Hotline
+86-136 8495 9862
Email:cennia@szmizhi.com
Add::104,Building 27,Third Industrial Zone, Longxi Community,Longgang District,Shenzhen,China.
Coil Forming & Handling Equipment
Surface Treatment Equipment
Solutions
Application
About Us
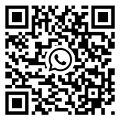
Welcome to MIZHI
For consultation/feedback, please call the service hotline: +86-136 8495 9862 Email:cennia@szmizhi.com
1. Introduction
In the realm of industrial manufacturing, the production of tubular products is a fundamental process that underpins numerous sectors. Tube forming rolls are the unsung heroes in this domain, enabling the transformation of flat sheets or strips of various materials into seamless, precisely shaped tubes. These rolls are utilized in a wide range of industries, from the automotive and aerospace sectors, where tubular components are crucial for engine and structural applications, to the plumbing and construction industries, which rely on tubes for fluid transportation and building frameworks. The design, functionality, and quality of tube forming rolls play a pivotal role in determining the efficiency, accuracy, and cost - effectiveness of tube production.
2. Working Principle of Tube Forming Rolls
2.1 The Forming Process
Tube forming rolls operate based on a sequential bending and shaping principle. The process typically starts with a flat strip of material, such as steel, aluminum, or copper. This strip is fed into a series of roll stands, each equipped with a set of rolls. The rolls in the initial stands are designed to gradually bend the edges of the strip upwards. For instance, in the production of a simple circular tube, the first few roll sets will create a U - shaped profile from the flat strip.
As the strip progresses through the subsequent roll stands, the degree of bending increases. The rolls are carefully designed to ensure that the material is evenly shaped, with consistent pressure applied along the width of the strip. In the case of a circular tube, the rolls in the middle stands will further curve the U - shaped profile towards a more circular shape. The final roll stands are responsible for closing the gap and forming a seamless tube. This is achieved by applying precise pressure to bring the edges of the strip together and, in some cases, welding or joining them to create a continuous tubular structure.
2.2 Role of Different Roll Sets
There are different types of roll sets within the tube - forming system, each with a specific function. The entry rolls, also known as the guide rolls, are the first to interact with the flat strip. Their primary role is to guide the strip into the forming process smoothly, ensuring that it is centered and properly aligned. These rolls help to prevent misalignment, which could lead to uneven forming and defects in the final tube.
The forming rolls are the main components that shape the strip into the desired tube profile. They are designed with specific curvatures and angles that correspond to the cross - sectional shape of the tube. For example, if a square - shaped tube is being produced, the forming rolls will have square - like profiles that gradually bend the strip into the four - sided shape. The number of forming roll sets can vary depending on the complexity of the tube profile and the material being processed.
The sizing rolls, located towards the end of the tube - forming line, are used to fine - tune the dimensions of the tube. They ensure that the tube meets the exact specifications in terms of diameter, wall thickness, and straightness. Sizing rolls can apply a small amount of pressure to correct any minor deviations in the tube's shape and dimensions, resulting in a high - quality final product.
3. Design Considerations for Tube Forming Rolls
3.1 Material - Specific Design
The design of tube forming rolls is highly influenced by the material being processed. Different materials have distinct mechanical properties, such as hardness, ductility, and yield strength. For example, when working with stainless steel, which is relatively hard and has a high yield strength, the rolls need to be made from materials that can withstand the significant forces required for shaping. High - carbon steel alloys or carbide - coated rolls are often used in such cases to ensure durability and long - term performance.
On the other hand, when forming soft materials like some types of aluminum alloys, the roll design can be more delicate. The rolls may have a smoother surface finish to prevent scratching or marring the soft material. Additionally, the forming forces need to be carefully controlled to avoid over - deformation or wrinkling of the aluminum strip.
3.2 Tube Profile Complexity
The complexity of the tube profile is another crucial factor in roll design. Simple circular or rectangular tubes require a relatively straightforward roll design. However, for complex tube profiles, such as those with multiple bends, tapered sections, or non - standard cross - sectional shapes, the roll design becomes much more challenging.
In the case of a tube with a helical shape, the rolls need to be designed to gradually impart the helical twist to the strip as it progresses through the forming process. This requires precise calculation of the roll curvatures, angles, and the sequence of shaping operations. For tubes with internal features, such as corrugations or fins, the roll design must incorporate additional elements to create these features during the forming process.
3.3 Production Volume and Speed
The intended production volume and speed also impact the design of tube forming rolls. For high - volume production runs, the rolls need to be designed for maximum durability and efficiency. This may involve using more expensive, high - quality materials and implementing advanced heat - treatment processes to enhance the roll's wear resistance. The roll design may also be optimized to reduce friction and energy consumption during the forming process, as high - speed production can generate significant heat and stress on the rolls.
If the production speed is high, the roll design must ensure that the material can be formed quickly without sacrificing quality. This may require improving the roll - to - material contact area, reducing the number of forming steps if possible, and ensuring efficient transfer of the forming forces. In some cases, high - speed tube forming may also require additional cooling mechanisms for the rolls to prevent overheating, which can affect the material properties and the accuracy of the forming process.
4. Manufacturing of Tube Forming Rolls
4.1 Precision Machining
Precision machining is the cornerstone of tube forming roll manufacturing. Computer - Numerical - Control (CNC) machining is widely employed due to its ability to achieve extremely high levels of accuracy. CNC mills, lathes, and grinders are used to shape the rolls from raw materials, typically high - quality steel alloys.
The manufacturing process begins with the creation of a detailed design in a CAD (Computer - Aided Design) software. The CAD model serves as a blueprint for the CNC machines, which interpret the design data and precisely cut and shape the roll material. The machining process usually starts with rough cutting to remove the bulk of the excess material. This is followed by fine - finishing operations such as grinding and polishing. Grinding is crucial for achieving the exact surface finish and dimensional tolerances required for the rolls. For example, the surface of the rolls may need to be ground to a roughness of less than 0.8 micrometers to ensure smooth material flow during tube forming.
4.2 Heat Treatment
After machining, tube forming rolls often undergo heat - treatment processes to enhance their mechanical properties. Heat treatment can improve the hardness, toughness, and wear resistance of the rolls. One common heat - treatment process is quenching and tempering. Quenching involves rapidly cooling the heated rolls in a suitable medium, such as oil or water, to increase their hardness. However, quenching can make the rolls brittle, so tempering is carried out to reduce the brittleness and achieve the desired balance of hardness and toughness.
In some cases, surface - hardening treatments like carburizing or nitriding may be applied. Carburizing involves diffusing carbon into the surface layer of the rolls, increasing their surface hardness and wear resistance. Nitriding, on the other hand, involves introducing nitrogen into the surface, which can improve the corrosion resistance and fatigue strength of the rolls. These surface - hardening treatments are particularly beneficial for rolls that are used in high - stress tube - forming applications.
4.3 Assembly and Quality Control
Once the individual roll components are manufactured and heat - treated, they are assembled into a complete roll set. The assembly process requires careful alignment and fastening of the rolls. Precision alignment is crucial to ensure that the rolls work in harmony during the tube - forming process. Any misalignment can lead to uneven shaping of the tube, resulting in defects.
Quality control is an integral part of tube forming roll manufacturing. Dimensional inspection is carried out using precision measuring instruments such as coordinate - measuring machines (CMMs). CMMs can accurately measure the dimensions of the rolls, including their diameters, lengths, and the shape of the forming surfaces, to ensure that they meet the design specifications. Surface finish inspection may also be performed using optical profilometers or other surface - measurement devices. In addition, functional testing of the assembled roll sets may be conducted by running sample strips through a tube - forming machine to verify the accuracy of the tube - forming process.
5. Applications of Tube Forming Rolls
5.1 Automotive Industry
In the automotive industry, tube forming rolls are used to produce a wide range of tubular components. Exhaust systems, which are subjected to high temperatures and corrosive gases, are made from tubes formed using these rolls. The rolls shape the metal strips into the complex bends and shapes required for the exhaust pipes, ensuring proper fitment within the vehicle's chassis.
Automotive chassis components, such as the frame rails and suspension components, often incorporate tubular structures. Tube forming rolls are used to create these components, which need to be strong, lightweight, and have precise dimensions for optimal vehicle performance. For example, the roll - formed tubes used in the suspension system must have consistent wall thickness and straightness to ensure smooth operation and accurate handling of the vehicle.
5.2 Aerospace Industry
The aerospace industry relies heavily on tube forming rolls for the production of critical components. Aircraft engine components, such as the compressor and turbine blades, are often attached to tubular structures. These tubes are formed using rolls to meet the strictest quality and dimensional requirements. The rolls ensure that the tubes have the right shape and strength to withstand the extreme mechanical and thermal stresses experienced during flight.
Aerospace structural components, such as the fuselage frames and wing spars, also use tubular elements. The tube forming rolls are designed to produce high - strength, lightweight tubes made from advanced materials like titanium alloys. These tubes contribute to the overall strength and efficiency of the aircraft, while also reducing its weight, which is crucial for fuel efficiency and performance.
5.3 Construction and Plumbing Industries
In the construction industry, tube forming rolls are used to produce a variety of products. Steel tubes for building frameworks, such as those used in high - rise buildings and industrial structures, are formed using these rolls. The rolls shape the steel strips into the required cross - sectional shapes, such as circular, rectangular, or square, depending on the structural requirements.
In the plumbing industry, copper and plastic tubes are commonly used for water supply and drainage systems. Tube forming rolls are used to produce these tubes, ensuring that they have the right dimensions and smooth interior surfaces for efficient water flow. The rolls can also be used to create tubes with specific fittings or joints, such as threaded ends or compression fittings, which are essential for easy installation and connection in plumbing systems.
6. Advantages of Tube Forming Rolls
6.1 High - Volume, Cost - Effective Production
Tube forming rolls are well - suited for high - volume production. Once the roll sets are properly installed and the tube - forming process is optimized, the production line can operate continuously, producing a large number of tubes in a relatively short time. The cost per unit of production is relatively low, especially when compared to other manufacturing methods like casting or machining for tubular products. This is because the roll - forming process requires less material waste, as the flat strip is gradually shaped without significant material removal.
6.2 High Dimensional Accuracy
Tube forming rolls can achieve a high degree of dimensional accuracy. The precision machining of the rolls and the careful control of the forming process ensure that the tubes produced have consistent diameters, wall thicknesses, and straightness. For example, in the production of tubes for the medical industry, where tight tolerances are crucial for proper functioning, tube forming rolls can be designed to produce tubes with dimensional tolerances in the range of ±0.05mm or even less. This accuracy is essential for ensuring the proper fit and function of the tubes in the final products.
6.3 Versatility in Material and Tube Shapes
Tube forming rolls can be used with a wide variety of materials, including metals (such as steel, aluminum, copper, and titanium), plastics, and even some composite materials. This versatility allows manufacturers to produce tubes for different applications and industries. Moreover, the rolls can be designed to create a vast range of tube shapes, from simple circular and rectangular tubes to complex, custom - designed profiles. This makes tube forming rolls a preferred method for producing tubes with unique shapes that may be difficult to achieve using other manufacturing techniques.
6.4 Energy - Efficient Process
The tube - forming process using rolls is relatively energy - efficient. Since the material is gradually formed through a series of rolling operations, it requires less energy compared to processes that involve high - force impact or extensive material removal, such as forging or machining. This energy efficiency not only reduces the production cost but also has a positive environmental impact by minimizing the overall energy consumption of the manufacturing process.
7. Challenges and Solutions in Tube Forming Roll Usage
7.1 Roll Wear and Maintenance
One of the primary challenges in using tube forming rolls is roll wear. The continuous contact between the rolls and the material, especially when processing hard materials or at high production speeds, can cause the rolls to wear out over time. Worn - out rolls can lead to inconsistent tube shapes, surface defects, and increased scrap rates.
To address this issue, regular maintenance of the tube forming rolls is essential. This includes periodic inspection of the rolls for signs of wear, such as grooves, scratches, or uneven surfaces. When wear is detected, the rolls can be re - ground or replaced. Using high - quality, wear - resistant materials for the rolls, such as carbide - coated steel, can significantly extend the roll's lifespan. In addition, implementing proper lubrication systems during the tube - forming process can reduce friction and wear between the rolls and the material.
7.2 Material Variability
Material variability can pose significant challenges in tube forming. Different batches of the same material may have slightly different mechanical properties, such as thickness variations, differences in yield strength, or variations in surface finish. These variations can affect the tube - forming process, leading to inconsistent tube shapes, wrinkles, or even material failure during forming.
To overcome material variability, manufacturers can implement strict quality control measures for the incoming raw materials. This may include measuring the thickness, mechanical properties, and surface finish of each batch of material before processing. In addition, modern tube - forming machines can be equipped with sensors that can detect the material properties in - line and adjust the tube - forming process parameters, such as the forming force and speed, to compensate for the material variations.
7.3 Design Complexity for New Tube Profiles
Designing tube forming rolls for new or complex tube profiles can be a daunting task. It requires a deep understanding of material behavior, mechanical engineering principles, and the tube - forming process itself. The design process may involve multiple iterations and simulations to ensure that the rolls can successfully form the desired tube profile.
To simplify the design process for new tube profiles, manufacturers can use advanced computer - aided engineering (CAE) software. CAE software can simulate the tube - forming process, predicting the material flow, stress distribution, and potential forming defects. This allows designers to optimize the roll design before manufacturing, reducing the risk of costly design errors and improving the overall efficiency of the roll - development process.
8. Future Trends in Tube Forming Roll Technology
8.1 Advanced Materials for Roll Construction
The future of tube forming rolls may witness the use of more advanced materials for roll construction. Nanocomposite materials, for example, offer the potential for improved wear resistance, strength, and toughness. These materials can be engineered at the nanoscale to have unique properties that can significantly enhance the performance of tube forming rolls. In addition, the development of new, high - performance coatings for roll components can further improve their durability and resistance to corrosion and wear.
8.2 Integration of Smart Technologies
Tube forming rolls are likely to become more integrated with smart technologies in the future. Sensors can be embedded in the roll components to monitor various parameters, such as the temperature, pressure, and wear of the rolls. This real - time data can be used to optimize the tube - forming process, predict maintenance needs, and ensure the quality of the produced tubes. In addition, the integration of artificial intelligence and machine learning algorithms can analyze the sensor data and automatically adjust the tube - forming process parameters to achieve the best possible results.
8.3 Sustainable Manufacturing Practices
As environmental concerns become more prominent, the tube - forming roll industry is likely to adopt more sustainable manufacturing practices. This may include the use of recycled materials for roll construction, reducing energy consumption during the roll - manufacturing process, and optimizing the tube - forming process to minimize material waste. In addition, the development of water - based lubricants or dry - forming techniques can reduce the environmental impact of the tube - forming process.
In conclusion, tube forming rolls are essential tools in the manufacturing of tubular products across a wide range of industries. Their ability to efficiently and accurately shape various materials into precise tube profiles makes them invaluable. While there are challenges associated with their use, ongoing technological advancements and innovative solutions are continuously improving their performance and capabilities. As industries continue to evolve, tube forming rolls will play an increasingly important role in driving efficient, sustainable, and high - quality manufacturing processes.