Hotline
+86-136 8495 9862
Email:cennia@szmizhi.com
Add::104,Building 27,Third Industrial Zone, Longxi Community,Longgang District,Shenzhen,China.
Coil Forming & Handling Equipment
Surface Treatment Equipment
Solutions
Application
About Us
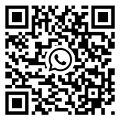
Welcome to MIZHI
For consultation/feedback, please call the service hotline: +86-136 8495 9862 Email:cennia@szmizhi.com
1. Introduction
In the dynamic landscape of metal processing industries, slitting lines play a fundamental role in transforming large - width metal coils into narrower strips. A used slitting line can be a cost - effective solution for businesses looking to enter the metal - slitting market or expand their existing operations. These lines are a collection of integrated machinery and systems that work in harmony to perform the precise task of splitting metal coils according to specific width requirements. Whether it's for the production of components in the automotive, construction, or electrical industries, the proper functioning of a slitting line is crucial, and a used one can offer significant value if evaluated and maintained correctly.
2. Components and Working Principle
2.1 Decoiling Unit
The operation of a slitting line begins with the decoiling unit. In a used slitting line, this unit is responsible for unwinding the large - diameter metal coil. It consists of a sturdy mandrel that expands to grip the inner diameter of the coil firmly. Motors and drive systems are attached to the mandrel to control the unwinding speed. In well - maintained used lines, the decoiling speed can be adjusted smoothly to ensure a continuous and even feed of the metal strip into the subsequent processing stages. This is essential as any irregularities in the decoiling process, such as uneven tension or sudden stops, can lead to defects in the slit strips, like waviness or inconsistent widths.
2.2 Leveling and Straightening Section
After decoiling, the metal strip often has some curvature or irregularities due to the coiling process. The leveling and straightening section in a used slitting line is designed to eliminate these imperfections. This section typically contains a series of rolls arranged in a specific pattern. The rolls apply controlled pressure to the metal strip, gradually flattening it and making it suitable for accurate slitting. In older or used slitting lines, the condition of these rolls is crucial. Worn - out or misaligned rolls can result in an unevenly straightened strip, which will, in turn, affect the quality of the slitting operation. Regular inspection and, if necessary, replacement of the leveling rolls are essential maintenance tasks for a used slitting line.
2.3 Slitting Section
The heart of the slitting line is the slitting section. Here, the metal strip is cut into multiple narrower strips. The slitting process is carried out using circular slitting knives. These knives are mounted on arbors, and the distance between the knives can be adjusted to achieve the desired strip widths. In a used slitting line, the quality of the slitting knives is a key factor. Dull or damaged knives can cause burrs on the edges of the slit strips, reduce the cutting accuracy, and even lead to breakage of the strip during slitting. The arbors also need to be in good condition, with proper alignment and minimal run - out to ensure consistent and precise slitting.
2.4 Scrap Rewinding and Strip Winding Units
As the metal strip is slit, the scrap material (the narrow strips that are not part of the final product) needs to be removed. The scrap rewinding unit in a used slitting line takes care of this task. It winds up the scrap into a coil for easy disposal or recycling. On the other hand, the strip winding units are responsible for winding the slit strips into individual coils. These units need to apply the right amount of tension during the winding process to ensure that the coils are wound tightly and evenly. In a used slitting line, the tension control mechanisms of these winding units may require calibration and adjustment to achieve the desired winding quality.
3. Applications of Used Slitting Lines
3.1 Automotive Industry
In the automotive industry, used slitting lines can be a valuable asset. Many automotive components, such as body panels, engine parts, and chassis components, are made from metal sheets. These sheets are often slit into specific widths to match the requirements of the manufacturing processes. For example, the metal strips used for stamping door panels or hoods need to be of precise widths. A used slitting line can provide the necessary precision in slitting the metal coils, enabling automotive manufacturers to produce high - quality components at a reduced cost. By using a used slitting line, smaller automotive parts suppliers can also enter the market and compete more effectively, as the initial investment in equipment is lower compared to purchasing a new slitting line.
3.2 Construction Industry
The construction industry is another major consumer of slit metal products. Metal sheets are used for roofing, siding, and structural components. A used slitting line can be used to slit metal coils into widths suitable for these applications. For instance, the metal strips for roofing are typically slit to standard widths that are easy to install and provide proper coverage. In the case of structural components, the slit metal strips can be further processed into channels, angles, or other profiles. The ability to slit metal coils in - house using a used slitting line allows construction material manufacturers to have more control over the production process, reduce lead times, and potentially lower costs.
3.3 Electrical and Electronics Industry
In the electrical and electronics industry, metal strips are used for various purposes, such as in the production of electrical enclosures, circuit boards, and connectors. A used slitting line can be used to slit metal coils into the narrow widths required for these applications. For example, the metal strips used for making connectors need to be of very precise widths to ensure proper fit and electrical conductivity. The slitting process in a used slitting line, when properly maintained, can meet these high - precision requirements, enabling electronics manufacturers to produce components with consistent quality.
4. Advantages of Investing in a Used Slitting Line
4.1 Cost - Effectiveness
One of the most significant advantages of a used slitting line is the cost savings. New slitting lines can be extremely expensive, especially for high - capacity and high - precision models. A used slitting line, on the other hand, can be purchased at a fraction of the cost of a new one. This makes it an attractive option for small and medium - sized enterprises (SMEs) that may have budget constraints but still want to enter the metal - slitting business or expand their existing operations. The lower initial investment also means that the return on investment (ROI) can be achieved more quickly, as the revenue generated from the slitting operations can start covering the cost of the equipment sooner.
4.2 Proven Technology
Used slitting lines have already been in operation, which means that their technology and performance have been tested in real - world applications. By purchasing a used slitting line from a reliable source, the buyer can have some confidence in the equipment's capabilities. There may be a wealth of operational data available from the previous owner, which can be used to assess the line's performance, maintenance requirements, and potential areas for improvement. This is in contrast to new, untested models where the buyer may have to rely solely on the manufacturer's specifications and marketing claims.
4.3 Shorter Delivery Times
When purchasing a new slitting line, there is often a significant lead time involved in manufacturing, shipping, and installation. In contrast, a used slitting line can be acquired and put into operation much more quickly. Once the used slitting line is identified and purchased, it can be transported to the buyer's facility and installed with relative ease, depending on its condition. This shorter delivery time allows businesses to start their slitting operations sooner, reducing the time to market for their products and potentially increasing their competitiveness.
5. Challenges and Considerations when Buying a Used Slitting Line
5.1 Equipment Condition
The condition of a used slitting line is a major concern. Over time, the components of the slitting line, such as the decoiling motors, slitting knives, and leveling rolls, can experience wear and tear. Worn - out components can lead to poor - quality slitting, increased downtime, and higher maintenance costs. It is essential to conduct a thorough inspection of the used slitting line before purchase. This inspection should include a visual examination of all components, testing of the electrical and mechanical systems, and, if possible, a trial run of the line with sample metal coils. Hiring an experienced technician or inspector to assess the equipment can be a wise investment to avoid purchasing a line with significant hidden problems.
5.2 Compatibility and Upgradability
Another consideration is the compatibility of the used slitting line with the buyer's existing operations and future expansion plans. The line may need to be integrated with other equipment, such as coil handling systems or downstream processing machinery. Additionally, the buyer may want to upgrade the slitting line in the future to improve its performance or add new features. It is important to ensure that the used slitting line has a modular design or is otherwise adaptable to such upgrades. Checking the availability of spare parts and the manufacturer's support for the model of the used slitting line is also crucial, as this will affect the long - term operability and maintenance of the equipment.
5.3 Maintenance and Support
Maintaining a used slitting line can be more challenging than maintaining a new one. The previous owner may not have followed the recommended maintenance schedule, or the equipment may have been modified in ways that are not immediately apparent. Finding reliable sources of spare parts can also be a problem, especially for older models. Before purchasing a used slitting line, the buyer should research the availability of maintenance services, spare parts, and technical support. This may involve contacting the original manufacturer, third - party service providers, or other users of the same model of slitting line.
6. Maintenance and Optimization of Used Slitting Lines
6.1 Regular Inspection and Preventive Maintenance
To ensure the long - term performance of a used slitting line, regular inspection and preventive maintenance are essential. This includes daily visual inspections of the equipment for any signs of wear, such as frayed belts, loose bolts, or damaged components. Weekly or monthly inspections should be more comprehensive, including checks of the electrical systems, lubrication levels, and the alignment of the rolls and knives. Preventive maintenance tasks, such as replacing worn - out parts before they fail, lubricating moving parts, and calibrating sensors and controls, can significantly reduce the risk of unexpected breakdowns and improve the overall efficiency of the slitting line.
6.2 Upgrading and Retrofit
Upgrading a used slitting line can enhance its performance and extend its useful life. This may involve replacing old - fashioned control systems with modern, programmable logic controllers (PLCs) for better precision and ease of operation. Upgrading the slitting knives to higher - quality, more durable models can also improve the cut quality and reduce the frequency of knife replacements. Retrofitting the line with new sensors for better tension control or strip - edge detection can further optimize the slitting process and minimize waste.
6.3 Operator Training
Well - trained operators are crucial for the efficient operation of a used slitting line. Operators should be trained on the proper startup and shutdown procedures, how to adjust the slitting parameters for different metal types and widths, and how to recognize and address common operational issues. Regular training sessions can also keep operators updated on the latest maintenance and safety practices, ensuring that the slitting line is operated in a safe and efficient manner.
7. Future Outlook for Used Slitting Lines
7.1 Technological Advancements
As new technologies continue to emerge, used slitting lines can also benefit from retrofitting and upgrades. For example, the integration of artificial intelligence (AI) and machine learning (ML) algorithms into slitting lines can enable real - time monitoring of the slitting process, predictive maintenance, and automatic adjustment of cutting parameters based on the characteristics of the incoming metal coils. The development of more advanced materials for slitting knives and rolls can also improve the performance and durability of used slitting lines, allowing them to handle a wider range of metal types and thicknesses with greater precision.
7.2 Market Trends
The demand for slit metal products is expected to remain strong in the coming years, driven by growth in industries such as automotive, construction, and electronics. This will create opportunities for businesses that own used slitting lines. However, competition will also increase, and companies will need to continuously optimize their operations and improve the quality of their slit products. The used slitting line market may also see an increase in the availability of refurbished or remanufactured lines, which offer a balance between cost - effectiveness and performance.
In conclusion, a used slitting line can be a valuable investment for businesses in the metal - processing industry. While there are challenges associated with purchasing and maintaining a used slitting line, the cost - savings, proven technology, and shorter delivery times can make it a viable option. With proper inspection, maintenance, and potential upgrades, a used slitting line can provide reliable and efficient service, enabling businesses to meet the growing demand for slit metal products in a cost - effective manner. As technology advances and market trends evolve, the role of used slitting lines in the metal - processing landscape is likely to become even more significant.