Hotline
+86-136 8495 9862
Email:cennia@szmizhi.com
Add::104,Building 27,Third Industrial Zone, Longxi Community,Longgang District,Shenzhen,China.
Coil Forming & Handling Equipment
Surface Treatment Equipment
Solutions
Application
About Us
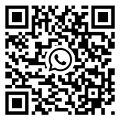
Welcome to MIZHI
For consultation/feedback, please call the service hotline: +86-136 8495 9862 Email:cennia@szmizhi.com
The Use of 3D Printing for Roll Form Tooling
The use of 3D printing for roll form tooling is emerging as a transformative technology in the roll forming industry, offering significant advantages in terms of speed, cost, and design flexibility. Here are the key insights and benefits of using 3D printing for roll form tooling:
1. Rapid Prototyping and Tooling Production
3D printing enables manufacturers to produce roll form tooling and prototypes quickly and cost-effectively. This technology allows for rapid adjustments to tool designs, reducing lead times and speeding up product development. Traditional tooling processes often involve complex and time-consuming steps, whereas 3D printing can produce intricate tool designs directly from CAD models, significantly shortening the production cycle.
2. Customization and Design Flexibility
3D printing offers unparalleled customization capabilities for roll form tooling. Manufacturers can design and produce highly specific tooling that meets precise project requirements without the need for extensive manual adjustments. This flexibility is particularly valuable in industries like aerospace and automotive, where complex geometries and high precision are required.
3. Reduced Costs
By eliminating the need for traditional mold-making processes, 3D printing reduces the costs associated with tooling development. The ability to iterate designs quickly and produce only the required amount of material minimizes waste and lowers overall production costs. Additionally, 3D printing can use a variety of materials, including metal powders and thermoplastics, which further enhances cost-effectiveness.
4. Improved Quality and Consistency
3D-printed tooling can achieve higher precision and consistency compared to traditional methods. The additive manufacturing process ensures that tooling is produced with high accuracy, reducing the likelihood of defects and improving the overall quality of the roll-formed products.
5. Integration with Existing Processes
3D-printed tooling can be seamlessly integrated with existing roll forming processes. This allows manufacturers to leverage the benefits of 3D printing without overhauling their entire production line. For example, 3D-printed molds can be used in conjunction with traditional roll forming machines to enhance production efficiency and flexibility.
6. Applications Across Industries
The use of 3D printing for roll form tooling is gaining traction across various industries, including automotive, aerospace, construction, and consumer electronics. These sectors benefit from the ability to produce lightweight, high-strength components with complex geometries.
7. Future Outlook
As 3D printing technology continues to advance, its application in roll forming is expected to grow. Innovations in materials and printing processes will further enhance the capabilities of 3D-printed tooling, making it an even more attractive option for manufacturers. The integration of AI and data analytics with 3D printing will also enable more efficient production and quality control.
In summary, 3D printing is revolutionizing roll form tooling by offering rapid production, design flexibility, and cost savings. As the technology matures and becomes more accessible, it is poised to play a significant role in the future of the roll forming industry.