Hotline
+86-136 8495 9862
Email:cennia@szmizhi.com
Add::104,Building 27,Third Industrial Zone, Longxi Community,Longgang District,Shenzhen,China.
Coil Forming & Handling Equipment
Surface Treatment Equipment
Solutions
Application
About Us
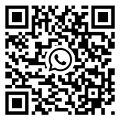
Welcome to MIZHI
For consultation/feedback, please call the service hotline: +86-136 8495 9862 Email:cennia@szmizhi.com
Tumble blasting machines are designed for high-volume surface treatment of small to medium-sized parts, offering automated efficiency for deburring, descaling, and surface finishing. These machines use a rotating drum (tumble barrel) to agitate components while abrasive media is blasted at high pressure, ensuring uniform coverage on all surfaces. This batch-processing method is widely used in automotive, aerospace, and hardware industries to process parts like gears, fasteners, castings, and stamped components.
The tumble blasting process begins by loading parts into the drum, which rotates or tumbles to expose each component to the abrasive stream. Media options include steel shot, grit, glass beads, or plastic pellets, chosen based on the desired finish and material hardness. For example, steel shot is effective for removing heavy rust from cast iron parts, while plastic media is gentler for deburring aluminum or zinc components without causing scratching. The drum’s motion ensures that even intricate or hard-to-reach areas are treated, eliminating the need for manual handling.
One of the primary benefits of tumble blasting is its ability to process hundreds of parts simultaneously, significantly reducing labor costs compared to manual blasting. The automated system also ensures consistent results, as blasting parameters (e.g., pressure, media type, cycle time) can be precisely controlled. Additionally, many tumble blasters feature built-in dust collection systems, improving workplace safety and compliance with environmental regulations.
However, tumble blasting is best suited for parts that can withstand the mechanical agitation of the drum. Fragile or delicate components may require alternative methods like vibratory finishing. Maintenance is also crucial to prevent media buildup and wear on drum linings, which can affect part quality over time. Modern tumble blasting machines often incorporate advanced features such as programmable cycles, quick-change media hoppers, and automatic loading/unloading systems, further enhancing productivity for high-volume operations.
In applications ranging from automotive component manufacturing to jewelry polishing, tumble blasting machines deliver reliable, cost-effective surface treatment at scale. Their combination of automation, versatility, and precision makes them a cornerstone of mass finishing processes worldwide.