Hotline
+86-136 8495 9862
Email:cennia@szmizhi.com
Add::104,Building 27,Third Industrial Zone, Longxi Community,Longgang District,Shenzhen,China.
Coil Forming & Handling Equipment
Surface Treatment Equipment
Solutions
Application
About Us
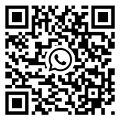
Welcome to MIZHI
For consultation/feedback, please call the service hotline: +86-136 8495 9862 Email:cennia@szmizhi.com
Definition
A Stone Shot Blasting Machine is a specialized industrial equipment designed to clean, texture, and prepare stone surfaces using abrasive media (such as steel shot or grit). This machine is widely used in the stone processing, construction, and restoration industries to enhance the appearance and durability of stone materials.
Working Principle
The Stone Shot Blasting Machine operates by propelling abrasive media at high speeds onto the surface of stones to achieve various surface treatments. The key processes involved are:
1.Loading:
Stones are loaded into the blasting chamber either manually or using an automated loading system. The stones are typically placed on a conveyor belt or a rotating table that moves them through the machine.
2.Blasting:
Inside the blasting chamber, high-speed blast wheels or turbines accelerate the abrasive media (such as steel shot or grit) and project it onto the stone surface. The impact of the media removes dirt, stains, and imperfections, while also creating a textured or smooth finish as required.
3.Media Recovery and Recycling:
The used abrasive media, along with debris and contaminants, falls to the bottom of the chamber. An elevator system lifts the mixture to a separator, where the reusable media is separated from the waste materials. The clean media is then recycled back into the blast wheels for reuse, reducing waste and operational costs.
4.Dust Collection:
A dust collection system captures and filters the fine particles and dust generated during the blasting process. This ensures a clean working environment and compliance with environmental regulations.
5.Unloading:
After the blasting process is complete, the treated stones are unloaded from the machine, ready for further processing, inspection, or installation.
Key Components
1.Blast Chamber:
A robust, enclosed chamber where the blasting process takes place. It is designed to contain the abrasive media and prevent it from escaping, ensuring safety and efficiency.
2.Blast Wheels/Turbines:
These components are responsible for propelling the abrasive media at high speeds. They are typically equipped with adjustable settings to control the intensity and direction of the blast, allowing for precise surface treatment.
3.Conveyor System:
The conveyor system moves the stones through the blast chamber. It can be designed to handle different sizes and weights of stones, ensuring smooth and efficient processing.
4.Media Recovery System:
This includes an elevator and a separator to collect and recycle the abrasive media. The system ensures efficient use of the media and reduces waste, lowering operational costs.
5.Dust Collector:
An essential component that captures and filters dust and fine particles generated during the blasting process. It helps maintain air quality and meets environmental standards.
6.Control Panel:
The control panel allows operators to monitor and adjust the machine's settings, such as blast intensity, conveyor speed, and media flow rate. Modern machines often come with advanced control systems for precise operation.
Advantages
1.Surface Preparation:
The machine effectively removes dirt, stains, and imperfections from stone surfaces, leaving them clean and ready for further processing or installation.
2.Texture Enhancement:
By controlling the blasting parameters, the machine can create various textures on stone surfaces, enhancing their aesthetic appeal and slip resistance.
3.Efficiency:
The automated process allows for high throughput, making it suitable for large-scale stone processing operations.
4.Environmental Compliance:
The inclusion of dust collection and media recycling systems ensures that the machine operates in an environmentally friendly manner, reducing waste and pollution.
5.Versatility:
The machine can handle a wide range of stone materials, including granite, marble, limestone, and sandstone, making it a versatile tool for various applications.
6.Durability:
Built with high-quality materials and components, the machine is designed for long-term durability and reliability, ensuring consistent performance over time.
Applications
Stone Shot Blasting Machines are used in a variety of industries and applications, including:
1.Stone Processing:
Used in quarries and stone processing plants to clean and texture stone slabs and tiles before they are sold or installed.
2.Construction:
Prepares stone surfaces for installation in building facades, floors, and countertops, ensuring a clean and uniform appearance.
3.Restoration:
Restores the appearance of old or weathered stone structures, monuments, and sculptures by removing dirt, stains, and moss.
4.Architectural Finishes:
Creates custom textures and finishes on stone surfaces to meet specific architectural and design requirements.
Maintenance and Safety
1.Regular Inspection:
Regularly inspect the blast wheels, conveyor system, and dust collector to ensure they are in good working condition. Replace any worn or damaged parts promptly.
2.Media Management:
Monitor the quality and quantity of the abrasive media. Replace or replenish it as needed to maintain optimal blasting performance.
3.Dust Collector Maintenance:
Clean and maintain the dust collector regularly to ensure it operates efficiently and complies with environmental regulations.
4.Safety Precautions:
Ensure that operators are trained in the safe operation of the machine and are equipped with appropriate personal protective equipment (PPE), such as gloves, safety goggles, and masks.
5.Environmental Compliance:
Regularly check and maintain the dust collection and media recycling systems to ensure they are functioning properly and meeting environmental standards.
In summary, a Stone Shot Blasting Machine is a versatile and efficient tool for cleaning, texturing, and preparing stone surfaces. Its ability to enhance the appearance and durability of stone materials makes it an essential piece of equipment in the stone processing, construction, and restoration industries.