Hotline
+86-136 8495 9862
Email:cennia@szmizhi.com
Add::104,Building 27,Third Industrial Zone, Longxi Community,Longgang District,Shenzhen,China.
Coil Forming & Handling Equipment
Surface Treatment Equipment
Solutions
Application
About Us
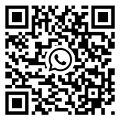
Welcome to MIZHI
For consultation/feedback, please call the service hotline: +86-136 8495 9862 Email:cennia@szmizhi.com
1.Name: Tumble Belt Blast Machines
2.Model:Q326
3.Manul Open Door
Tumble belt blast machines are industrial devices used for surface treatment of various workpieces through a tumbling and blasting process.
Here is a detailed description of these machines:
Structure and Components
1.Blasting Chamber: This is the core area where the actual blasting process takes place. It is typically constructed with strong profiles and thick steel plates to withstand the impact of the blasting media. The chamber is designed to optimize the blasting angle and distance, ensuring efficient coverage of the workpieces.
2.Tumble Belt System: The workpieces are placed on a continuously rotating rubber or steel belt, which tumbles and mixes them during the blasting process. This ensures that all surfaces of the workpieces are exposed to the blasting media. The belt is usually made of durable materials like high-resistance rubber or manganese steel to withstand wear and tear.
3.Blast Wheels/Turbines: These are responsible for propelling the blasting media at high speeds towards the workpieces. They are often equipped with wear-resistant components and designed for high efficiency and long service life. Some machines use multiple blast wheels to enhance the blasting capacity.
4.Abrasive Recycling System: After the blasting process, the used blasting media is collected and transported to a separator via a screw conveyor or an elevator. The separator, which may use advanced technologies like DISA & Pangborn, efficiently separates usable media from waste material, allowing for recycling and reducing costs.
5.Dust Collection System: To maintain a clean working environment and comply with environmental regulations, these machines are equipped with dust collectors. The collectors use cartridge filters to capture dust particles with high efficiency, typically around 99.9%. They also have features like silencers to minimize noise and easy-to-replace filters for maintenance.
6.Loading and Unloading Mechanisms: Depending on the machine type, workpieces can be loaded manually or through automated systems like skip loaders or belt conveyors. The loading capacity varies, with some machines able to handle several hundred kilograms of workpieces at a time. The unloading process is also automated in many cases, with vibrating conveyors or belt conveyors used to collect the blasted parts.
Working Principle
1.Workpieces are loaded into the blasting chamber, which is then sealed.
2.The blast wheels start rotating at high speed, propelling the blasting media (such as steel shot or grit) towards the workpieces.
3.The workpieces are continuously tumbled and mixed by the rotating belt, ensuring that all surfaces are evenly blasted.
4.The used blasting media and any debris from the workpieces flow out of the chamber and into the recycling system. The media is separated, cleaned, and then returned to the blast wheels for reuse.
5.Dust generated during the process is sucked into the dust collector for filtration, with clean air being released back into the atmosphere.
6.Once the blasting process is complete, the workpieces are unloaded, typically through an automated conveyor system.
Maintenance and Safety
1.Regular inspection and replacement of wear-prone components, such as the blast wheels and belt, are essential to ensure the machine's performance and longevity.
2.Safety interlocks and proper training for operators are crucial to prevent accidents and ensure safe operation.
3.Tumble belt blast machines are essential tools in various industries, providing efficient and effective surface treatment solutions for a wide range of workpieces. Their versatility, efficiency, and cost-effectiveness make them a valuable investment for many manufacturing processes.
Types and Variants
1.Batch Type Tumble Belt Blast Machines: These machines process workpieces in batches, with a stop-start operation. They are suitable for a wide range of applications and can handle various types of workpieces, from small plastic parts to large metal castings. Examples include the RMBC-S model, which is a compact system for batch processing of sturdy plastic parts.
2.Continuous Feed Tumble Belt Blast Machines: These machines allow for the continuous processing of bulk goods and workpieces with complex geometries. They typically have a higher capacity and are used in industries with high production volumes.
Applications
3.Foundry Industry: Used for desanding, decoring, and surface preparation of castings before further processing like welding or painting.
Forging and Heat Treatment: Effective for removing scale and burrs from forged or heat-treated parts, ensuring a clean surface for subsequent operations.
4.Plastic and Rubber Parts: Ideal for deburring and surface finishing of plastic and rubber components, providing a consistent and high-quality finish.
5.Automotive and General Engineering: Used for cleaning and surface treatment of various automotive parts and general engineering components.
Advantages
1.High Efficiency: The tumbling action ensures that all surfaces of the workpieces are evenly blasted, resulting in a high-quality finish.
2.Cost-Effective: The recycling of blasting media and the ability to process batches of workpieces make these machines economically efficient.
3.Versatility: Suitable for a wide range of materials and workpiece sizes, from small plastic parts to large metal castings.
4.Low Maintenance: Many models are designed with easy access to key components and low maintenance requirements, reducing downtime and maintenance costs.
5.Environmentally Friendly: The enclosed design and efficient dust collection system minimize environmental pollution.