction to ensure accurate and consistent slitting results. It is capable of handling different types of metals, including steel, aluminum, copper, and stainless steel, as well as various thicknesses and widths of coils. This versatility makes it a valuable tool for a wide range of applications.
Design and Construction:
The design of a coil slitting machine is a complex engineering feat. The machine typically consists of several key components, including a decoiler, a slitting head, a tension control system, a recoiler, and various auxiliary equipment.
The decoiler is responsible for unwinding the metal coil and feeding it into the slitting line. It is designed to handle different coil sizes and weights, and may be equipped with features such as automatic coil loading and unloading systems for increased efficiency.
The slitting head is the heart of the machine. It consists of a set of circular knives or blades that cut the metal coil into narrower strips. The design of the slitting head must ensure accurate and clean cuts, while also being able to handle the hardness and toughness of different metals. Advanced slitting heads may feature adjustable knife spacing, automatic knife sharpening systems, and precision alignment mechanisms to ensure optimal performance.
The tension control system is crucial for maintaining consistent tension on the metal strip throughout the slitting process. This helps to ensure accurate cuts and prevent wrinkling or stretching of the material. The tension control system may consist of tension sensors, brake systems, and motor drives that work together to maintain the desired tension level.
The recoiler is responsible for rewinding the slit metal strips into smaller coils. It must be able to handle the high speeds and tensions generated during the slitting process, and may be equipped with features such as automatic coil changing systems and tension control feedback loops for increased productivity.
In addition to these main components, a coil slitting machine may also include various auxiliary equipment such as conveyors, stackers, and inspection systems. Conveyors are used to transport the metal strip between different stages of the slitting process, while stackers are used to stack the slit coils for easy storage and transportation. Inspection systems may be used to detect defects or irregularities in the metal strip, ensuring that only high-quality products are produced.
The construction of a coil slitting machine is typically made of high-quality materials such as steel and cast iron to ensure durability and stability. The machine is designed to withstand the harsh operating conditions of metal processing, and may be equipped with safety features such as guards, emergency stop buttons, and interlocks to protect operators and prevent accidents.
Slitting Process:
The slitting process using a coil slitting machine typically involves several steps.
1. Coil Loading:
The metal coil is loaded onto the decoiler. The decoiler unwinds the coil and feeds the metal strip into the slitting line.
2. Tension Control:
The tension control system is activated to maintain consistent tension on the metal strip. This helps to ensure accurate cuts and prevent wrinkling or stretching of the material.
3. Slitting:
The metal strip passes through the slitting head, where the circular knives or blades cut it into narrower strips. The slitting head is adjusted to the desired strip width and spacing.
4. Inspection:
The slit metal strips may be inspected for defects or irregularities using inspection systems such as vision systems or ultrasonic detectors. Any defective strips can be removed or marked for further processing.
5. Recoiling:
The slit metal strips are rewound onto smaller coils by the recoiler. The recoiler is adjusted to the desired coil size and tension.
6. Packaging and Storage:
The slit metal coils are packaged and stored for transportation or further processing.
Advantages of Coil Slitting Machines:
1. High Precision:
Coil slitting machines are designed to provide accurate and clean cuts, ensuring consistent strip widths and quality. This is crucial for meeting the strict requirements of different industries.
2. High Efficiency:
These machines are capable of processing high volumes of metal coils at high speeds, significantly increasing production efficiency. The automated nature of the slitting process reduces labor costs and minimizes the risk of human error.
3. Versatility:
Coil slitting machines can handle different types of metals, as well as various thicknesses and widths of coils. They can also be adjusted to produce different strip widths and spacings, providing flexibility in production.
4. Cost-Effective:
By processing large coils of metal into narrower strips, coil slitting machines can reduce material waste and increase efficiency. This can lead to significant cost savings in material procurement and production.
5. Reliability:
Constructed from high-quality materials and equipped with advanced technology, coil slitting machines are built to withstand the harsh operating conditions of metal processing. They are designed for long-term use and require minimal maintenance, ensuring reliable and consistent performance.
Applications:
Coil slitting machines are widely used in various industries for different applications. Some of the common applications include:
1. Automotive Industry:
In the automotive industry, coil slitting machines are used to produce metal strips for body panels, chassis components, and other parts. The high precision and durability of these machines are essential for meeting the strict quality and performance requirements of the automotive industry.
2. Construction Industry:
The construction industry uses coil slitting machines to produce metal strips for roofing, siding, and other building materials. The versatility and cost-effectiveness of these machines make them suitable for various construction applications.
3. Packaging Industry:
In the packaging industry, coil slitting machines are used to produce metal strips for cans, lids, and other packaging materials. The malleability and barrier properties of metals make them an ideal material for packaging applications, and the precision of the slitting process is crucial for ensuring the integrity and functionality of these packaging materials.
4. Electronics Industry:
The electronics industry uses coil slitting machines to produce metal strips for heat sinks, electrical conductors, and other components. The high thermal conductivity and electrical conductivity of metals make them an ideal material for electronics applications, and the precision of the slitting process is crucial for ensuring the performance and reliability of these components.
5. General Manufacturing Industry:
Coil slitting machines are also used in general manufacturing industries for a wide range of applications, such as producing metal strips for machinery parts, furniture components, and decorative items. The versatility and cost-effectiveness of metals make them a valuable material for many manufacturing applications, and the slitting process allows for custom sizes and shapes to meet specific production needs.
Conclusion:
The coil slitting machine is an essential piece of equipment in the metal processing industry. With its advanced technology, robust construction, and high precision, this machine offers a reliable and efficient solution for cutting metal coils into narrower strips. Whether it's for the automotive, construction, packaging, electronics, or general manufacturing industry, the coil slitting machine plays a crucial role in meeting the growing demand for customized metal products. As technology continues to advance, coil slitting machines are likely to become even more efficient and versatile, further enhancing their importance in the industry.