Hotline
+86-136 8495 9862
Email:cennia@szmizhi.com
Add::104,Building 27,Third Industrial Zone, Longxi Community,Longgang District,Shenzhen,China.
Coil Forming & Handling Equipment
Surface Treatment Equipment
Solutions
Application
About Us
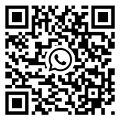
Welcome to MIZHI
For consultation/feedback, please call the service hotline: +86-136 8495 9862 Email:cennia@szmizhi.com
The Innovation of Advanced Materials for Roll Forming
The innovation of advanced materials for roll forming is a significant trend that is reshaping the industry, driven by the need for higher performance, sustainability, and cost-effectiveness. Here are the key advancements and trends in this area:
1. Advanced High-Strength Steels (AHSS) and Aluminum Alloys
The adoption of advanced high-strength steels (AHSS) and aluminum alloys is becoming more prevalent in roll forming. These materials offer superior strength-to-weight ratios, corrosion resistance, and formability, making them ideal for demanding applications in automotive, aerospace, and construction. For example, AHSS is widely used in automotive manufacturing to produce lightweight yet robust structural components.
2. Composite Materials
Composite materials are also gaining traction in roll forming processes. These materials combine different properties (e.g., high strength, low weight, and durability) and can be tailored to meet specific application requirements. The use of composites allows manufacturers to produce components that are not only lighter but also more resistant to wear and environmental damage.
3. Eco-Friendly and Recyclable Materials
Sustainability is a key focus in the roll forming industry, driving the adoption of eco-friendly and recyclable materials. Manufacturers are increasingly using recycled metals and developing new coatings and finishes that are more environmentally friendly. This trend aligns with the growing demand for sustainable manufacturing practices and helps reduce the industry's carbon footprint.
4. Material Processing Innovations
Processing high-strength materials presents challenges such as increased hardness, springback tendencies, and sensitivity to temperature variations. However, innovations in roll forming technology, such as advanced heat treatment methods, precision tooling designs, and process simulation software, are addressing these challenges. By optimizing roll geometry, forming speeds, and cooling strategies, manufacturers can effectively shape high-strength materials without compromising dimensional accuracy.
5. Customization and Specialized Applications
The roll forming industry is increasingly focusing on customized solutions to meet specific customer needs. Advanced materials allow for greater flexibility in designing complex profiles and incorporating specialized finishes. Manufacturers are collaborating closely with material suppliers and end-users to develop innovative solutions that leverage the benefits of advanced materials while ensuring cost-effectiveness.
6. Future Outlook
As material science continues to advance, the roll forming industry will have access to a broader range of high-performance materials. This will enable the production of more robust, lightweight, and sustainable components, catering to the evolving needs of industries such as automotive, aerospace, and construction. Additionally, the integration of AI and data analytics will further enhance material selection and process optimization.
In summary, the innovation of advanced materials for roll forming is driving significant advancements in the industry. By adopting high-strength alloys, composites, and eco-friendly materials, manufacturers can produce higher-quality, more sustainable products while meeting the growing demand for customization and performance.