Hotline
+86-136 8495 9862
Email:cennia@szmizhi.com
Add::104,Building 27,Third Industrial Zone, Longxi Community,Longgang District,Shenzhen,China.
Coil Forming & Handling Equipment
Surface Treatment Equipment
Solutions
Application
About Us
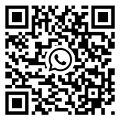
Welcome to MIZHI
For consultation/feedback, please call the service hotline: +86-136 8495 9862 Email:cennia@szmizhi.com
1. Introduction
In the vast and dynamic landscape of the steel - processing industry, steel slitters stand as indispensable machinery. These specialized devices are designed to transform large - width steel coils into precisely cut, narrower strips, catering to the diverse needs of countless downstream applications. Whether it's for the production of automotive components, construction materials, or electrical products, the demand for accurately slit steel strips is ever - present. When considering steel slitters for sale, businesses embark on a journey that involves understanding the technology, evaluating different models, and assessing the long - term benefits and challenges. This exploration is not only about acquiring a piece of equipment but also about investing in a solution that can enhance productivity, reduce costs, and improve product quality.
2. Understanding Steel Slitters: Working Principle and Components
2.1 Decoiling Mechanism
The operation of a steel slitter commences with the decoiling mechanism. This is the initial stage where a large - diameter steel coil is carefully unwound. The decoiling unit consists of a robust expandable mandrel. When the steel coil is loaded onto the mandrel, it expands to firmly grip the inner diameter of the coil. High - torque motors are then engaged to control the speed of unwinding. The ability to adjust the decoiling speed is crucial. For instance, when dealing with thin - gauge steel coils, a slower and more controlled decoiling speed is required to prevent the strip from stretching or wrinkling. In contrast, for thicker steel coils, a higher - speed decoiling might be feasible, but still, it must be carefully monitored to ensure a smooth feed into the subsequent processing stages. Tension control systems are also integrated into the decoiling mechanism. These systems continuously monitor and adjust the tension in the steel strip as it is unwound. Maintaining the right tension is essential as it directly impacts the quality of the slit strips. If the tension is too high, the strip may be over - stressed and prone to breakage, while too low a tension can lead to sagging and uneven feeding, which in turn can cause defects in the slitting process.
2.2 Leveling and Straightening Section
After the steel strip is decoiled, it often has some inherent curvature or irregularities due to the coiling process. The leveling and straightening section of the steel slitter is designed to eliminate these imperfections. This section is composed of a series of precision - ground rolls. The rolls are arranged in a specific pattern, and as the steel strip passes through them, they apply a controlled amount of pressure. The number of rolls, their diameter, and the pressure exerted can be adjusted according to the thickness and type of the steel being processed. For example, when processing thick - gauge carbon steel coils for structural applications, the leveling section may have a larger number of rolls and apply higher pressure to effectively straighten the stiff material. The straightening process is not only about making the strip flat but also about ensuring that it has a consistent cross - sectional shape. This consistency is vital for accurate slitting, as any variations in the strip's shape can lead to inconsistent cut widths and poor - quality slit products.
2.3 Slitting Section
The slitting section is the heart of the steel slitter. Here, the actual cutting of the steel strip into narrower strips takes place. High - precision circular slitting knives are the key components in this section. These knives are typically made from high - quality tool steel, which is heat - treated to achieve exceptional hardness and wear resistance. The knives are mounted on precisely machined arbors. The distance between the knives can be adjusted to achieve the desired strip widths. In modern steel slitters, computer - controlled systems are commonly used to manage the knife - setting process. Operators can input the required strip widths into the control panel, and the system automatically adjusts the positions of the knives with great accuracy. This allows for the production of slit strips with very tight width tolerances, often within ±0.1mm or even less in high - end models. The slitting section also features a high - speed cutting mechanism. The cutting speed can be adjusted based on the thickness and type of the steel. For thinner steel strips, a higher cutting speed may be possible, while thicker steel requires a slower speed to ensure a clean and accurate cut.
2.4 Scrap Rewinding and Strip Winding Units
As the steel strip is slit, the scrap material (the narrow strips that are not part of the final product) needs to be efficiently removed. The scrap rewinding unit in the steel slitter is designed to handle this task. It quickly and neatly winds up the scrap into a coil, which can be easily disposed of or recycled. On the other hand, the strip winding units are responsible for winding the slit strips into individual coils. These units are equipped with advanced tension control systems to ensure that the coils are wound tightly and evenly. The tension control is crucial during the winding process. If the tension is too high, the strip may be stretched or damaged, and if it is too low, the coils may be loose and prone to tangling. The strip winding units can precisely adjust the tension according to the characteristics of the steel strip, ensuring high - quality coil winding.
3. Types of Steel Slitters Available for Sale
3.1 Manual Steel Slitters
Manual steel slitters are the most basic type of slitters available. They are relatively simple in design and operation. These slitters are often suitable for small - scale operations or for businesses with low - volume production requirements. In a manual steel slitter, the operator is responsible for most of the processes, such as adjusting the slitting knives, setting the decoiling speed, and controlling the winding of the slit strips. While they are more affordable compared to their automated counterparts, they require a higher level of manual labor and may not be as precise in terms of cut widths. However, for some small - scale metalworking shops that deal with simple steel - slitting tasks, manual steel slitters can be a cost - effective solution.
3.2 Semi - Automatic Steel Slitters
Semi - automatic steel slitters offer a step up in terms of automation. In these slitters, some of the processes are automated, while others still require manual intervention. For example, the slitting knife adjustment may be automated, allowing the operator to input the desired strip widths into a control panel, and the machine will adjust the knives accordingly. However, the decoiling and winding processes may still require some level of manual control. Semi - automatic steel slitters are a good option for medium - sized businesses that want to increase their productivity without making a significant investment in fully automated equipment. They offer a balance between cost and automation, providing more precision and efficiency compared to manual slitters.
3.3 Fully Automatic Steel Slitters
Fully automatic steel slitters are the pinnacle of slitting technology. These machines are equipped with advanced computer - controlled systems that automate all aspects of the slitting process. From the decoiling of the steel coil to the winding of the slit strips, everything is controlled by the machine's control system. They are capable of high - speed operation and can achieve extremely tight tolerances in cut widths. Fully automatic steel slitters are ideal for large - scale industrial operations with high - volume production requirements. They offer maximum productivity, reduced labor costs, and consistent product quality. However, they also come with a higher price tag and require a more sophisticated infrastructure for installation and maintenance.
4. Applications of Steel Slitters in Different Industries
4.1 Automotive Industry
In the automotive industry, steel slitters play a crucial role in the production of various components. Steel strips produced by slitters are used for manufacturing car body panels, such as doors, hoods, and fenders. The accurate widths and straight edges of the slit strips ensure that the stamped panels fit together perfectly during the assembly process. This not only improves the aesthetics of the vehicle but also enhances its structural integrity and safety. In addition, steel slitters are used to produce metal strips for engine parts, such as gaskets and fuel lines. The high - precision slitting ensures that these components have the correct dimensions, which is essential for the proper functioning of the engine.
4.2 Construction Industry
The construction industry is a major consumer of products processed by steel slitters. Steel sheets are used extensively for roofing, siding, and structural components. For roofing applications, steel slitters can cut steel coils into strips of the exact width required for different roofing systems. This ensures a proper fit and reduces the need for on - site cutting and adjustments. In the case of siding, the precise slitting allows for the production of uniform - sized steel strips that can be easily installed to create a smooth and aesthetically pleasing exterior. For structural components, such as steel beams and columns, steel slitters can cut steel strips that are further processed into channels, angles, and other profiles. The accuracy of the slitting process contributes to the overall strength and stability of the construction structures.
4.3 Electrical and Electronics Industry
In the electrical and electronics industry, steel slitters are used for the production of components such as electrical enclosures, circuit boards, and connectors. For electrical enclosures, steel slitters cut steel strips to the required widths for forming the enclosures. The precise slitting ensures that the enclosures have a tight - fitting and secure design, protecting the electrical components inside. In the production of circuit boards, steel slitters cut steel strips for the manufacturing of conductive traces and other components. The high - precision slitting is essential for ensuring the proper electrical conductivity and functionality of the circuit boards. For connectors, steel slitters cut steel strips into narrow widths that are used to make the contact points. The accuracy of the slitting process ensures that the connectors have a reliable and consistent connection.
5. Advantages of Purchasing Steel Slitters
5.1 Cost - Efficiency in the Long Run
While the initial investment in a steel slitter can be significant, especially for more advanced models, it offers long - term cost - efficiency. By in - house slitting of steel coils, businesses can reduce their dependence on pre - slit steel products from external suppliers. This eliminates the additional costs associated with purchasing pre - slit materials, such as transportation, handling, and the supplier's profit margin. Moreover, the ability to precisely cut the steel according to the exact requirements of the production process reduces material waste. For example, if a business needs steel strips of a specific non - standard width, purchasing pre - slit steel may result in a lot of wasted material. With an in - house steel slitter, the business can cut the steel coils exactly to the required width, minimizing waste and saving on raw material costs.
5.2 Quality Control
Having a steel slitter in - house gives businesses greater control over the quality of the slit steel strips. They can monitor and adjust the slitting process according to their specific quality standards. For example, they can ensure that the cut edges are smooth, the strip widths are consistent, and the steel has no surface defects during the slitting process. This level of quality control is difficult to achieve when relying on external suppliers. In addition, businesses can quickly respond to any quality issues that arise during the slitting process. They can make immediate adjustments to the machine settings or replace worn - out components to ensure that the quality of the slit products remains high.
5.3 Customization and Flexibility
Steel slitters allow businesses to customize the width of the slit steel strips according to their specific production needs. This flexibility is crucial in industries where different products require different - sized steel components. For example, in the manufacturing of metal furniture, the steel strips used for the frames and legs may have different widths. With a steel slitter, the business can easily adjust the slitting process to produce strips of the required widths. This eliminates the need to stock a large inventory of pre - slit steel strips of various widths, as the business can produce the required widths on - demand.
6. Considerations when Buying Steel Slitters
6.1 Production Requirements
Before purchasing a steel slitter, businesses need to carefully assess their production requirements. This includes the volume of steel they need to slit, the types of steel they will be processing (such as carbon steel, stainless steel, or alloy steel), and the range of strip widths they require. For high - volume production, a fully automatic steel slitter may be the best option, as it can handle large - scale operations efficiently. If the business deals with a variety of steel types and widths, a slitter with a wide range of adjustable parameters will be more suitable. On the other hand, for small - scale production with limited types of steel and strip widths, a manual or semi - automatic slitter may be sufficient.
6.2 Budget Constraints
Budget is an important consideration when buying a steel slitter. Manual and semi - automatic slitters are generally more affordable, making them suitable for small and medium - sized businesses with limited budgets. However, if the business has long - term growth plans and high - volume production requirements, investing in a more expensive fully automatic slitter may be a more cost - effective solution in the long run. It's also important to consider the total cost of ownership, which includes not only the purchase price but also the cost of installation, maintenance, and training. Some high - end steel slitters may require specialized installation and maintenance services, which can add to the overall cost.
6.3 Supplier Reputation and After - Sales Support
The reputation of the steel slitter supplier is crucial. A reliable supplier will offer high - quality equipment, provide accurate product information, and offer good after - sales support. After - sales support includes services such as installation, training, and technical assistance. A supplier that offers prompt and efficient after - sales support can help the business quickly resolve any issues that may arise with the steel slitter, minimizing downtime and ensuring smooth production. It's also important to check the availability of spare parts from the supplier. A supplier with a good inventory of spare parts can ensure that the business can quickly replace any worn - out or damaged components, reducing the impact on production.
7. Maintenance and Operation of Steel Slitters
7.1 Regular Maintenance
Regular maintenance is essential to ensure the long - term performance and reliability of a steel slitter. This includes daily visual inspections of the machine for any signs of wear, such as frayed belts, loose bolts, or damaged components. Weekly or monthly inspections should be more comprehensive, including checks of the electrical systems, lubrication levels, and the alignment of the rolls and knives. The slitting knives, in particular, need to be regularly inspected and sharpened or replaced when they become dull. Regular maintenance can prevent unexpected breakdowns, extend the lifespan of the machine, and ensure consistent product quality.
7.2 Operator Training
Well - trained operators are crucial for the efficient and safe operation of a steel slitter. Operators should be trained on the proper startup and shutdown procedures, how to adjust the slitting parameters for different steel types and widths, and how to recognize and address common operational issues. Training should also cover safety protocols, as steel slitters can be dangerous if not operated properly. Some suppliers offer operator training programs as part of their after - sales support, and businesses should take advantage of these programs to ensure that their operators are proficient in using the steel slitter.
7.3 Upgrades and Retrofits
Over time, as technology advances, businesses may consider upgrading or retrofitting their steel slitters. Upgrades can include replacing old - fashioned control systems with modern, more advanced ones, such as programmable logic controllers (PLCs). Retrofits may involve adding new features, such as automated material handling systems or advanced tension control systems. These upgrades and retrofits can enhance the performance of the steel slitter, improve productivity, and reduce operating costs.
8. Future Outlook for Steel Slitters
8.1 Technological Advancements
The future of steel slitters will be shaped by technological advancements. We can expect to see the integration of more advanced artificial intelligence (AI) and machine learning (ML) algorithms. These technologies can enable real - time monitoring of the slitting process, predictive maintenance, and automatic adjustment of cutting parameters based on the characteristics of the incoming steel coils. For example, AI - powered sensors can detect any anomalies in the steel strip, such as thickness variations or surface defects, and automatically adjust the slitting process to compensate for these issues. This will lead to higher - quality slit products and reduced waste.
8.2 Sustainable and Environmentally Friendly Features
As environmental concerns become more prominent, steel slitters will likely incorporate more sustainable and environmentally friendly features. This may include the use of energy - efficient motors and drives, recycling systems for scrap materials, and the reduction of lubricant and coolant usage. For example, some steel slitters may be designed to use water - based lubricants instead of traditional oil - based ones, which are more environmentally friendly. Additionally, more advanced scrap - recycling systems may be developed to ensure that a higher percentage of the scrap steel is recycled, reducing the environmental impact of the steel - slitting process.
8.3 Expansion into New Markets
Steel slitters may also find new applications in emerging markets. With the growth of industries such as renewable energy, 3D printing, and advanced manufacturing, there may be a demand for steel slitters that can process new types of steel materials or meet the specific requirements of these industries. For example, in the renewable energy industry, steel slitters may be used to produce components for wind turbines or solar panels. This expansion into new markets will drive the development of more specialized and versatile steel slitters.
In conclusion, when considering steel slitters for sale, businesses are making a significant investment in their production capabilities. By understanding the technology, applications, advantages, and considerations associated with steel slitters, they can make an informed decision that aligns with their business goals. As technology continues to evolve, steel slitters will play an even more important role in the steel - processing and manufacturing industries, driving innovation, efficiency, and sustainability.