Hotline
+86-136 8495 9862
Email:cennia@szmizhi.com
Add::104,Building 27,Third Industrial Zone, Longxi Community,Longgang District,Shenzhen,China.
Coil Forming & Handling Equipment
Surface Treatment Equipment
Solutions
Application
About Us
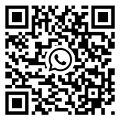
Welcome to MIZHI
For consultation/feedback, please call the service hotline: +86-136 8495 9862 Email:cennia@szmizhi.com
The Wheelabrator machine is a highly efficient and advanced piece of equipment widely used in various industries for surface preparation and finishing. With its innovative design and powerful performance, it has become a staple in many manufacturing processes. In this article, we will explore the features, applications, and benefits of the Wheelabrator machine.
I. History and Background
The Wheelabrator brand has a long and rich history in the field of surface preparation. Founded in the early 20th century, the company has been at the forefront of developing cutting-edge technologies for cleaning, deburring, and strengthening metal surfaces. Over the years, Wheelabrator has continuously evolved and expanded its product range to meet the changing needs of different industries.
Today, Wheelabrator machines are recognized worldwide for their quality, reliability, and performance. They are used in a wide range of applications, including automotive, aerospace, construction, shipbuilding, and many other industries.
II. Types of Wheelabrator Machines
Wheelabrator offers a diverse range of machines to meet different surface preparation requirements. Some of the common types include:
1. Shot Blasting Machines
Shot blasting machines are the most widely used Wheelabrator machines. They use high-velocity steel shots or grit to clean and roughen metal surfaces. These machines can be designed for various applications, such as cleaning castings, forgings, and steel structures.
2. Tumblast Machines
Tumblast machines are ideal for processing small to medium-sized parts. The parts are tumbled in a chamber while being blasted with abrasive media, ensuring uniform surface treatment.
3. Hanger-Type Machines
Hanger-type machines are suitable for large and heavy components. The parts are suspended on hangers and passed through the blasting chamber, where they are blasted from all sides.
4. Roller Conveyor Machines
Roller conveyor machines are designed for continuous processing of long and large parts. The parts are conveyed on rollers through the blasting chamber, allowing for efficient and high-volume production.
III. Components and Working Principle
A typical Wheelabrator machine consists of several key components:
1. Abrasive Storage and Feeding System
This system stores the abrasive media (such as steel shots or grit) and feeds it into the blasting chamber at a controlled rate.
2. Blasting Chamber
The blasting chamber is where the surface preparation takes place. It is designed to contain the abrasive media and direct it onto the parts being processed.
3. Blast Wheels
Blast wheels are the heart of the Wheelabrator machine. They accelerate the abrasive media to high velocities and project it onto the parts, achieving the desired surface treatment.
4. Dust Collection System
A dust collection system is essential to remove the dust and debris generated during the blasting process. This helps maintain a clean working environment and ensures the safety of operators.
The working principle of a Wheelabrator machine is based on the impact of abrasive media on the surface of the parts being processed. The high-velocity abrasive particles remove contaminants, rust, scale, and old coatings, while also creating a roughened surface for better adhesion of paints, coatings, or other surface treatments.
IV. Applications of Wheelabrator Machines
1. Automotive Industry
In the automotive industry, Wheelabrator machines are used for cleaning and preparing engine blocks, cylinder heads, transmission parts, and other components. The surface treatment provided by these machines helps improve the adhesion of paints and coatings, ensuring long-lasting durability and corrosion resistance.
2. Aerospace Industry
The aerospace industry requires extremely high-quality surface finishes for aircraft components. Wheelabrator machines are used to clean and prepare turbine blades, engine parts, landing gear components, and other critical parts. The precise surface treatment helps ensure proper fit and function, as well as resistance to fatigue and corrosion.
3. Construction Industry
In the construction industry, Wheelabrator machines are used for cleaning and preparing steel structures, such as bridges, buildings, and storage tanks. The surface treatment helps remove rust and old coatings, providing a clean and durable surface for painting or other protective coatings.
4. Shipbuilding Industry
Shipbuilding is another industry that benefits from Wheelabrator machines. These machines are used to clean and prepare the hulls, decks, and other parts of ships, ensuring proper adhesion of anti-corrosion coatings and improving the overall lifespan of the vessel.
5. Foundry Industry
Foundries use Wheelabrator machines to clean castings of sand, oxides, and other contaminants. The surface treatment helps improve the appearance and quality of the castings, as well as preparing them for further processing such as machining or painting.
V. Benefits of Wheelabrator Machines
1. Efficient Surface Preparation
Wheelabrator machines offer highly efficient surface preparation, significantly reducing the time and labor required compared to manual methods. The high-velocity abrasive media can quickly remove contaminants and create a uniform surface finish.
2. Enhanced Adhesion
The roughened surface created by Wheelabrator machines provides excellent adhesion for paints, coatings, and other surface treatments. This helps ensure long-lasting durability and corrosion resistance.
3. Improved Product Quality
By removing contaminants and creating a clean and uniform surface, Wheelabrator machines help improve the overall quality of the products. This can lead to reduced rework and scrap, as well as improved customer satisfaction.
4. Versatility
Wheelabrator machines can be used on a wide range of materials, including steel, aluminum, cast iron, and many others. They can also handle various part sizes and shapes, making them highly versatile for different applications.
5. Environmental Friendliness
Many Wheelabrator machines are equipped with dust collection systems that help reduce dust emissions and improve the working environment. Additionally, the use of abrasive media can be recycled, reducing waste and environmental impact.
VI. Maintenance and Operation
Proper maintenance and operation of Wheelabrator machines are essential to ensure their long-term performance and reliability. Some key maintenance tasks include:
1. Regular Inspection
Inspect the machine regularly for signs of wear and damage. Check the blast wheels, abrasive storage and feeding system, dust collection system, and other components for proper functioning.
2. Lubrication
Lubricate the moving parts of the machine as per the manufacturer's instructions. This helps reduce friction and wear, ensuring smooth operation.
3. Abrasive Media Management
Monitor the abrasive media level and quality. Replace worn or contaminated media as needed to maintain optimal blasting performance.
4. Dust Collection System Maintenance
Clean and maintain the dust collection system regularly to ensure proper dust removal and prevent clogging.
In terms of operation, it is important to follow the manufacturer's guidelines and safety procedures. Operators should be trained on the proper use of the machine and understand the potential hazards associated with the blasting process.
VII. Future Trends and Developments
The field of surface preparation is constantly evolving, and Wheelabrator is at the forefront of innovation. Some of the future trends and developments in Wheelabrator machines may include:
1. Automation and Robotics
As the demand for increased productivity and quality control grows, there is a trend towards automating the surface preparation process. Wheelabrator is likely to continue developing robotic systems and automated solutions to meet this demand.
2. Energy Efficiency
With increasing concerns about energy consumption and environmental impact, there is a need for more energy-efficient surface preparation solutions. Wheelabrator may focus on developing machines that use less energy while maintaining high performance.
3. Advanced Materials and Technologies
The development of new materials and technologies may lead to improved surface preparation methods. For example, the use of advanced abrasive media or innovative blasting techniques could offer better results and reduced environmental impact.
4. Digitalization and Connectivity
The integration of digital technologies and connectivity in Wheelabrator machines could enable real-time monitoring, optimization, and remote control. This could improve productivity, reduce downtime, and enhance overall process efficiency.
VIII. Conclusion
The Wheelabrator machine is a powerful and versatile tool for surface preparation and finishing. With its advanced design, efficient performance, and wide range of applications, it has become an essential part of many industries. Whether it's cleaning and preparing metal components for painting, removing contaminants from castings, or strengthening surfaces for improved durability, the Wheelabrator machine offers a reliable and effective solution. As technology continues to advance, we can expect further innovations and developments in Wheelabrator machines, making them even more efficient, sustainable, and user-friendly.