Hotline
+86-136 8495 9862
Email:cennia@szmizhi.com
Add::104,Building 27,Third Industrial Zone, Longxi Community,Longgang District,Shenzhen,China.
Coil Forming & Handling Equipment
Surface Treatment Equipment
Solutions
Application
About Us
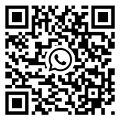
Welcome to MIZHI
For consultation/feedback, please call the service hotline: +86-136 8495 9862 Email:cennia@szmizhi.com
I. Introduction
A high - speed cut - to - length line is a crucial piece of equipment in various manufacturing industries. It is designed to accurately cut a continuous material, such as metal sheets, plastic films, or paper rolls, into specific lengths at a relatively high speed. This process is essential for meeting the precise requirements of end - products in industries like automotive, construction, packaging, and electronics.
II. Components of a High - speed Cut - to - length Line
Uncoiling System
The uncoiling system is the starting point of the cut - to - length line. It is responsible for holding and unwinding the large roll of material. For high - speed operations, the uncoiling system must be able to smoothly release the material without causing any sudden jerks or tension variations. It often consists of a mandrel on which the roll is mounted, and a motor - driven mechanism to rotate the mandrel at a controlled speed. In addition, there are often brakes and tension control devices. The brakes are used to prevent the roll from over - unwinding when the line stops suddenly, while the tension control devices ensure that the material is under a consistent tension throughout the uncoiling process. This is vital because inconsistent tension can lead to wrinkling or stretching of the material, which can affect the accuracy of the cutting process.
Feeding System
The feeding system takes over from the uncoiling system and is responsible for transporting the material at a constant speed towards the cutting unit. In high - speed cut - to - length lines, precision in the feeding speed is of utmost importance. The feeding system typically consists of a series of rollers. These rollers are carefully designed and manufactured to have a high - quality surface finish to minimize friction and ensure smooth material movement. Some advanced feeding systems also incorporate servo - motors, which can be precisely controlled to adjust the feeding speed according to the requirements of different cutting lengths. Additionally, sensors are often installed in the feeding system to monitor the position and speed of the material, and this information is fed back to the control system for real - time adjustments.
Cutting Unit
The cutting unit is the heart of the high - speed cut - to - length line. There are several types of cutting mechanisms that can be used, depending on the nature of the material being cut. For example, for metal sheets, shearing cutters are commonly used. These shearing cutters work by applying a large force to the material to cause it to fracture cleanly along a straight line. In the case of plastic films or paper, rotary cutters are often more suitable. Rotary cutters consist of a sharp - edged circular blade that rotates at a high speed and cuts through the material as it passes by. The cutting unit also needs to be highly accurate in terms of the cutting position. To achieve this, it is often equipped with a positioning system, which can be based on laser - guided technology or mechanical stops. The cutting force or speed also needs to be adjustable to handle different materials and thicknesses.
Stacking and Packaging System
Once the material has been cut to the required length, it needs to be stacked and packaged for further processing or shipment. The stacking system is designed to neatly stack the cut pieces of material. In high - speed operations, the stacking system must be able to handle the high volume of cut pieces without causing any misalignment or damage. It may use robotic arms or conveyor belts with specialized grippers to transfer and stack the pieces. The packaging system then encloses the stacked material in a suitable container, such as a box or a plastic wrap. This system also needs to be efficient, especially in high - speed cut - to - length lines, to keep up with the production rate.
III. Control Systems in High - speed Cut - to - length Lines
PLC - based Control
Programmable Logic Controllers (PLCs) are widely used in high - speed cut - to - length lines. PLCs are able to control multiple functions of the line, such as the uncoiling speed, feeding speed, cutting operation, and stacking process. They can be programmed to follow a set of predefined instructions based on the desired cutting lengths and production rates. For example, a PLC can be programmed to adjust the uncoiling speed based on the remaining roll diameter to maintain a constant feeding speed. It can also control the cutting unit to ensure that each cut is made at the exact specified length. PLCs are highly reliable and can operate in harsh industrial environments, which is essential for continuous production in manufacturing plants.
HMI (Human - Machine Interface)
The Human - Machine Interface is an important part of the control system. It allows operators to interact with the high - speed cut - to - length line. Through the HMI, operators can set parameters such as cutting lengths, production quantities, and line speeds. The HMI also provides real - time information about the status of the line, such as the current position of the material, the status of each component (e.g., if a roller is malfunctioning), and the overall production progress. Modern HMIs are often touch - screen based and provide a user - friendly interface, making it easier for operators to monitor and control the line even in high - pressure production situations.
Sensor - based Feedback Control
Sensors play a crucial role in high - speed cut - to - length lines. There are various types of sensors used, such as photoelectric sensors to detect the presence and position of the material, and load cells to measure the tension in the material. The data collected by these sensors is fed back to the control system (usually the PLC). Based on this feedback, the control system can make real - time adjustments to ensure that the line operates smoothly and accurately. For example, if a photoelectric sensor detects that the material is not in the correct position in the feeding system, the control system can slow down or stop the line to correct the position before resuming production.
IV. Applications of High - speed Cut - to - length Lines
Automotive Industry
In the automotive industry, high - speed cut - to - length lines are used to cut metal sheets for various components such as car body panels, engine parts, and interior trim. The accuracy of the cutting length is crucial as it directly affects the fit and assembly of these components. For example, the body panels need to be cut to precise lengths so that they can be welded together seamlessly during the assembly process. High - speed cut - to - length lines are also used to cut plastic films for automotive interiors, such as seat covers and dashboard covers. These films need to be cut to the correct size to ensure a proper fit and aesthetic appearance.
Construction Industry
In the construction industry, metal sheets are often cut to length for use in roofing, siding, and structural components. High - speed cut - to - length lines enable contractors to quickly obtain the required lengths of metal sheets, increasing construction efficiency. For example, when installing a metal roof, the sheets need to be cut to the exact length to fit the roof structure without any gaps or overlaps. In addition, in the production of pre - cast concrete elements, high - speed cut - to - length lines can be used to cut the formwork materials, such as plywood or plastic sheets, to the appropriate sizes.
Packaging Industry
The packaging industry relies heavily on high - speed cut - to - length lines. For example, cardboard boxes are often made from large rolls of corrugated cardboard. High - speed cut - to - length lines are used to cut the cardboard into the appropriate sizes for box - making. Similarly, plastic films are cut to length for use as packaging materials, such as shrink - wrap for products. The ability to cut these materials at high speeds is essential for meeting the high - volume production demands of the packaging industry.
Electronics Industry
In the electronics industry, high - speed cut - to - length lines are used to cut printed circuit boards (PCBs) and other thin - film materials. PCBs need to be cut to precise sizes to fit into electronic devices. The high - speed operation of these lines allows for efficient production of PCBs in large quantities. Additionally, in the production of flexible electronics, such as flexible displays and sensors, high - speed cut - to - length lines are used to cut the flexible substrates to the required lengths.
V. Challenges and Solutions in High - speed Cut - to - length Operations
Material Handling and Quality
One of the main challenges in high - speed cut - to - length operations is material handling. As the speed increases, the risk of material damage, such as scratches, dents, or wrinkling, also increases. To address this, the rollers in the feeding and uncoiling systems need to be carefully selected and maintained. High - quality rollers with low - friction coatings can help reduce the risk of material damage. Additionally, proper tension control is essential. If the tension is too high, the material may stretch or break, and if it is too low, it may cause wrinkling. Advanced tension control systems, such as load - cell - based feedback systems, can be used to maintain the correct tension.
Cutting Accuracy
Achieving high - cutting accuracy at high speeds is another challenge. The cutting unit needs to be precisely calibrated and maintained. For example, the blades in the cutting unit need to be sharp and properly aligned. In rotary cutters, any misalignment of the blade can lead to inaccurate cuts. Regular blade replacement and alignment checks are necessary. Laser - guided positioning systems can also be used to improve cutting accuracy, especially for materials where precise positioning is critical.
Line Synchronization
In a high - speed cut - to - length line, all the components need to be synchronized. The uncoiling, feeding, cutting, and stacking systems must work in harmony. Any mis - synchronization can lead to production delays or quality issues. To ensure synchronization, the control system, such as the PLC, needs to be carefully programmed. Timing belts and gears can also be used to physically connect the components and ensure that they operate at the correct relative speeds.
VI. Future Trends in High - speed Cut - to - length Lines
Automation and Robotics
The future of high - speed cut - to - length lines will see increased automation and the integration of robotics. Robotic arms can be used for more complex stacking and handling tasks, such as sorting the cut pieces according to different quality levels or packaging them in a more customized way. Automation will also reduce the need for human intervention, increasing production efficiency and reducing the risk of human error.
Integration with Industry 4.0
High - speed cut - to - length lines will be increasingly integrated with Industry 4.0 concepts. This means that they will be connected to the factory's overall network, allowing for real - time data sharing and remote monitoring. Operators will be able to monitor and control the line from a central control room or even remotely from off - site locations. This integration will also enable predictive maintenance, where sensors on the line can detect potential problems before they cause a breakdown, and the necessary maintenance can be scheduled in advance.
Advanced Materials and Cutting Technologies
As new materials are developed in various industries, high - speed cut - to - length lines will need to adapt. For example, the development of high - strength and lightweight materials in the automotive and aerospace industries will require new cutting technologies and cutting units that can handle these materials effectively. Laser - cutting technology may become more prevalent in high - speed cut - to - length lines as it offers high - precision cutting for a wide range of materials.
In conclusion, high - speed cut - to - length lines are a vital part of modern manufacturing. Their efficient operation, accurate cutting, and ability to handle various materials at high speeds contribute to the productivity and quality of end - products in multiple industries. As technology continues to evolve, these lines will continue to improve and adapt to meet the ever - changing needs of the manufacturing world.