Hotline
+86-136 8495 9862
Email:cennia@szmizhi.com
Add::104,Building 27,Third Industrial Zone, Longxi Community,Longgang District,Shenzhen,China.
Coil Forming & Handling Equipment
Surface Treatment Equipment
Solutions
Application
About Us
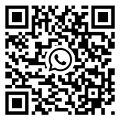
Welcome to MIZHI
For consultation/feedback, please call the service hotline: +86-136 8495 9862 Email:cennia@szmizhi.com
What is Coil Spring Shot Peening Machie ?
Coil Spring Shot Peening Machine is a specialized equipment used to enhance the fatigue strength and durability of coil springs through a process known as shot peening. Here's a detailed explanation of what a Coil Spring Shot Peening Machine is and its applications:
1.Process Description: The machine operates by bombarding the surface of the coil spring with small, pellet-sized shot at high velocity, which creates tiny dimples on the surface. This process induces a layer of compressive stress on the surface of the metal, which strengthens the metal and makes it more resistant to fatigue, corrosion, and cracking.
2.Applications: Coil Spring Shot Peening Machines are primarily used for shot peening suspension springs, valve springs, and leaf springs. The process is specially designed to increase the fatigue strength of components subjected to alternating stress, improving their fatigue fracture and stress corrosion fracture resistance, and enhancing the reliability and durability of the springs.
3.Key Benefits: The use of such machines results in lower production costs due to automatic operation, high output, and uniform quality. They feature high specific blast performance, ensuring parts are always shot peened in the hot spot of the blast stream, optimizing the blast effect. The machines are also energy efficient and maintain the shot operating mixture within the desired nominal size.
4.Technical Specifications: Some technical specifications of a Coil Spring Shot Peening Machine include the ability to handle workpieces with an outer diameter of φ100~φ260 and a length of 200~400. The average productivity ranges from 1.5~3.6m/min, and the abrasive used has a diameter of 0.8~1.2mm with a hardness of HRC ≥45. The machine includes two sets of Q063RKA blast wheels with a maximum shot blasting capacity of 2×300kg/min, and a motor power of 2×18.5kW.
5.Operation: The process involves an electrically controlled adjustable conveyor roller feeding the springs into the shot peening zone of the machine chamber. The entire surface of the springs is exposed to the accelerated peening media, where the high-velocity abrasive hits and rubs the surface of the springs, quickly detaching scale, rust layer, and dirt, and providing the surface with a certain roughness.
In summary, a Coil Spring Shot Peening Machine is an essential piece of equipment in industries that require high-performance springs with enhanced fatigue life and stress resistance, such as automotive, aerospace, and industrial machinery manufacturing.
Which industries use shot blasting more?
Shot blasting is widely used across various industries due to its effectiveness in surface preparation, cleaning, and finishing. Here are some of the industries that use shot blasting more extensively:
1.Automotive Industry: Shot blasting is extensively used in the automotive industry for cleaning and preparing surfaces of body panels, engine parts, and other components before painting or powder coating.
2.Construction Industry: It is used to clean and prepare structural steel before protective coating application and in the production of rebar.
3.Aerospace Industry: Shot blasting is crucial for cleaning compressor blades, deburring turbine blades, and other precision components that have strict surface requirements.
4.Metalworking Industry: The iron and steel working industries use shot blasting for descaling, stripping paint from older equipment, and removing rust and detritus.
5.Aviation: Shot peening is a critical step in airplane design, toughening key components to make them more resistant to damage or fatigue.
6.Rail Maintenance: Shot blasting is used in the preparation of rails and to prepare and strip trains for painting or regular mechanical treatment.
7.Energy Industries: Shot blasting is used for surface preparation before painting, applying powder coatings, or other treatments, especially in preparing pump rods, pipe coating, wind towers, and other on-site machinery.
8.Marine Industry: Shot blasting is used for corrosion removal, cleaning, and debris removal, especially on ships.
9.Military: Shot blasting techniques are used for cleaning key equipment, from individual car parts to intensive blasting for armored vehicles.
10.Masonry: Shot blasting is used to cut, abrade, or process stonework, particularly with natural stones like granite and marble.
These industries rely on shot blasting for its ability to improve the quality and longevity of metal products, ensure better adhesion of coatings, and prepare surfaces for further manufacturing processes. The use of shot blasting in these sectors highlights its importance in achieving high standards of surface finish and preparation
How does shot blasting differ from sandblasting?
Shot blasting and sandblasting are both surface preparation techniques that use abrasive media to clean or modify surfaces, but they differ in several key aspects:
1.Abrasive Media:
Shot blasting uses metallic shots or projectiles, typically made of steel or other metallic alloys, while sandblasting uses fine sand particles or other abrasive media such as crushed glass, aluminum oxide, or steel grit.
2.Surface Cleaning:
Shot blasting is generally more effective for heavy-duty cleaning tasks, such as removing heavy rust, coatings, or contaminants from surfaces.Sandblasting is typically used for lighter cleaning or surface preparation tasks, where a gentler abrasive action is sufficient.
3.Surface Profile:
Shot blasting is known for its ability to create a more precise and controlled surface profile. The impact of the metallic shots results in a uniform and well-defined texture or roughness on the surface.Sandblasting, while it can also create a surface profile, may produce a less uniform or predictable result due to the irregular shape and size of the abrasive particles.
4.Efficiency and Speed:
Generally, shot blasting is faster and more efficient than sandblasting. This is because the high-velocity impact of the metallic shots allows for rapid cleaning and removal of coatings or contaminants.
5.Environmental and Health Considerations:
Shot blasting produces less dust compared to sand blasting due to the reuse of metallic abrasives and integrated dust collection systems in the equipment.Sandblasting, especially when using silica sand, generates significant amounts of dust, which poses health risks like silicosis.
6.Cost and Maintenance:
Shot blasting equipment is typically more expensive due to its complexity and the use of durable materials.Sandblasting equipment is generally less expensive to set up, with simpler equipment and lower initial investment.
7.Material Suitability:
Shot blasting is best suited for hard and durable materials like steel, iron, and other metals. Sandblasting is suitable for a wider range of materials, including metals, plastics, glass, and wood.
In conclusion, the choice between shot blasting and sandblasting depends on the specific requirements of the project, the materials involved, and the desired surface finish. Shot blasting is ideal for heavy-duty applications and surface strengthening, while sandblasting offers precision and versatility for a wider range of materials and delicate surfaces.
What is shot blasting machine ?
A shot blasting machine is a type of equipment used for surface treatment of cast or forged metal products. It operates by projecting tiny abrasive particles at high speed against a metal product to clean or confer particular characteristics to its surface. Here's a detailed explanation of what a shot blasting machine is and how it works:
1.Operation Principle: Shot blasting machines use a centrifugal wheel to propel abrasive materials like steel shot and grit onto surfaces for finishing. The process uses centrifugal force, unlike sandblasting which relies on compressed air.
2.Applications: These machines are used in various industries for different purposes such as deburring, rust removal, scaling, general cleaning, and ceramic shell removal.They are also used to prepare surfaces for painting or coating, ensuring better adhesion.
3.Industrial Uses: Shot blasting machines are predominantly used in industrial settings and are essential for preparing metal surfaces for welding and finishing processes like painting or coating.They are also used in foundries for de-sanding, stripping, and preparing for cutting, welding, painting, metallization, or surface finishing of bronze and aluminum.
4.Types of Abrasives: The material used for shot blasting can include steel grit, shot-steel, copper shots, and aluminum pellets, among others.
5.Advantages: Shot blasting is generally more aggressive and efficient than sandblasting, making it suitable for treating tougher materials or removing thicker coatings. It is also considered less expensive and safer compared to other abrasive surface preparation methods.
6.Disadvantages: Shot blasting machines are not suitable for fragile products and can generate dust, which requires proper dust collection systems to prevent environmental pollution.
7.Environmental Considerations: Shot blasting machines often have a dust collection system to prevent tiny particles and dust from escaping into the surrounding environment, which also helps in recycling abrasives.
In summary, a shot blasting machine is an enclosed equipment designed for abrasive blasting for cleaning and preparing metal, stone, and other surfaces. It is widely used across different sectors for various surface preparation methods, including deburring, rust removal, and improving the durability of workpieces.
As we all know, the routine maintenance affects the shot blasting machine spanlife so much, even the same machine, if it is well maintained, the service life will be many years longer than the bad maintained situation. So what should we do for routine maintenance of the shot blasting machine?
1.Are the fixing bolts on the shot blasting wheel loose?
2.Whether the internal parts are worn?
3.Does the dust pipe leak air?
4.Is there any sediment on the blasting machine?
5.Whether each switch and indicator light are normal?
This is a giant and long catenary through shot blasting machine in our client's workshop. It consists of the work piece inlet & outlet chamber and the blasting chamber with 16pcs high-quality casted blast wheels placed at two sides of the blasting chamber. Our specially-designed wet Venturi dust collector was installed to have high efficiency of dedusting. The length of the hanging chain and the number of the hangers can be customized according to customer's workpiece productivity and efficiency requirements.
Usually, continuous hanging chain shot blasting machine needs a pit to have the lower part of the machine installed in the pit to save room but this will be done according to the local government policy of building a workshop.
Economic style solution with powerful capacity of cleaning thoroughly every side of work pieces that are suitable for tumbling. It is an ideal option for blasting and cleaning work pieces in batches to have optimum blasting results on small delicate metallic parts, heavy castings, partially covered with sand or scale.
Work pieces are loaded into the blasting chamber manually or automatically with loading & unloading system. In the process of blasting, work pieces are continuously cascading and tumbling over each other, resulting in all-around blasting coverage with high efficiency. Work pieces touch and contact each other during the tumbling make it even easier for blasting process.
Automatic loading and unloading system makes MIZHI tumble belt shot blasting machine a typical & optimized choice to have reliable quality, extremely long lifespan, high efficiency of blasting and save cost of labor.
MIZHI manufactures single-turntable and double-turntable version rotary table shot blasting machine, and both work with the main turntable. Hangers can be equipped on both single-turntable and double-turntable version to have easier and more thorough shot blasting work for hanging work pieces.
Multiple working stations can be designed on the main turntable to allow work pieces loading when at the same time other work pieces are in the blasting process to save time of working. This machine is an ideal solution for symmetric parts and the turntable can be programmed to stay at specific position to work with specific blasting wheel to have thorough surface cleaning of dissymmetric parts.
MIZHI rotary table shot blasting machine can handle work piece at max. weight 50KG for double-turntable version and up to 2000KG for single-turntable version and the maximum weight can be even higher. Work pieces are either loaded as a large single component for processing or hung on specific hanger on the turntable and rotated to the working stations for blasting process. It is usually used for medium casting and forgings, valves and petroleum drill etc.
MIZHI wire mesh belt shot blasting machines are specially designed for constant and continuous blasting of de-scaling, de-sanding, cleaning and pre-treatment for different type of medium & small work pieces with great processing capacity. It is especially suitable for work pieces in wide and flat shape. No crush among work pieces during blasting, great blasting capacity, high efficiency, guaranteed sealing system, compact design and easy loading and unloading, all these features make our wire mesh belt shot blasting machine an ideal option for many fields, such as automotive parts, forgings, castings, ship parts manufacturing, aerospace industry, aluminum alloy parts and machinery industry etc.
Wire mesh belt works as the carrier of work pieces in the wire mesh belt shot blasting machine and is available in two types: steel wire mesh belt & wear-resisting rubber wire mesh belt.
Our Advantages
*Top quality
The wire mesh belt, made of Mn 13 steel materials, is highly durable and wear-resisting and driven steadily and stably by the chain and chain wheel. The wire mesh belt transport system ensures efficient shot blasting on parts/components, including sand and die castings, profiled and flame cut and car body parts as well as machined work pieces, which may be too small for a roller conveyor shot blasting machine. Work pieces can be placed on the wire mesh side by side for constant & continuous blasting process to reach high efficiency, save abrasives and have with reliable performance of cleaning & dedusting.
Blasting machine body: 6-10mm thickness Manganese 13 steel plates well-welded in one piece and Manganese 13 steel protective boards, offering excellent wear resistance and protection from even the most aggressive blast media
*Smart designs
The position of the high-performance blasting wheels, ideally set at a vertical as well as at a horizontal angle on the blasting chamber, ensures that complicated surface areas of work pieces are fully reached by the blasting shots.
Ultimately compact design for easy operation and wide range of options of models to adapt to diversified production efficiencies and sizes of work pieces.
*All-around shot blasting machine
MIZHI wire mesh belt blasting machines are the best solutions for all-around continuous blast cleaning of flat, wide and complex shaped work pieces. This high flexible machine guarantees a high operational efficiency for a wide range of shot blasting applications, especially for deburring, blast cleaning, surface roughening, de-scaling and de-rusting.
*High-end technology applied
In front of the blasting chamber inlet, optical grating detecting device is installed to transmits time-lapse signal to the PLC as soon as the work piece goes into the blasting chamber to start the blasting process.
*MIZHI technique of sealing system
Blasting sealing: rubber segments are equipped at the roller conveyor inlet & outlet and the blasting chamber to keep the machine nearly 100% tight and prevent accidents of shot spillage.
*All-in-one control & operation center
PLC control, all process parameters of work pieces blasting can be configured and saved in PLC control unit, in the result that repeat input, repeat pushing different buttons are completely unnecessary. This means, much shorter time of parameter configuration, much less working hours of operator and high efficiency.
Smart communication with built-in 3D guiding technology UI and 7 Inch colorful touch screen for safe operation, easy maintenance.
*Care about environment
Great importance is attached by MIZHI to environment protection: noise and dust emission. We adopt high-end methods to reduce noise to 85DB and dust emission concentration to less than 50mg/m3 (these results can be even better with higher standard of configurations).
Range of applications
This is highly flexible system that can be applied in many applications such as de-scaling, de-sanding of forgings, castings, stamping parts, aluminum parts and heat-treated parts, rust removal, sand removal of iron, steel and metal castings, in fields of automotive vehicle, aerospace, railway and machinery etc. It is especially suitable for work pieces in wide and flat shape and pipes, wires and work pieces that are not suitable for tumbling.