Hotline
+86-136 8495 9862
Email:cennia@szmizhi.com
Add::104,Building 27,Third Industrial Zone, Longxi Community,Longgang District,Shenzhen,China.
Coil Forming & Handling Equipment
Surface Treatment Equipment
Solutions
Application
About Us
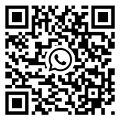
Welcome to MIZHI
For consultation/feedback, please call the service hotline: +86-136 8495 9862 Email:cennia@szmizhi.com
1.Name: 850MM Cut To Length Line
2.Cutting Material: Metal Coil
3.Cutter QTY: 1 set
4.The Max. Coil Width:850mm
What is cut to length line ?
A cut-to-length line (CTL line) is specialized machinery used in the metal processing industry to transform large coils of metal into specific lengths, providing a high degree of precision and efficiency. These lines are crucial in converting raw materials into usable components for various industries where exact dimensions are critical for the final product's integrity and performance.
The primary function of a cut-to-length line is to uncoil, level, and cut metal sheets to a predetermined length. This process is essential in industries such as automotive, construction, and electrical manufacturing.
Components of a Cut-to-Length Line
1.Uncoiler and Decoiler: The uncoiler, also known as the decoiler, is the starting point of the cut-to-length line. It holds the metal coil and feeds it into the line, ensuring a steady and controlled release of the coil.
2.Leveler or Straightener: Once the metal is uncoiled, it passes through a leveler or straightener to remove any curvature or waviness from the metal sheet, ensuring the material lies flat and is ready for precise cutting.
3.Feeding Mechanism: The feeding mechanism controls the flow of material through the cut-to-length line, ensuring consistent speed and alignment, which is crucial for accurate cutting.
4.Shear or Cutting Mechanism: The shear or cutting mechanism is where the actual cutting of the metal sheet takes place, with different types of shears suited for specific applications.
Applications of Cut-to-Length Lines
Cut-to-length lines are versatile and find applications across various industries, each benefiting from the precision and efficiency they offer:
1.Automotive Industry: Used for producing components like body panels, chassis components, and other structural parts.
2.Construction and Building Materials: Fabricating structural components such as beams, columns, and other elements.
3.Electrical and Appliance Manufacturing: Producing components like electrical panels, enclosures, and appliance housings.
Benefits of Cut-to-Length Lines
1.High Processing Speeds: Capable of cutting up to 500 feet of metal per minute.
2.Precision: Offers unparalleled accuracy in cutting metal sheets to the desired dimensions.
3.Versatility: Can process a wide range of metals, from steel to aluminum, and handle varying thicknesses.
4.Efficiency: Automated nature enhances production efficiency by minimizing manual intervention and reducing human errors.
5.Waste Reduction: Optimized to minimize material waste, ensuring maximum usable metal from each coil.
6.Just-in-Time Blank Production: Enables on-demand production of blanks, eliminating the need for large inventories of pre-cut blanks.
In summary, cut-to-length lines are indispensable in the metal processing industry, offering unmatched precision, efficiency, and versatility, essential for various industries to meet stringent specifications and maintain high-quality standards.
How does the automated nature of CTL lines improve efficiency in manufacturing?
The automated nature of cut-to-length (CTL) lines significantly improves efficiency in manufacturing through several key aspects:
1.Operational Efficiency: Automation in CTL lines allows for the continuous operation of processes such as uncoiling, leveling, shearing, and stacking, which enhances the overall operational efficiency.This streamlined process from maintaining supply levels to delivering end products minimizes manual intervention and reduces human errors.
2.Data-Driven Decision Making: Advanced automation solutions provide businesses with a holistic view of their operations, empowering them with data-driven decision-making capabilities.This leads to better strategic planning and quicker responses to operational inefficiencies.
3.Increased Productivity: Automation in CTL lines increases productivity by reducing production costs and improving the precision of the cutting process.The integration of computerized controls and automation systems ensures consistent, accurate results, which is crucial for maintaining the integrity of the final product.
4.Quality Assurance: Automation helps in maintaining the structural integrity of products by ensuring that they meet stringent regulations.The precision cutting offered by CTL lines reduces the likelihood of defects, which is critical for applications where minor deviations can lead to significant performance issues
5.Cost Reduction: While the initial investment in automation can be high, the long-term savings in labor, energy, and material costs are substantial.Automation reduces manual labor, leading to cost savings, and ensures precision and quality, which minimizes the need for rework and waste.
6.Enhanced Safety: Automation technologies take over dangerous tasks, significantly reducing workplace accidents and enhancing safety for employees.This is particularly important in metal processing, which can involve high temperatures and heavy machinery.
7.Predictive Maintenance: Advanced analytics and monitoring systems in automated CTL lines allow for predictive maintenance, reducing the likelihood of unexpected downtime and extending the lifespan of the machines.This ensures smooth operation and reduces capital expenditure on replacements.
8.Integration with Smart Manufacturing: AI and machine learning algorithms optimize production planning, predictive maintenance, and quality control, reducing downtime and waste.CTL lines can learn from their operations and make adjustments in real-time, leading to a significant reduction in material wastage and maximization of raw material utilization.
9.Sustainability: Automation in CTL lines contributes to sustainability by optimizing energy use and reducing waste.Energy-efficient components and closed-loop water systems reduce energy consumption and water usage, aligning with the industry’s commitment to environmental responsibility.
In summary, the automation of CTL lines improves efficiency in manufacturing by increasing productivity, ensuring quality, reducing costs, enhancing safety, and promoting sustainability.