Hotline
+86-136 8495 9862
Email:cennia@szmizhi.com
Add::104,Building 27,Third Industrial Zone, Longxi Community,Longgang District,Shenzhen,China.
Coil Forming & Handling Equipment
Surface Treatment Equipment
Solutions
Application
About Us
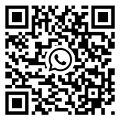
Welcome to MIZHI
For consultation/feedback, please call the service hotline: +86-136 8495 9862 Email:cennia@szmizhi.com
Introduction:
In the world of industrial manufacturing, a used slitting line can be a valuable asset for businesses looking to expand their production capabilities or upgrade their existing equipment without breaking the bank. A used slitting line offers several advantages, including cost savings, quick installation, and the opportunity to obtain a reliable piece of equipment that has already been tested in a production environment.
The slitting line is a crucial piece of machinery in various industries, such as metalworking, packaging, and printing. It is used to cut large rolls of material, such as metal sheets, plastic films, or paper, into narrower strips of specific widths. This process is essential for producing a wide range of products, from automotive parts to packaging materials.
When considering the purchase of a used slitting line, it is important to understand the different components and features of these machines, as well as the factors to consider when evaluating a used equipment option. This article will provide an in-depth look at used slitting lines for sale, including their design, operation, advantages, and considerations for potential buyers.
Design and Components of a Slitting Line:
A slitting line typically consists of several key components, including a decoiler, a slitting head, a tension control system, a recoiler, and various auxiliary equipment.
The decoiler is used to unwind the large roll of material and feed it into the slitting line. It is usually equipped with a braking system to control the speed of the unwind and ensure a smooth feeding process.
The slitting head is the heart of the slitting line. It contains a set of circular knives or blades that cut the material into narrower strips. The slitting head can be adjusted to different widths and spacings to meet the specific requirements of the production process.
The tension control system is essential for maintaining a consistent tension on the material throughout the slitting process. This helps to ensure accurate cuts and prevent wrinkling or stretching of the material. The tension control system may include tension sensors, brake systems, and motor drives.
The recoiler is responsible for rewinding the slit strips into smaller rolls. It must be able to handle the high speeds and tensions generated during the slitting process and may be equipped with features such as automatic coil changing and tension control feedback loops.
In addition to these main components, a slitting line may also include various auxiliary equipment, such as conveyors, stackers, and inspection systems. Conveyors are used to transport the material between different stages of the slitting process, while stackers are used to stack the slit rolls for easy storage and transportation. Inspection systems may be used to detect defects or irregularities in the material and ensure the quality of the final product.
Operation of a Slitting Line:
The operation of a slitting line involves several steps. First, the large roll of material is loaded onto the decoiler. The decoiler unwinds the material and feeds it into the slitting head. The slitting head cuts the material into narrower strips according to the preset widths and spacings.
As the material passes through the slitting head, the tension control system maintains a consistent tension on the material. This is crucial for ensuring accurate cuts and preventing wrinkling or stretching of the material.
After being slit, the strips are rewound onto the recoiler. The recoiler must be able to handle the high speeds and tensions generated during the slitting process and ensure that the slit rolls are wound tightly and evenly.
Throughout the slitting process, various inspection systems may be used to monitor the quality of the material and detect any defects or irregularities. This helps to ensure that only high-quality products are produced.
Advantages of Buying a Used Slitting Line:
1. Cost Savings:
One of the main advantages of buying a used slitting line is the significant cost savings compared to purchasing a new machine. Used equipment can often be obtained at a fraction of the cost of a new slitting line, allowing businesses to expand their production capabilities without a large capital investment.
2. Quick Installation:
Since used slitting lines have already been assembled and tested in a production environment, they can often be installed and commissioned more quickly than new equipment. This can help businesses get up and running faster and start generating revenue sooner.
3. Proven Performance:
A used slitting line has already been used in a production environment, which means that its performance and reliability have been tested. This can give potential buyers more confidence in the equipment and reduce the risk of unexpected problems or downtime.
4. Availability:
Used slitting lines are often more readily available than new equipment. This can be especially beneficial for businesses that need to expand their production capabilities quickly or those that have specific requirements that may not be met by new machines currently on the market.
Considerations When Buying a Used Slitting Line:
1. Condition and Maintenance History:
When considering a used slitting line, it is important to assess its condition and maintenance history. Look for signs of wear and tear, such as damaged components or excessive corrosion. Also, ask for documentation of any maintenance or repairs that have been performed on the equipment.
2. Compatibility with Production Requirements:
Make sure that the used slitting line is compatible with your production requirements. Consider factors such as the material types and thicknesses that the machine can handle, the maximum width and speed of the slitting process, and any specific features or options that you may need.
3. Seller Reputation:
Buying from a reputable seller is crucial when purchasing used equipment. Look for sellers with a proven track record of providing high-quality used machinery and excellent customer service. Check reviews and references from previous customers to ensure that you are dealing with a reliable seller.
4. Installation and Support:
Consider the installation and support options offered by the seller. Some sellers may provide installation services or technical support to help you get the used slitting line up and running smoothly. Make sure that you understand what support is available and what the costs may be.
5. Future Upgrades and Maintenance:
Think about the potential for future upgrades and maintenance of the used slitting line. Consider whether the machine can be easily upgraded to meet changing production requirements and whether spare parts and service support are readily available.
Conclusion:
A used slitting line can be a valuable investment for businesses in various industries. By carefully considering the condition, compatibility, seller reputation, installation support, and future upgrade potential, businesses can find a used slitting line that meets their production needs and provides cost savings and reliable performance. Whether you are looking to expand your production capabilities or replace an existing machine, a used slitting line may be the right choice for your business.
The price of a steel coil slitting machine can vary significantly depending on several factors:
1. Machine Type and Functionality
Basic Manual Machines: These are the most simple and least expensive type. They may have basic slitting capabilities and require more manual operation and adjustment. Their price can range from a few thousand dollars to around $10,000. For example, a basic small-scale steel coil slitting machine for light-duty applications might cost between $3,000 and $5,000. If it has slightly better features like a more stable frame and easier blade adjustment, the price could go up to around $8,000 to $10,000.
Semi-Automatic Machines: These offer more functionality and some degree of automation, such as automatic coil feeding and tension control to a certain extent. The price for semi-automatic steel coil slitting machines typically starts from around $10,000 and can go up to $30,000 or more. For instance, a mid-range semi-automatic slitting machine with reliable feeding and tension control systems, suitable for medium-scale production, might cost around $20,000 to $25,000.
Fully Automatic Machines: These are the most advanced and high-performance machines, capable of fully automated operation, including precise slitting, automatic material handling, and advanced control systems. The price of fully automatic steel coil slitting machines can range from $30,000 to several hundred thousand dollars. A high-quality fully automatic slitting machine for large-scale industrial production with high-speed operation and excellent precision could cost anywhere from $50,000 to $100,000 or even more for top-of-the-line models.
2. Slitting Capacity and Specifications
Coil Width and Thickness: Machines that can handle wider and thicker steel coils generally cost more. For example, a slitting machine capable of handling steel coils up to 1 meter in width and with a moderate thickness range might cost around $20,000. If the machine is designed to handle coils up to 2 meters in width and can handle thicker materials, the price could increase to $30,000 or more.
Slitting Speed and Precision: Machines with higher slitting speeds and better precision also come at a higher price. A machine with a relatively lower slitting speed but acceptable precision might be priced at $15,000, while a machine with extremely high slitting speed and very high precision, which is required in some high-demanding industries like aerospace or automotive, could cost $50,000 or more.
Power Requirements: Machines with higher power requirements to drive the slitting process and other functions will have a higher price tag. A machine with a lower power motor might cost less, but it may not be suitable for heavy-duty or continuous operation. A slitting machine with a powerful motor to ensure efficient and stable operation can add several thousand dollars to the price.
3. Manufacturer and Brand
Well-Known Brands: Established and well-known manufacturers with a good reputation for quality and reliability often charge a premium for their steel coil slitting machines. Brands that have a long history of manufacturing and have a proven track record in the industry may offer machines at a higher price but also provide better after-sales service and support. For example, machines from a renowned international brand could cost 20% to 30% more than those from a less-known manufacturer.
Regional Manufacturers: Manufacturers from different regions may offer machines at different price ranges due to differences in production costs, technology, and quality standards. Machines from developed regions like Europe or North America may be more expensive due to advanced technology and high-quality materials, while machines from some emerging manufacturing regions may offer more competitive prices but may vary in terms of quality and performance.
4. Additional Features and Accessories
Blade Quality and Types: High-quality blades that are durable and can maintain sharpness for a long time are more expensive. Specialized blades for specific materials or applications, such as blades for stainless steel or high-strength steel, can also increase the price. The cost of replacing blades over time should also be considered when evaluating the overall cost of the machine.
Control Systems: Advanced control systems, such as programmable logic controllers (PLCs) and touchscreen interfaces for easy operation and precise control, can add to the cost of the machine. A machine with a basic control system might be priced lower, but a machine with a sophisticated control system that offers more functionality and better control accuracy will be more expensive.
Safety Features: Machines equipped with comprehensive safety features, such as emergency stop buttons, safety guards, and sensors to detect faults and ensure operator safety, may have a higher price. However, these safety features are essential for preventing accidents and ensuring the safe operation of the machine.
The price of a coil slitting machine can vary significantly depending on several factors. Here is an in-depth analysis of the price range and the factors influencing it:
1. Type and Functionality of the Machine
Basic Manual Coil Slitting Machines: These are relatively simple machines that require more manual operation. They are suitable for small-scale operations or businesses with lower production demands. The price of a basic manual coil slitting machine can range from a few thousand dollars to around $20,000. For example, a small manual coil slitting machine for processing thin metal sheets might cost around $5,000 to $10,000, while a slightly more advanced model with better build quality and more functions could cost up to $20,000.
Semi-Automatic Coil Slitting Machines: These machines offer a combination of manual and automatic operations, providing greater efficiency and accuracy compared to manual ones. The price of semi-automatic coil slitting machines typically ranges from $20,000 to $50,000. For instance, a semi-automatic machine for slitting plastic films or thinner metal coils could cost around $25,000 to $35,000, while a machine with higher precision and a wider range of processing capabilities for medium-thickness materials might cost up to $50,000.
Fully Automatic Coil Slitting Machines: These are highly advanced machines that offer fully automated operation, high processing speed, and excellent precision. They are suitable for large-scale industrial production. The price of fully automatic coil slitting machines can range from $50,000 to several hundred thousand dollars or even more. For example, a high-quality fully automatic coil slitting machine for processing heavy-duty steel coils could cost over $200,000, while a machine for slitting high-precision electronic materials might cost around $100,000 to $150,000.
2. Processing Capacity and Specifications
Material Thickness and Width: The ability of the coil slitting machine to process different thicknesses and widths of materials has a significant impact on its price. Machines that can handle thicker materials or wider coils generally require more powerful motors, stronger mechanical structures, and advanced control systems, which increase the cost. For example, a coil slitting machine that can process materials up to 5 mm in thickness and has a wide coil width of 2 meters might cost twice as much as a machine that can only handle materials up to 2 mm in thickness and has a narrower coil width of 1 meter.
Processing Speed: The processing speed of the coil slitting machine is another important factor. Machines with higher processing speeds can complete more work in a shorter time, increasing production efficiency. However, achieving higher processing speeds requires more advanced technology and better components, which also drive up the price. A coil slitting machine with a high processing speed of over 100 meters per minute could cost 50% more than a machine with a moderate processing speed of around 50 meters per minute.
Coil Weight and Diameter: The weight and diameter of the coils that the machine can handle also affect the price. Machines that are designed to handle heavier and larger diameter coils need to have stronger frames, more powerful drive systems, and larger workspaces, which add to the manufacturing cost. For instance, a coil slitting machine that can handle coils weighing up to 10 tons and with a diameter of 3 meters will be more expensive than a machine that is suitable for smaller and lighter coils.
3. Brand and Manufacturer
Well-Known Brands: Established and well-known brands in the coil slitting machine industry often command higher prices due to their reputation for quality, reliability, and after-sales service. These brands have invested a lot in research and development, manufacturing processes, and quality control, ensuring that their machines perform well and have a longer lifespan. For example, machines from renowned international brands might cost 20% to 30% more than those from less-known domestic brands, but they offer better performance and durability.
Manufacturing Location: The location of the manufacturer can also influence the price. Machines manufactured in developed countries with high labor costs and strict quality standards tend to be more expensive than those from developing countries. However, machines from developing countries may have lower prices but might require more attention to quality and after-sales service. For instance, a coil slitting machine made in Europe or the United States could cost significantly more than a similar machine made in China or India, but it may come with more advanced technology and better quality assurance.
4. Additional Features and Accessories
Control Systems: Advanced control systems, such as PLC (Programmable Logic Controller) control and touchscreen interfaces, offer easier operation, better control accuracy, and more functionality. Machines with these advanced control systems are generally more expensive. A coil slitting machine with a basic control system might cost $30,000, while a machine with a high-end PLC control system and a touchscreen interface could cost $40,000 or more.
Cutting Tools and Blades: The quality and type of cutting tools and blades used in the coil slitting machine also affect the price. High-quality blades made of special materials, such as tungsten carbide or high-speed steel, have better cutting performance and longer service life but cost more. Additionally, some machines may offer interchangeable blades or multiple cutting heads for different cutting requirements, which also add to the cost. For example, a set of high-quality cutting blades for a coil slitting machine could cost several thousand dollars.
Safety Features: Machines with comprehensive safety features, such as emergency stop buttons, safety guards, and sensor systems to prevent accidents, are more expensive. These safety features are essential for ensuring the safety of operators and reducing the risk of workplace accidents. A coil slitting machine with basic safety features might cost $25,000, while a machine with advanced safety systems could cost $30,000 or more.